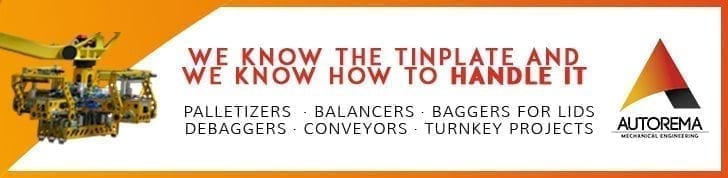
MANUFACTURE AND CHARACTERISTICS OF TINPLATE
This document develops in some detail the different stages in the manufacture of tinplate, from obtaining the base steel and its different varieties, to the successive sequences of tinplate tinning.
INDEX
Introduction
1.- Manufacture of steelN
1.1.- Manufacture of the base steel
1.2.- Manufacturing sequence
1.3.- Base steel composition
1.4.- Types of base steel
2.- Tinning
2.1- Tin
2.2.-Electrolytic tin plating
3.- TFS
INTRODUCTION TO TINPLATE
Tinplate is a material that although its invention comes from ancient times, it really reached its maximum development during the last century. It was the United States that was the driving force behind this industry, reaching its highest volume of activity in that country in the 1970s. Then, the great deployment of beverage containers, which in North America used aluminum as raw material, the use of alternative containers and the obsolescence of the American steel industry, caused the decline of this market.
The same did not happen in other parts of the world. Europe was able to modernise its steel industry in time, maintaining its competitiveness, and was thus able to successfully resist the challenge of aluminium. However, a wide variety of packaging options put a bit of a dent in the industry, which responded successfully with a series of mergers, enabling it to maintain an excellent level of technology.
Also in other geographical areas such as South America, the Far East and Asia, the market for tinplate and other coated products maintained a good market position.
Today it is still an important sector worldwide, although in continuous competitive struggle. It is therefore worth knowing a little about how this material is manufactured.
1.- MANUFACTURE OF THE BASE STEEL
Tinplate is normally by weight, 99% or more steel, and is therefore essentially a steel product. The manufacturing process actually starts in the blast furnace and tin smelter, but in practice it is considered to start from steelmaking. In fact, it is at this moment when the composition and type of steel ingot to be made is decided, defining its future use as a rolled product. Consequently, the basic raw materials for the manufacture of tinplate are steel and refined tin.
1.1.- Manufacture of the base steel.
There are two basic procedures for obtaining crude steel in liquid state: from (a) iron ore and b) scrap metal.
A.- From iron ore (smelting process): iron ore is a rock composed of iron oxides and various other minerals (gangue). The ores and scrap metals used in the smelting process are initially full of impurities. Iron is never in a pure state in nature; it is most often in the form of oxides and sulphides.
In the industrial process developed in the blast furnace, the aim is to obtain a product as rich as possible in iron, but other components will always appear in it. Among the parasitic materials, many have a lower combustion and evaporation temperature than iron, and will disappear by heating the ore, or have a lower density than iron, and will float on the melting metal. To free iron compounds in the form of ferrous (FeO), magnetic (Fe3O) and ferric (Fe2O3) oxides from oxygen, it is necessary to take advantage of the ease with which carbon reacts with oxygen.
Carbon in its combustion is a great devourer of oxygen, which will take it from the air, but also from the oxide to form the compounds CO and CO2 (carbon monoxide and carbon dioxide). In this operation, the excess carbon will leave traces of carbon combined with iron (3 to 6 %). This material produced in the blast furnace is called “melt”.
To get rid of the carbon, a complementary operation can be done by adding oxygen to form CO and CO2, carbon dioxide gases. This oxygen can also react with other elements contained in the melt, such as manganese forming manganese oxide (MnO), silica (SiO2), alumina (Al2O3)… All these operations are carried out first in the blast furnace and then, as we will see later, in the refining operation.
Summing up, we could say that in a blast furnace, after a stage of ore preparation in the agglomeration workshop, the iron is extracted in the blast furnace, with the help of a fuel: carbon (coke). Pure iron is not yet obtained, but iron smelting, a liquid mixture of iron (96%) plus carbon (3%) from the rest of the coke that has not been burnt, plus some residues (phosphorus, sulphur…) from the gangue. Figure 1 shows a vertical section of a blast furnace.
Figure 1: Schematic diagram of a blast furnace
B.- From scrap (“electrical process”): The components with which the furnace is fed can be from raw materials (e.g. machinery parts) duly selected, to scrap prepared, selected, crushed, calibrated, with a minimum iron content of 92%. The whole assembly is melted in an electric furnace.
Pig iron or iron from the blast furnace, or from scrap melted in an electric furnace, is an iron-carbon alloy, brittle and with a high content of the latter element. There may also be high sulphur and phosphorus content. Steelmaking is the process of refining, to reduce and control the percentages of elements other than iron, in order to produce ingots of the required purity, characteristics and malleability. In general terms, these elements and impurities are reduced by oxidation with iron oxide or oxygen, and removed by flotation with the addition of high melting point materials (e.g. limestone).
At present, four basic processes are used to obtain steel: the Siemens-Martin or open crucible process, the Bessemer or Thomas process, the top-blown oxygen process and the electric furnace. The latter is rarely used for the manufacture of tinplate. The first and the second are perhaps the most extensively used pneumatic procedures.
Open crucible” process – The crucible is usually charged with molten iron from the blast furnace, scrap and cold pig iron. The impurities are oxidized causing the formation of an oxidizing slag, and the fuel used can be liquid or gaseous. The capacity of a furnace of this type can be up to 400 tons and through the use of bulk oxygen, of relative economy, can have high performance, reaching up to 50 tons/hour. These ovens can be fixed or tilting.
Bessemer or Thomas process – In this system, the impurities are reduced by direct injection of air or oxygen through the molten metal by means of nozzles placed at the bottom of the converter. See figure nº 2:
Figure no. 2: Steel processing in the Thomas Converter
To burn the carbon from the melt, air or a mixture of air and oxygen is blown through the molten metal poured into the converter, which is a large steel retort with a capacity of 25 to 50 tons. The refractory walls of the converter are made of basic dolomite, untreatable to the lime that must be introduced to remove phosphorus from the melt. Productivity and quality can be improved by controlling the composition of the injected oxidizing gas, air, oxygen enriched air, oxygen, oxygen/carbon dioxide mixture, etc. For example, the VLN variant (very low nitrogen) not only increases production but also reduces the normally undesirable incorporation of nitrogen into the steel.
During the process several phases or periods can be distinguished. In the first period a lot of sparks are produced, caused by the combustion of the silicon which lasts from 2 to 3 minutes. In the second one, flames are generated by the combustion of carbon, with a persistence of 10 to 12 minutes. In the third is characterized by the expulsion of gases caused by the subsequent blowing and combustion of the phosphorus, its interval is 3 to 5 minutes.
Throughout the process, different solid elements are usually added, such as: lime, scrap, ferro-manganese or specular pig iron, depending on the needs.
There is a system called Duplex, which applied to the manufacture of tinplate steel, means the combination of the Bessemer acid process with the basic open crucible process. In the converter the main purification takes place, while in the second part of the process the phosphorus reduction takes place.
Superior oxygen injection process. The Bessemer process is widely used mainly because of its low installation cost and flexibility of operation, but it has great limitations in terms of final quality, as it requires a raw material with high phosphorus content and restrictions on the use of scrap. These difficulties strongly affected some manufacturers, which led to the development of superior oxygen injection processes, which allow to obtain steels of good and constant quality, with low nitrogen and high or low phosphorus content, according to needs. There are three systems widely used for laminated materials and they are called LD, DDAC and KALDO.
The LD process was the first one based on the availability of oxygen in large quantities. It consists of replacing the injection of air from the bottom of a Bessemer converter by the injection of a jet of oxygen at high pressure from the top, which produces a strong agitation, and therefore a very rapid oxidation of impurities. It is a fast and efficient process, with initial investments not much higher than with the Bessemer process, it reduces maintenance problems and produces a material with low nitrogen content, being one of its limitations the use of low or medium phosphorus content irons. This system was developed by two companies located in Linz and Donawitz. From the initials of these cities comes the name of the LD process.
DDAC is exactly the same process as above, except that lime is injected along with the oxygen. It is a technology of French origin
The KALDO process was first developed in Sweden and uses a rotating and tilting crucible or kiln, with the application of an oxygen jet at the top and the addition of lime by injection or in chunks.
Oxygen processes are versatile and allow the use of reasonable amounts of ore and scrap, producing low phosphorus and low nitrogen steel with good mechanical characteristics.
Casting of the steel – Once the steel has been obtained by one of the procedures described above, while it is still in the converter and in a liquid state, it must be transformed into a solid state by casting it. Industrially there are two casting processes. The most classic in which it can be converted into ingots (“ingot casting”) or follow the “continuous casting” procedure.
Ingot mould casting – This is the conventional procedure. By means of a ladle the molten steel is poured into ingot moulds, which once cooled give rise to manageable ingots with which the following operations are fed.
Continuous casting – This is the most modern process for the manufacture of plates. It has the main advantages of producing very high quality semi-finished products, it allows lower production costs, and increases the productivity of the steel mill. In fact, thanks to this system, the operations are fewer and simpler than in ingot mould casting. . It is banishing the use of ingots for steels intended for rolling. See figure nº 3:
Figure no. 3: Continuous casting
In continuous casting, the contents of the converter are poured by means of a ladle in a regular and uninterrupted manner into a cooled bottomless ingot mould with a cross-section that corresponds to that of the desired plate. It then passes through a series of rollers for flattening, and finally by means of an oxy-fuel torch the sheets are cut to the desired length. In this way we obtain slabs (slab) of length between 5 to 20 meters, width up to a little more than one meter and thickness of about 20 cms.
1.2.- Manufacturing sequence.
Figure nº 4 presents a sequence of the different operations or phases in the production of the steel plates that will be the basic raw material in the tinplate manufacturing plants.
Figure no. 4: Fabrication of steel plates
When the ingot casting process has been used, once the steel has been melted into ingots, the first operation carried out is the rolling of the ingot to turn it into a slab. This operation is usually carried out in reversible, double-high rolling mills. The so-called Universal type, have cylinders or side rollers that work simultaneously the 4 faces of the ingot, eliminating the operation of rotating the ingot on its axis during this stage.
The final product of this operation, the slab, is 125 to 230 mm thick, the approximate width of the tinplate that is finally desired, and a length that depends on the size of the original ingot.
The slabs generated both by continuous casting and by ingot rolling are prepared for treatment in hot rolling.
Hot rolling is the next step, although there is usually an intermediate stage, which consists of cooling and storing the plates, a selection process, a surface preparation (scarfing) and a heating of the plate to a suitable temperature for rolling. Eliminating this intermediate stage requires a very precise programming, and a very high technological capacity, which ensures the absence of defects in the plates or slabs. Figure nº 5 shows the different phases of hot rolling.
Figure no. 5: Hot rolling process
The surface preparation is carried out in the “descaling machine”, in which the plate is subjected to a detachment of iron oxides and impurities, which is achieved by means of a weak rolling pressure, detaching them by the action of water at high pressure. The plate is heated to a temperature of 880º C. It is necessary to remove this layer of oxides because it damages the laminate, as it causes rapid wear of the cylinders, streaks on the metal, oxide incrustations and other manufacturing defects (breaks, slipping, folds…).
The hot rolling mill reduces the sheet to a continuous strip of about 2 mm thickness. It normally consists of two sections, a roughing section and a finishing section. It can be of a continuous or reversible type, depending on the capacity of the installation, etc.
The roughing mill usually consists of 4 to 6 boxes that reduce the initial thickness of the plate by 25 to 50% per box. The finishing train has 4 to 7 boxes, again reducing the thickness by 25 to 30 % per box, except for the last one which only reduces by 10 %. The maximum speed of this operation can be in the 100km/h. At the exit the material is at 850º C. It proceeds to a cooling by water curtain up to 590º, forming coils with the same.
The coil produced must be pickled and lubricated before cold rolling. This operation is usually carried out in a succession of tanks containing hot dilute sulphuric acid (close to 100º C), washed, dried and lubricated with palm oil or other lubricant suitable for cold rolling. The pickling line is normally fitted with a circular cutter, which cuts the edges, thus ensuring that they are suitable for cold reduction or cold rolling, also setting the maximum width of tinplate to be obtained and also the one that will give the best economic results. See figure nº 6.
Figure No. 6: Cold rolling, annealing and skin-pass rolling of base steel
The next operation is cold rolling, which can be done in continuous (tandems) or reversible mills. Lubricants and coolants are used during this operation, and the resulting thickness is very close to the desired finish. The reduction is therefore of 1.8 or 2 mms to a measure between 0.15 to 0.3 mm approximately according to the final size of the tinplate to be produced.
The coil obtained is made of a very hard material and subject to strong tensions, and needs a suitable treatment to give it the necessary machinability, causing a recrystallization of the steel. This treatment is called annealing and involves heating the metal in a reducing atmosphere to avoid any oxidation (mixture of nitrogen and hydrogen) and can be done continuously (continuous annealing) or in batch annealing furnaces (batch annealing).
Continuous annealing: The strip circulates through a furnace at a temperature of 630º C, with each point of the material remaining in the furnace for a minimum of 1.5 minutes. Continuous annealing has a number of advantages and disadvantages such as:
Advantages:
– Reduction of materials “in process” of production.
– Reduction of manufacturing lead times.
– Improvement of the quality of the manufactured products:
o Constant and continuous heating along the entire length of the coil, which results in more homogeneous mechanical properties.
o Fast cycle, obtaining fine equiaxial grains, therefore an isotropic metal and superior mechanical properties, such as improvement of the elastic limit.
o Better corrosion resistance. The fast cycle does not allow elements such as carbon, manganese, phosphorus… to move to the surface of the material as happens in the base or bell annealing.
o Allows the use of a MR type steel composition, less loaded with hardening elements: carbon, manganese-…. (continuous annealing = 0.08 % carbon, base annealing = 0.10/0.13 % carbon) which favours operations such as welding, specialties…
Disadvantages:
– Manufacturing:
o Difficult programming of the orders, since the maximum variation in width between consecutive coils is of the order of 50 mm, and in thickness of the order of 10 %.
o Delicate conduction of the line. Risk of belt breakage in the oven. It is an important stop. The elastic limit of the strip at the annealing furnace temperature is low (approx. 30 N/mm2).
o Impossibility of line stops.
– Use:
o Fine crystallography that generates a less ductile metal, with weak anisotropy, which impairs drawing.
o Risk of presence of Lüder lines.
Annealing in a bell: Several stacked coils are covered with a bell in a reducing atmosphere at a temperature of 680º C for at least 85 hours, divided into 32 hours of heating, 34 hours of cooling under a bell up to 170º, and 19 hours of accelerated cooling in the open air. See figure nº 7
Figure nº 7: Diagram of the bell annealing process.
In both cases it is essential to previously eliminate the residues of the lubricating and cooling agents previously used, being the method used for this, consistent with the type of annealing to be done, normally by electrochemical means, such as a bath of degreasing agent heated to 95 ºC or mechanical, with brushing on both sides.
Next comes the tempering operation, surface treatment or finishing (temper rolling or skin-pass). It is made by means of a reduction or lamination, without lubricant and very light, which usually does not exceed 2% in thickness. For this purpose, a rolling mill consisting of two boxes is used. The strip, when passing between the cylinders under the effect of the established pressure and traction, undergoes a superficial modification of the structure, achieving an increase in the hardness of the surface layer, but preserving the internal softness.
In short, this operation gives the strip the desired hardness, a good flattening and a surface finish of the material depending on the roughness of the rolls used in the rolling mill boxes. Combining the surface finish of the cylinders of the boxes of this lamination, and the final remelting of the tin after the tinning operation, different surface finishes of the tinplate are achieved. The main types of finishes are:
Glossy finish: To achieve this finish, it is essential to obtain a mirror polish on the cylinders. In addition, it is necessary to apply the tin plating refusion. This type of finish is, together with the stone, the most requested.
Stone finish: The cylinders undergo two grinding passes with a special grain grinding wheel, which gives the product a striated appearance. As in the previous case, the tin coating is remelted, which also ensures brilliance.
Matte finish: It has a low reflective surface. To achieve this, the cylinders are shot-blasted and the remelting operation after tinning is omitted.
In the case of double reduced tinplate, the last size reduction is made by replacing the tempering operation with a further size reduction or rolling of approximately 33%, with the consequent lengthening of the material by a similar percentage, this time using surface lubricants. This gives the tinplate high mechanical properties with a small thickness.
It is common practice to prepare the coils prior to the tinning operation. It consists mainly in cutting the edges and eliminating the sections of low quality or out-of-spec calibre, forming coils of optimum size for the tinning line.
In electrolytic tin plating, the prepared material passes continuously through the operations of electrolytic cleaning, electrolytic pickling, electro-deposition of tin, tin remelting (flow-melting), passivation treatment and lubrication. After this series of operations, the product can be cut into sheets to the ordered size (length, as the width was given when preparing the coils), inspected, sorted and packed; or it can be wound for shipment to the customer or for slitting, etc. on a separate slitting line. It is normal to carry out on the same line, the selection of the material, before packing. We will return to these points in more detail later.
1.3.- Composition of the base steel.
For tinplate, the base steel is essentially a mild steel of low carbon content, with a generic composition of the following type:
– Carbon 0.04 – 0.15 %.
– Silicon 0.08 % maximum
– Sulfur 0.015 – 0.05 %.
– Phosphorus 0.01 – 0.14 %.
– Copper 0.02 – 0.20 %.
– Manganese 0.20 – 0.70 %.
– Nitrogen 0.001 – 0.025 %.
Due to the use of scrap in steelmaking, other elements such as nickel, chromium and tin may be present, but no other elements are intentionally added. The only exceptions are phosphorus and nitrogen, which can provide special properties. The use of copper to increase corrosion resistance, and of some carbides to control ageing has fallen into disuse.
The influence of some elements on the base steel of tinplate is given in outline in the following paragraphs.
– Carbon: Carbon increases yield strength, tensile strength and hardness, decreases elongation and ductility. Within the usual limits for tinplate, variations in the content of this element are of little importance, as other elements have a much greater influence.
– Silicon: It exists in tinplate as a residual element, very rarely is it added as a deoxidising agent. Slightly hardens and in some cases adversely affects corrosion resistance.
– Sulphur: In this type of steel, the effects of sulphur are counteracted by manganese, which is always present. However, due to its consequences on ductility, surface quality and corrosion resistance, every effort is made, within economic limits, to reduce it to the minimum possible.
– Phosphorus: It is an element that highly influences hardness and corrosion resistance. When there is a possibility of acid corrosion, it must be kept within certain limits, and the content is increased when greater steel strength is required and there is no danger of corrosion.
– Copper: Although it increases resistance, it does not do so effectively within the usual limits. Exceeding these limits increases atmospheric corrosion resistance, but may reduce internal corrosion resistance, so for most types of tinplate, a maximum copper content is specified.
– Manganese; It is used in the manufacture of steel for tinplate, mainly to react with other elements, mainly sulfur, rendering them inoperative.
– Nitrogen: In Bessemer steels, it is a normal constituent element in percentages higher than 0.01% and has always been considered a disadvantage. Subsequently it has been found that its intentional addition greatly increases the strength of the steel without appreciably modifying the corrosion resistance, although it may affect ageing. The development of oxygen processes (LD, etc.) has made it possible to accurately control the content of this element, giving a uniform and continuous quality.
– Nickel: At permitted levels, it does not affect the physical or mechanical properties of tinplate, but it does affect the chemical properties, especially corrosion in certain types of packaging. The same is true for chromium.
– Tin: This element has a high solubility in iron or steel, and percentages higher than 10% are necessary for a second phase to form. At normal levels it has no effect on the metallographic structure. Its presence progressively increases the elastic limit and the tensile breaking limit, with a reduction in the modulus of elasticity. It is important to note that small amounts of tin, in steels containing copper, can cause serious difficulties in hot working the steel.
In steelmaking, practical rules are sometimes used to calculate the effects of alloying and residual elements on the mechanical properties of tinplate steel. One of the most common is the Strohmayer index, which is calculated by multiplying the nitrogen content by 5, adding the phosphorus and multiplying the sum by 1000.
1.4.- Types of base steel
Traditionally there are three basic types of tinplate steel, although with today’s technologies it is sometimes difficult to stay within the classic types. These are:
Type L: It is a cold rolled steel, coming from open crucible furnaces (Siemmens Martin). It has a low content in metalloids and residual elements, especially limited in phosphorus, with the following composition:
Carbon 0.05 – 0.13 %.
Manganese 0.30 – 0.60 %.
Sulphur 0.04 max.
Phosphorus 0.015 max.
Silicon 0.010 max.
Copper 0.06 max.
Nickel 0.04 max.
Chromium 0.06 max.
Molybdenum 0.05 max.
Arsenic 0.02 max.
Nitrogen 0.02 max.
It is used when a high resistance to very corrosive products is required.
Type MR: It is the most used. It is of the same origin as the previous one, cold rolled and used in moderately corrosive products. Your analysis is:
Carbon 0.05 – 0.15 %.
Manganese 0.30 – 0.60 %.
Sulphur 0.04 max.
Phosphorus 0.020max.
Silicon 0.010 max.
Copper 0.20 max.
Type MC: It is a steel made in Bessemer converter or Siemmens Martin furnace, used when the resistance and the content of the container is of low corrosiveness. Your sample analysis is as follows:
Carbon 0.05 – 0.15 %.
Manganese 0.25 – 0.60%.
Sulphur 0.04 max.
Phosphorus 0.03 – 0.15 %.
Silicon 0.010 max.
Copper 0.20 max.
There are also some special steels such as type D, aluminium quenched and tempered, used in specific cases of deep drawing.
Generally manufacturers in Europe have been forced to try to eliminate specialised tinplate productions and thus find economical and competitive procedures, so they try to simplify the problem.
Also important from the point of view of corrosion resistance is the surface of the steel, which depends in part on the type of atmosphere used during annealing. An atmosphere containing nitrogen, hydrogen, carbon dioxide and water vapour produces a less resistant tinplate than a dry nitrogen containing 4 to 8% hydrogen. Also dissolved tin ions have in general an inhibiting effect on the corrosion of tinplate by some products.
2.- TINNING
2.1.- Tin
When this material is intended for the manufacture of tinplate, it is logical to think that it will be in prolonged contact with foodstuffs and must therefore meet certain requirements in terms of impurities. The American Society for Testing and Materials (ASTM) classifies into five groups, each with minimum tin contents as follows: grade AA = 99.98 % tin, A = 99.80 %, B = 99.7 %, C-1 = 99.0 % and C-2 = 99.0 %. The minimum specified for the manufacture of tinplate is grade A. Its analysis is:
Tin (minimum) 99.80 %.
Antimony 0.04 %.
Arsenic 0.04 %.
Bismuth 0.015 % Bismuth 0.015 % Bismuth 0.015 % Bismuth 0.015
Copper 0.03 %.
Iron 0.015 % Iron 0.015 % Iron 0.015 % Iron 0.015 % Iron 0.015
Lead 0.05 %.
Nickel and Cobalt 0.015 %.
Silver 0.01 % Silver 0.01 % Silver 0.01 % Silver 0.01 % Silver 0.01 % Silver 0.01
Sulfur 0.003 % Sulfur 0.003 % Sulfur 0.003 % Sulfur 0.003
Zinc 0.001 % Zinc 0.001 % Zinc 0.001 % Zinc 0.001 % Zinc 0.001
Cadmium 0.001 %.
Aluminum 0.001 %.
- 2.- Electrolytic tinning
The development of this tinning process was one of the most important steps in the tinning industry. The electro-deposition of tin on a continuous narrow strip (strip), started in Germany in 1930, but it was during the 2nd World War when the technique was developed intensively, mainly in the USA, due to the shortage of tin.
There are a number of technical and economic reasons that made electrolytic tinplate take the market away from coke tinplate or hot tinplate, which was the traditional way of obtaining it. One of the most important is the precise control of the amount of tin deposited and the uniformity in thickness. Another is the availability of differential electrolytic tinplate, which consists of applying different thicknesses of tin coating on each side of the sheet.
As we have already indicated in the base steel tempering operation, electrolytic tinplate can be produced in various finishes, although three are the most common. “Bright”, which is the most common, “matt” which consists of tinning base steel with a rough surface and then not remelting the tin and finally “stone” which is the same finish as above but remelting the tin, which gives a shiny finish but not reflective.
The manufacturing methods are basically two, acid and alkaline or basic process, but the latter has two variants of wide use, horizontal halogen lines and alkaline or vertical lines. There is a fourth procedure, which uses fluoborates as electrolyte, but it is very little used.
The lines that use the acid process are the ones that produce the highest percentage of electrolytic tinplate. They are often called Ferrostan, as this was the name registered by U.S. Steel for its tinplate, with many subsequent licensees of its technology around the world.
Electrolytes are the most delicate part of every process. For example, in acid lines, it is a solution of stannous salts in acid, but the good performance as an electrolyte depends on the various additives used which have three main objectives, to avoid oxidation, to favour the formation of compact and non-fuzzy deposits, and to improve wettability.
Some classic advantages of using alkaline electrolyte are having a simpler, easier to handle and non-corrosive electrolyte in relation to steel, which reduces the initial cost of the equipment. The preparatory section is also simpler.
Acid lines have the advantage of using less current for tin plating than alkaline lines, less anode surface area is required and the electrical efficiency is higher in electrodeposition. However, alkaline lines produce a tinplate with better corrosion resistance characteristics.
Broadly speaking, the three types of lines are made up of the following sections:
Unwinding
Preparation
Tinning
Finishing
Cutting – winding – packaging
The entry or unwinding section has the necessary equipment for the handling of the black sheet coils, and for the continuous feeding of the line, by cutting the beginning and end of each coil and the electric welding of the end of one with the beginning of the next. Includes guide and feed rollers, tension rollers, etc.
Between the unwinding and preparation section, there is a device for storing black plate strip, intended to accumulate a certain amount of strip, which feeds the line while the coil is being changed and spliced in the previous unwinding section. There are several types, predominantly well and “accordion”.
The preparation section has two main objectives, cleaning (degreasing) and pickling. The first one is the removal of all residual elements on the belt surface, coming from lubricants, cooling agents, etc., while the second one aims to remove the iron oxide adhered to both sides of the belt.
The treatment is carried out in a succession of chemical or electro-chemical baths, with alternating water jet and/or steam washes. The layout and type depends on the line. For example, degreasing is normally done in a detergent or alkaline solution and in lines of this type it is eliminated or reduced because degreasing is done automatically in the tinning section.
The tinning section differs completely in each process, being that of the halogen process the one that occupies the largest surface, since the strip moves flat, normally in 3 levels, while in the other two systems it follows a sinusoidal or serpentine shape.
Figure no. 9: Tinning line, electrolytic tank and anodes
Before tinning, the marks corresponding to the differential tinplate are made on the black plate strip, when it is this type that is manufactured, therefore these marks go on the base steel. Some manufacturers may mark the base steel so that in the event of later difficulties with the tinplate, the manufacturer can be identified. These marks are not visible on the leaf as such, they must be found in the laboratory.
The finishing section includes different steps, the main ones being: remelting, passivation and lubrication.
The purpose of remelting is to give a shiny finish to the tinplate, as the simple electro-deposition of tin produces a micro-rough surface with a matt appearance. However, this step is of fundamental importance for tinplate intended to be in contact with corrosive elements. During remelting, a layer of iron-tin alloy is formed, and because of the rapidity with which it is produced, the thickness is very thin. It follows that dull tinplate, which has not undergone remelting, should not be used for those purposes which require the presence of a layer of iron-tin alloy.
Passivation is a characteristic of electrolytic tinplate. In this case, especially in low coatings, it is convenient to provide it with a protective layer that avoids oxidation, not only during manufacturing, but also in subsequent operations, such as varnishing. It is also necessary to give a surface chemically more suitable for lithography and varnishing, and of a certain protective hardness. Passivation is intended to cover this aspect, and basically consists of forming a chromic oxide layer. The methods used are various chemical or electro-chemical methods, each designed to obtain special characteristics. They are usually known by the acronym USS and a three digit number, the first digit indicates the type of solution (1 = chromic acid, 2 = chromium phosphate, 3 = sodium dichromate, 4 = sodium carbonate), the second digit indicates the polarity of the tinplate in the solution (0 = non-electrolytic, 1 = cathodic, 2 = cathodic/anodic) and the third digit refers approximately to the level of current used.
There are three basic types of passivation, which are:
– Passivation 300: It is obtained by chemical procedure, by immersion in sodium dichromate solution, generating a layer of chromium oxide. It gives good results from the point of view of varnish adhesion. It offers weak protection against sulphuration. This passivation is however unstable. Its effectiveness decreases over time
– Passivation 311Electroplating: Obtained by electrochemical process by electrolytic deposition in a bath of sodium dichromate of a layer of chromium and chromium oxide. It is the most commonly used passivation. It has convenient yields from the point of view of varnish adhesion, although lower than the 300 passivation. It is much more stable over time than the 300. It can therefore be considered a compromise between the stability over time and the quality of adhesion of lithographic systems.
– Passivation 312: It is obtained by the same system as 311. It is in fact a reinforced 311 passivation. It is mainly used for tinplates that must resist sulphur products, such as meats, soups, products for dogs and cats… Its adhesion to inks and varnishes is inferior to 311.
The different passivation treatments not only affect the adherence of varnishes, welding, etc., but also produce various forms of attack or staining, as the tinplate is subjected to contact with corrosive products or sulphur compounds. Even from an aesthetic or presentation point of view, this detail is important, for example with condensed milk.
Finally, the finishing section performs the lubrication operation. The purpose of this lubricant is not so much to protect the tinplate itself, but the passivation and not to counteract the properties of this is very light, so the most commonly used method of application is by electro-deposition, although it can be done by spraying or immersion. Three types of oil are normally used, cottonseed oil, dioctyl sebacate and dibutyl sebacate, the latter being the most common. The normal amount of lubricant is in the order of 0.005 grs/m2. The lubricant is usually dried by means of steam and hot air coils.
The last part of the line depends on the formation of the final product and the productivity to be obtained, rather than the type of line (acid, …). If the production is exclusively in coils, there will be no cutting but there will be a storage device for the band, to allow the change of coils. If the production is exclusively in cut sheets, the storage device is not necessary. In the cutting operation, the selection of surface defects is made, this control is not very efficient due to the speed of the line, so the product obtained is classified as “unassorted” (unassorted). If you want to separate “firsts” from “seconds”, you need to use the auxiliary services of a selection line. It is in this section that off-spec and pin hole sheets are separated. When coils are delivered, it is normal not to make this separation, which decreases the yield, and it is up to the customer to do this operation when cutting. The quality “unselected” is defined as a normal product of an electrolytic tin plating line.
An electrolytic tinning line has a very complex auxiliary equipment, more complex in fact than the line itself, something similar to icebergs happens, you can’t see the sunken part. Electrical and electronic equipment, controls, pumps, electrolyte tanks, purification equipment, water and steam systems, air, etc., are of great importance and are normally installed underground. The installed electrical power is also very strong.
The strip speed during tinning is a function of the electrical current available for electrolysis, the condition of the electrolyte, the size and thickness of the material, the tin deposition desired and other factors.
3.- TFS
As a consequence of the increase in the price of tin and the risk of seeing the sources of supply of tin in danger, during the last third of the last century a substitute product for tinplate was developed, the TFS or chrome-plated sheet. This material soon aroused an interest that has increased over time. Its advantage lies in the fact that it is a perfectly valid option for the manufacture of lids, bottoms, accessories and deep-drawn containers, and slightly cheaper than tinplate.
The TFS is made of a support identical to that of tinplate: steel. Although protection is assured, not by a light layer of tin applied by electrolytic deposition and by a passivation film, but by a mixed coating of chromium and chromium oxide.
In the steel industry it is common to produce TFS on a mixed installation, which can produce tinplate or chrome plate with a series of not very complex changes, which are carried out in a moderate time. The application of chromium is also carried out by electrolytic system. Figure 10 shows the special part of a line for the production of chrome-plated sheet metal.
We do not go into detail in the process of obtaining it, because as we have already indicated the base steel is the same as for tinplate, and the coating line follows a sequence analogous to that of tin plating.
Finally, it is worth mentioning the important participation of the large packaging companies in the developments in the manufacture of steel for tinplate, in the manufacture of tinplate itself, in other alternative materials such as TFS, and of course, in its use.
We have an inquiry to get your offer Price per ton for supplying Standard grade electrolytic tinplate according to EN 10202:2001 (or equivalent) for welded aerosol cans (bottoms – Tops – Bodies) having the following properties:
– Item(1):
Tinplate Sheets En 10202-TS 245 – BA – BR – 2.8/2.8 – SP – 311
Dimensions(mm): 0.33 x 780 x 745
Hardness(HR30T): T52 BA
Type of steel: B
Usage: varnished and lacquered aerosol cans domed tops.
– Item (2)
Tinplate Sheets En 10202-TH 435-CA –BR 5.6/2.8D -SP -311
Dimensions(mm): 0.26 x 887 x 820
Hardness(HR30T): T65 CA
Type of steel: B
Usage: varnished and lacquered aerosol cans bottoms.
– Item (3)
Tinplate Sheets En 10202 – TS 245 – BA – BR – 2.8/2.8 – SP – 311
Dimensions(mm): 0.33 x 860 x 833
Hardness(HR30T): T52 BA
Type of steel: B
Usage: varnished and lacquered aerosol cans domed tops.
– Item (4)
Tinplate Sheets En 10202 – TS 290 – BA – BR – 2.8/2.8- HS-311
Dimensions(mm): 833 x 885 W x 0.18
Hardness(HR30T): T59 BA
Type of steel: A
Usage: varnished and lacquered welded aerosol cans bodies.
– Item (5)
Tinplate Sheets En 10202-TH 435-CA –BR 5.6/2.8 D -SP -311
Dimensions(mm): 0.31 x 899 x 721
Hardness(HR30T): T65 CA
Type of steel: B
Usage: varnished and lacquered aerosol cans bottoms.
– Item (6)
Tinplate Sheets En 10202 – TS 290 – BA – BR – 2.8/2.8- HS-311
Dimensions(mm): 912 x 850 W x 0.18
Hardness(HR30T): T59BA
Type of steel: A
Usage: varnished and lacquered welded aerosol cans bodies.
– Quality requirements :
1) Heavier coating should be packed down on platform.
2) The oil used should be suitable for varnishing, lacquering and printing (D.O.S).
3) The purity of tin should be 99.85% min.
4) Delivery is according to theoretical weight, deviation between actual weight and theoretical weight must not exceed sheets tolerances mentioned in European standard EN 10202:2001
Looking forward to receiving your reply and please let me know if you have any questions.