Introduction
Electrostatic powder is a polyester resin used in the metal packaging industry to protect welds from internal attack. Application and curing are critical processes that ensure the integrity and quality of the coating on the weld.
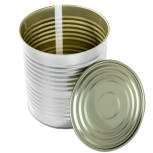
Electrostatic Powder Application
The electrostatic powder application process begins with the absorption of the powder from a fresh powder tank and its storage in a buffer tank. The powder then flows into a third tank that sends it to the application arm. Here, a negative tension d statically charges the particles, allowing them to adhere to the container forming a perfect band on the weld.
To delimit the application and form a precise strip, sealing skirts are used. A suction system recovers the excess powder immediately after application and sends it to a recycling unit for reuse.
Curing of the electrostatic powder
After application, the powder is melted and polymerized by the action of heat in a continuous oven. This curing process transforms the powder into a solid and resistant film that protects the weld.
Quality Control
Quality control is fundamental in the application and curing of electrostatic powder. Both in-line and laboratory tests are performed to ensure proper powder application and adhesion. Tests include measuring the thickness of the powder coating and verifying the absence of exposed metal after the container has been cordoned off.
Application Specifications
The specifications for the application of the electrostatic powder vary according to the type of welding and whether the inside of the container is varnished or not. The approximate ranges are:
- Coating width: 6-7 mm for bare containers, 10-12 mm for varnished containers.
- Film thickness: 35-50 microns.
- Film weight: 60-70 gr/m2 for bare interior, 85-120 gr/m2 for varnished interior.
Recommendations
For optimum application, it is recommended to cool the powder to improve its fluidity. In addition, the temperature of the supply air must be below 20°C to avoid problems in powder distribution.
Possible defects in electrostatic powder application and corrections may include:
- Insufficient powder application:
- Insufficient high voltage: Increase the powder charging current.
- Excessive high voltage: Reduce the charging current of the powder.
- Very low load: Increase the tribo air flow.
- Too much load: Reduce the tribo airflow.
- Electrode of the glued application head: Clean.
- Empty powder container: Refill powder.
- Bent dust duct: Replace the duct.
- Defective oscillating fork sensor: Check/adjust/replace.
- Old powder: Fill with new powder.
- Inner suction too strong: Check the effect of the injector.
- Powdered seam too thick:
- Welding seam too hot: Check the seam cooling system.
- Excessive supply air flow: Reduce the supply air flow.
- Irregular powder application:
- Empty powder container: Refill powder.
- Fluctuation of the system pressure: Check the network pressure.
- Accumulated dust: Clean the ducts.
- Static grounding: Check.
- Wave formation, dust accumulation:
- Dosing air/supply air ratio: Adjust (higher or lower).
- Application head/sticking spray element: Clean, replace.
- Sticking baffle: Clean.
- Worn baffle: Replace.
- Excessive dust on the body:
- Change of internal suction: Change of layer thickness.
- If the vacuum is insufficient, the powder ducts and the application head may become clogged.
- Change of additional suction: Change of the amount of powder suctioned in the area of the bodies.
- Crater formation due to spark discharge in the dust layer:
- Excessive dust in the body: Change the internal suction and adjust the coating thickness.
- Excessive dust on the internal part:
- Glued side brushes: Improve cooling of the weld seam.
- Too much powder: Reduce powder application.
- Defective sealing lips: Replace the sealing lips.