Nowadays printing is more and more based on speed and efficiency, for this reason one of the main key facts is the tuning of the Decorator.
Whether you operate a Rutherford or a Concord, the main effect is the Technician operating and maintaining the machine.
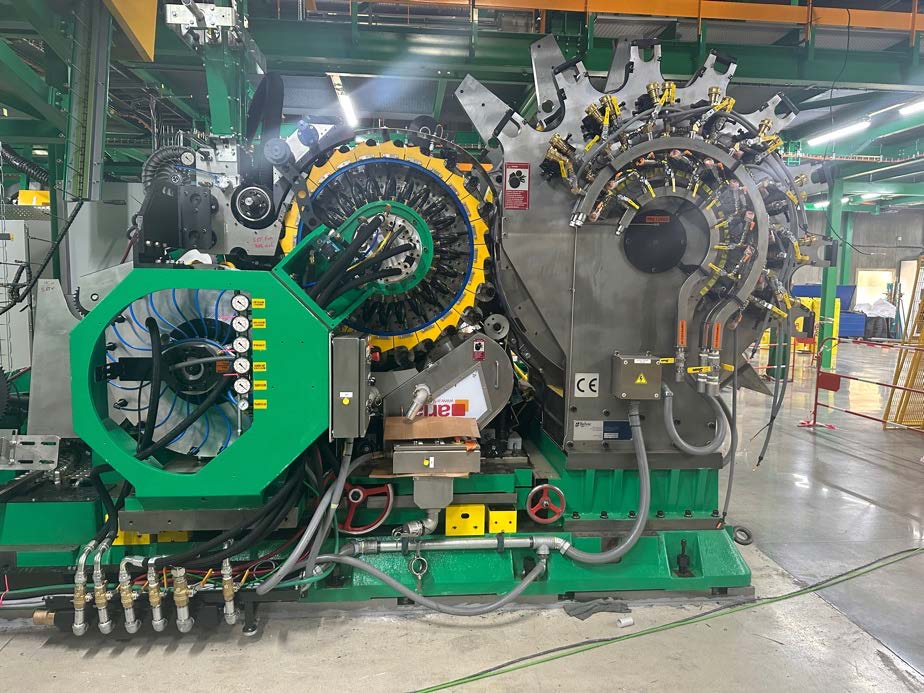
Both machines are doing a very good job, one is using the drive cylinder to move and print a can at high speed.
The other is using a very well engineered mechanical design to print a can, but both using the same printing form.
They are using a rubber blanket as a means to transfer the negative image onto the shiny can.
As the image begins to transfer onto a glossy can, both machines use pressure to squeeze the image with all the colors into the can.
This is what we call the printing pressure; with this printing pressure we can organize how the image will look on a can.
In certain cases it is necessary to adjust the printing pressure by increasing or decreasing it, sometimes we need to add pressure, this higher printing pressure is usually a sign that something is not in good condition.
In halftone printing, especially in fruit design, the printing pressure can be reduced to minimize dot gain. The dot gain effect will cause some spotting and color bleeding;
Therefore, the Decorator must maintain a minimum pressure.
There is a formula for calculating the actual pressure.
We take a blanket thickness of 0.077″ and add the can wall thickness of 0.005″, which equals 0.082″. Next, we use the space between the mandrel and the bear segment. In normal cases, this space is 0.068″ on a Concord and 0.065″ on a Rutherford. We then take 0.082″ and subtract the space (0.068″ and 0.065″), which will give us the impression of how much pressure we are creating inside the blanket.
The Concord operates with a printing pressure of 0.014″ and the Rutherford with 0.017″.
These two figures have shown us the small difference in printing, but more important is our tracking, tracking is something we will need at higher speed to maintain an equal print throughout the body of the can.
Over the years, this effect has been found to become increasingly important as speed increases. In the past the speed was quite low, around 1400-1800cpm, but now we aim to run at 2000-2200cpm continuously.
Just so you know, if you can imagine, the blanket wheel already runs at the double speed of the mandrel wheel and spindle disc and the time to complete a full print was just right, now with the high speed we have to set up and maintain the machines both very well to maintain a good quality printed can.
What can happen if our tracking changes, this will cause some printing problems especially on dark cans we will see this effect immediately.
But how can this happen? In most cases this occurs from lack of maintenance or misalignment or broken parts.
Just one example and this is a real case, an urgent service because the client customer was struggling for a long time with the Rutherford Deco to achieve the same label on two sides of the decorator.
As I tried to understand the situation, the customer told me that he had done almost everything possible to solve these problems. did almost everything to solve these problems, but they couldn’t find it and after two weeks of struggling they called in an expatriate to look into it.
It was a green label and they even brought in an expert from the ink manufacturer to install the green ink on a special machine so they could run the production.
We had a brief meeting and I asked the technician about maintenance and adjustments.
And, okay, everything was fine, but, nevertheless, I started to do my checks, first the printing pressure and then the tracking.
I immediately saw that there was some wear, as the leading edge was tighter than the trailing. I then asked the team to check the condition of the wear plates (Rutherford has wear plates where the carriage moves back and forth).
So, we lifted the car and we all had a big effect, we saw that one of the wear plates was broken, the wear plate was damaged on the rear which is heavier.
For me it was a quick fix problem after changing the plate and adjusting the height of the carriage the problem was solved.
This is just a sample of what can happen if the monitoring is not correct and has not been done correctly.
care for the machine no matter Concord or Rutherford.
Both machines require good maintenance and well-trained and qualified technicians.