Aluminum beverage can manufacturing is high volume, there are production lines that can run at more than 3,000 cans per minute when two printers are running in parallel, i.e. a production of more than 180,000 cans per hour. The slightest neglect at these speeds can lead to a massive production of non-conforming product and, as a consequence, to the separation of finished product, which is often difficult to avoid.
Personnel on the production floor are responsible for controlling product quality at every stage of the process, hence a robust can monitoring system must be in place throughout the entire production line. While the roles and responsibilities of the quality inspectors are to ensure that product quality is met at each stage of the process, auditing the information generated at the inspection stations and reinforcing with additional inspections any deviations or critical sampling points on the line.
A robust can quality monitoring system, with well-defined roles and responsibilities among operators in the different production areas, with the correct number of samples to be taken and at the critical sampling points in the line, will give us the guideline to detect in time any deviation in the process. However, even with this robust can quality monitoring scheme, it is necessary to understand the traceability patterns and codes that exist in an aluminum can for rapid root cause identification.
The aluminum cup that is produced in the cup press located at the front end of the line (Front End), often contains an identification on the outside bottom, this identification denotes the cavity in which it was produced and will always be in the direction of rolling of the material. This identification will exist throughout the entire aluminum can production process, serving as a reference to denote any anomaly with this cavity in the cup press.
Aluminum cans that are produced on bodymakers located at the Front End of the line have a number or identification stamped on the outside of the dome, this identification typically denotes the line and body forming machine on which the can was manufactured. The location of this number or identification will be located randomly with respect to the rolling direction of the material, hence it is preferred to have a clockwise location. This identification will exist throughout the entire aluminum can production process, serving as a reference to denote any anomaly with the body former.
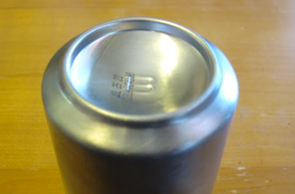
Aluminum cans that pass through the IC Spray Machine located at the Back End of the line are normally identified with an ink dot on the outside of the dome, this identification typically denotes the IC Spray Machine that processes that can. The ink color, number of dots and location is usually defined internally by the can manufacturer. The location of this ink spot will be randomly positioned with respect to the rolling direction of the material or the number of the body former. This identification will exist throughout the entire aluminum can production process, serving as a reference to denote any anomaly with the inner varnish atomizer.
Troubleshooting on a high-speed aluminum can production line is simpler, faster and more efficient if traceability patterns or symbols are included on the can body. Production codes located in the label overlap area or notches formed by printing blankets also located in the label overlap area form other identification alternatives for quick troubleshooting on the line.
Proper identification of the aluminum cups with their cavities, the can dome according to their body former, the production codes located in the overlap area of the label, the ink dots on the dome according to their inner varnish atomizer, and the identification label on each finished pallet, will be good manufacturing practices for quick and effective troubleshooting on an aluminum can production line.
Domingo R. Gonzalez
President and Founder
BetterCans, LLC.
Office. +1 (614) 389 -2278
Mobile. +1 (614) 949 -1786