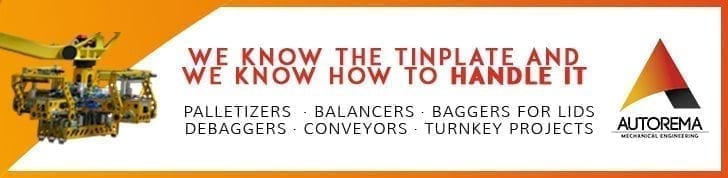
FABRICACIÓN Y CARACTERÍSTICAS DE LA HOJALATA
En este documento se desarrolla con cierto detalle las diferentes etapas en la fabricación de la hojalata, desde la obtención del acero base y sus distintas variedades, hasta las sucesivas secuencias del estañado de la misma.
ÍNDICE
Introducción
1.- Fabricación del aceroN
1.1.- Fabricación del acero base
1.2.- Secuencia de fabricación
1.3.- Composición del acero base
1.4.- Tipos de acero base
2.- Estañado
2.1- Estaño
2.2.-Estañado electrolítico
3.- TFS
INTRODUCCIÓN A LA HOJALATA
La hojalata es un material que aunque su invención viene de antiguo, realmente alcanzó su máximo desarrollo a lo largo del siglo pasado. Fue Estados Unidos el que tiró fuerte de esta industria, llegando en la década de los “70” a su mayor volumen de actividad en ese país. Después, el gran despliegue de los envases para bebidas, que en Norte América utilizó el aluminio como materia prima, el uso de envases alternativos y la obsolescencia de la industria siderurgia americana, hicieron entrar en declive ese mercado.
No ocurrió lo mismo en otras zonas del mundo. Europa supo modernizar a tiempo su siderurgia, manteniendo su competitividad, y así pudo resistir airosamente en envite del aluminio. De todas formas, una gran variedad de opciones de envasado hicieron algo de mella en el sector, que respondió acertadamente con una serie de fusiones, que permitieron mantener un excelente nivel tecnológico.
También en otras áreas geográficas como Sudamérica, Extremo Oriente y Asia, el mercado de la hojalata y otros productos recubiertos mantuvieron una buena posición en el mercado.
Hoy día sigue siendo un sector importante a nivel mundial, aunque en continua lucha competitiva. Por ello merece la pena conocer un poco como se fabrica este material.
1.- FABRICACIÓN DEL ACERO BASE
La hojalata normalmente es por peso, 99% o más acero, y es por tanto esencialmente un producto de acero. El proceso de fabricación realmente empieza en el horno alto y en la fundición de estaño, pero en la práctica se considera que empieza desde la fabricación del acero. De hecho es en este instante cuando se decide la composición y tipo de lingote de acero que se hará, definiendo su futura utilización como producto laminado. En consecuencia, las materias primas básicas para la fabricación de hojalata son acero y estaño refinado.
1.1.- Fabricación del acero base.
Hay dos procedimientos básicos para obtener acero en bruto en estado líquido: a partir de a) mineral de hierro y b) de chatarra.
A.- A partir de mineral de hierro (proceso de fundición): el mineral de hierro es una roca compuesta de óxidos de hierro y de otros varios minerales (ganga). Inicialmente los minerales y desechos metálicos empleados en la elaboración están llenos de impurezas. El hierro jamás está en estado puro en la naturaleza., se presenta la mayor parte de las veces en forma de óxidos y de sulfuros.
En el proceso industrial desarrollado en el alto horno se persigue obtener un producto lo mas rico posible en hierro, pero en él siempre aparecerán otros componentes. Entre las materias parásitas, muchas tienen una temperatura de combustión y de evaporación inferior a la del hierro, y desaparecerán calentando el mineral, o de densidad inferior al hierro, y estas flotaran en el metal en fusión. Para liberar del oxigeno a los compuestos de hierro en forma de óxidos ferrosos (FeO), magnéticos (Fe3O) y ferricos (Fe2O3) es necesario aprovechar la facilidad que tiene el carbono de reaccionar con el oxigeno.
El carbono en su combustión es un gran devorador de oxigeno, el cual lo tomará del aire, pero también del oxido para formar los compuestos CO y CO2 (monóxido y bióxido de carbono). En esta operación, la parte excedentaria de carbono dejará trazas de este último combinadas con el hierro (del 3 al 6 %). Este material resultante en el alto horno se denomina “fundición”.
Para liberarse del carbono se podrá hace una operación complementaria añadiendo oxigeno para volver a formar CO y CO2, gases carbónicos. También este oxigeno puede reaccionar con otros elementos contenidos en la fundición, como el manganeso formando oxido de manganeso (MnO) , sílice (SiO2), alúmina (Al2O3)… Todas estas operaciones se realizan en primer lugar en el alto horno y después, como veremos algo mas adelante, en la operación de refinado.
Haciendo pues un resumen, podíamos decir que en un alto horno, después de una etapa de preparación del mineral en el taller de aglomeración, se realiza la extracción del hierro en el alto horno, con la ayuda de un combustible: el carbono (coke). No se obtiene todavía hierro puro, sino fundición de hierro, mezcla liquida de hierro (96 %) más carbono (3%) proveniente del resto de coke que no se ha quemado, mas algunos residuos (fósforo, azufre…) provenientes de la ganga. En la figura nº 1 se presenta un corte vertical de un alto horno.
Figura nº 1: Esquema de un alto horno
B.- A partir de chatarra (“procedimiento eléctrico): Los componentes con los que se alimenta el horno puede ser desde materiales en estado bruto (por ejemplo piezas de maquinaria) debidamente seleccionados, hasta la chatarra preparada, seleccionada, triturada, calibrada, con un contenido mínimo de hierro del 92 %. Todo este conjunto se funde en un horno eléctrico.
El arrabio (pig iron) o hierro proveniente del horno alto, o el procedente de chatarra fundida en horno eléctrico, es una aleación de hierro-carbono, frágil y con alto contenido de este ultimo elemento. Puede haber también alto contenido de azufre y fósforo. La fabricación del acero es el proceso de refinamiento, para reducir y controlar los porcentajes de otros elementos distintos al hierro, con objeto de producir lingotes de la pureza, características y maleabilidad requeridas. En términos generales, estos elementos y las impurezas se reducen por oxidación con oxido de hierro u oxigeno, y se eliminan por flotación con adición de materiales de alto punto de fusión (por ejemplo piedra caliza).
En la actualidad se emplean cuatro procedimientos básicos para la obtención de acero, que son: proceso Siemens-Martin o de crisol abierto, proceso Bessemer o Thomas, proceso de inyección de oxigeno superior (top-blown oxygen process) y horno eléctrico. Este último es poco utilizado para la fabricación de hojalata. El primero y el segundo son quizás los más extensamente usados junto los procedimientos neumáticos..
Proceso de “crisol abierto”.- El crisol suele ser cargado con hierro fundido procedente del horno alto, chatarra y arrabio frío. Las impurezas son oxidadas provocando la formación de una escoria oxidante, y el combustible empleado puede ser líquido o gaseoso. La capacidad de un horno de este tipo puede ser hasta 400 toneladas y mediante el uso de oxigeno a granel, de economía relativa, puede tener alto rendimiento, llegando a las 50 toneladas/hora. Estos hornos pueden ser fijos o basculantes.
Proceso Bessemer o Thomas.- En este sistema, las impurezas son reducidas por inyección directa de aire u oxigeno, a través del metal fundido, por medio de toberas colocadas en el fondo del convertidor. Ver figura nº 2:
Figura nº 2: Elaboración del acero en el convertidor Thomas
Para quemar el carbono de la fundición, se insufla aire o una mezcla de aire y oxigeno a través del metal en fusión vertido en el convertidor, que es una gran retorta de acero de una capacidad de 25 a 50 toneladas. Las paredes refractarias del convertidor son de dolomita básica, inatacable a la cal que se debe introducir para eliminar el fósforo de la fundición. La productividad y calidad puede mejorarse, controlando la composición del gas oxidante inyectado, aire, aire enriquecido con oxigeno, oxigeno, mezcla de oxigeno y bióxido de carbono, etc. Por ejemplo, la variante VLN (very low nitrógeno = muy bajo nitrógeno) no solamente aumenta la producción sino que reduce la incorporación de nitrógeno al acero, que normalmente es indeseable.
Durante el proceso se distinguen varias fases o periodos. En el primer periodo se producen bastantes chispas, ocasionadas por la combustión del silicio que dura de 2 a 3 minutos. En el segundo se generan llamas por la combustión del carbono, con una persistencia de 10 a 12minutos. En el tercero se caracteriza por la expulsión de gases provocada por el soplado posterior y la combustión del fósforo, su intervalo es de 3 a 5 minutos.
A lo largo del proceso se suelen añadir diferentes elementos sólidos como: cal, chatarra, ferro-manganeso o arrabio especular según necesidades.
Existe el sistema llamado Duplex, que aplicado a la fabricación de acero para hojalata, significa la combinación del proceso acido Bessemer con el de crisol abierto básico. En el convertidor se realiza la purificación principal, mientras que en la segunda parte del proceso se efectúa la reducción del fósforo.
Proceso de inyección de oxigeno superior.- El proceso Bessemer es ampliamente usado principalmente por su bajo coste de instalación y flexibilidad de operación, pero tiene grandes limitaciones en cuanto a calidad final, ya que requiere una materia prima con alto contenido de fósforo y restricciones en el uso de chatarra. Estas dificultades afectaron fuertemente a algunos fabricantes, lo que condujo al desarrollo de los procesos de inyección de oxigeno superior, que permiten obtener aceros de calidad buena y constante, con bajo contenido de nitrogeno y alto o bajo de fósforo, según necesidades. Hay tres sistemas bastante usados para materiales laminados y son los llamados LD, DDAC y KALDO.
El proceso LD fue el primero basado en la disponibilidad de oxigeno en grandes cantidades. Consiste en sustituir la inyección de aire por el fondo de un convertidor Bessemer, por la inyección de un chorro de oxigeno a alta presión, por la parte superior, lo que produce una fuerte agitación, y por consiguiente una oxidación muy rápida de las impurezas. Es un proceso rápido y eficiente, con inversiones iniciales no mucho mayores que con el proceso Bessemer, reduce los problemas de mantenimiento y produce un material de bajo contenido en nitrogeno, siendo una de sus limitaciones el tener que usar hierros de bajo o medio contenido de fósforo. Este sistema fue desarrollado por dos compañías localizadas en Linz y Donawitz. De las iniciales de estas ciudades viene el nombre de proceso LD.
DDAC es un proceso exactamente igual al anterior, salvo que se inyecta cal junto con el oxigeno. Es una tecnología de origen francés
El proceso KALDO primeramente fue desarrollado en Suecia y utiliza un crisol u horno rotativo y basculante, con aplicación de chorro de oxigeno en la parte superior y adición de cal por inyección o en trozos.
Los procesos de oxígeno son versátiles y permiten el uso de razonables cantidades de mineral y chatarra, produciendo acero de bajo fosforo y nitrogeno, con buenas características mecánicas.
Colada del acero.- Una vez obtenido el acero por alguno de los procedimientos descritos, estando aun en el convertidor y en estado líquido, hay que trasformarlo a estado sólido, realizando su colada. Industrialmente existen dos procedimientos de colada. El más clásico en el cual puede convertirse en lingotes (“colada en lingoteras”) o seguir el procedimiento de “colada continua”.
Colada en lingotera.- Es el procedimiento convencional. Por medio de una cuchara se va vertiendo el acero fundido en lingoteras, que una vez enfriadas dan lugar a lingotes manejables con los que se alimentan las siguientes operaciones.
Colada continua.- Es el procedimiento más moderno de fabricación de planchas. Tiene las ventajas principales de producir semiproductos de muy alta calidad, permite rebajar costos de producción, y aumenta la productividad de la aceria. De hecho, gracias a este sistema, las operaciones son menos numerosas y más simples que en la colada en lingoteras. . Está desterrando el uso de lingotes para aceros destinados a laminados. Ver figura nº 3:
Figura nº. 3: Colada continua
En la colada continua, el contenido del convertidor es vertido por medio de una cuchara, de modo regular y sin interrupción en una lingotera sin fondo y refrigerada, de sección tal que se corresponda con la de la plancha deseada. Después, pasa a través de una serie de rodillos para su aplanado, y finalmente por medio de un soplete de oxicorte se corta las planchas a la longitud deseada. De esta manera se obtienen planchas (slab) de longitud entre 5 a 20 metros, anchura hasta algo más de un metro y espesor de unos 20 cms.
1.2.- Secuencia de fabricación.
La figura nº 4 presenta una secuencia de las diferentes operaciones o fases de elaboración de las planchas de acero que serán la materia prima básica en las plantas de fabricación de hojalata.
Figura nº 4: Fabricación de planchas de acero
Cuando se ha empleado el proceso de colada en lingotera, una vez fundido el acero en lingotes, la primera operación que se efectúa es el laminado del lingote para convertirlo en plancha (slab). Esta operación se suele efectuar en trenes de laminación reversibles, de doble alto. Los del llamado tipo Universal, tienen cilindros o rodillos laterales que trabajan simultáneamente las 4 caras del lingote, eliminando la operación de girar sobre su eje el lingote durante esta etapa.
El producto final de esta operación, la plancha o slab, tiene de 125 a 230 mms de espesor, el ancho aproximado de la hojalata que finalmente se desea obtener, y una longitud que depende del tamaño del lingote original.
Las planchas generadas tanto por colada continua como por laminado de lingotes quedan preparadas para ser tratadas en el laminado en caliente.
El laminado en caliente es el paso siguiente, aunque normalmente hay una etapa intermedia, que consiste en enfriar y almacenar las planchas, hacer un proceso de selección, una preparación de la superficie (escarpado) y un calentamiento de la plancha a la temperatura conveniente para el laminado. Eliminar esta etapa intermedia requiere una programación muy exacta, y una capacidad tecnológica muy alta, que asegure la ausencia de defectos en las planchas o slabs. En la figura nº 5 se aprecia las diferentes fases del laminado en caliente.
Figura nº 5: Proceso de laminado en caliente
La preparación de la superficie se realiza en la “descascarilladora”, en la cual se somete a la plancha a un desprendimiento de óxidos de hierro e impurezas, lo cual se consigue por medio de una débil presión de laminado, desprendiendose los mismos por la acción de agua a alta presión. La plancha se calienta a una temperatura de 880º C. Es necesario eliminar esta capa de óxidos pues perjudica el laminado, ya que provoca desgate rápido de los cilindros, estrías sobre el metal, incrustaciones de óxidos y otros defectos de fabricación (roturas, deslizamientos, pliegues…)
El tren de laminación en caliente, reduce la plancha a una banda continúa de unos 2 mms de espesor. Normalmente se compone de dos secciones, una de desbaste y otra de acabado. Puede ser de tipo continuo o reversible, dependiendo de la capacidad de la instalación, etc.
El tren de desbaste suele constar de 4 a 6 cajas que reducen el espesor inicial de la plancha entre un 25 a 50% por caja.. El tren de acabado dispone de 4 a 7 cajas, reduciendo de nuevo el espesor entre el 25 a 30 % por caja, salvo la ultima que solo reduce un 10 %. La velocidad máxima de esta operación puede estar en los 100km/h. A la salida el material se encuentra a 850º C. Se procede a un enfriamiento por cortina de agua hasta los 590º, formándose bobinas con el mismo.
La bobina (coil) producida debe ser decapada y lubricada antes de proceder a su laminación en frío. Esta operación se suele efectuar en una sucesión de tanques que contienen ácido sulfúrico diluido caliente (próximo a 100º C), lavado, secado y lubricado con aceite de palma u otro lubricante adecuado para la laminación en frío. La línea de decapado va provista normalmente de una cortadora circular, que corta los bordes, asegurando así que estos son adecuados para la reducción o laminación en frío, fijando además el ancho máximo de la hojalata que se obtendrá y también el que dará los mejores resultados económicos. Ver figura nº 6.
Figura nº 6: Laminado en frío, recocido y “skin-pass” del acero base
La operación siguiente es el laminado en frío, que se puede hacer en trenes continuos (tándems) o reversibles. Durante esta operación se utilizan lubricantes y refrigerantes, y el espesor resultante es muy cercano al final deseado. La reducción es por tanto de 1.8 o 2 mms a una medida entre 0.15 a 0.3 mm aproximadamente según el calibre final de la hojalata a producir.
La bobina obtenida es de un material muy duro y sujeto a fuertes tensiones, y necesita un tratamiento adecuado para darle la maquinabilidad necesaria, provocando una recristalización del acero. Este tratamiento se llama recocido (annealing) y se trata de un calentamiento del metal en una atmosfera reductora para evitar toda oxidación (mezcla de nitrogeno y de hidrogeno) y puede hacerse continuo (continous annealing) o en hornos de campana (batch annealing).
Recocido continuo: La banda circula a través de un horno a una temperatura de 630º C, permaneciendo un tiempo mínimo cada punto del material 1,5 minutos en el horno. El recocido continuo presenta una serie de ventajas e inconvenientes como son:
Ventajas:
– Reducción de los materiales “en curso” de fabricación.
– Reducción de los plazos de fabricación.
– Mejora de la calidad de los productos fabricados:
o Calentamiento constante y continuo a todo lo largo de la bobina, con lo que se consiguen propiedades mecánicas mas homogéneas.
o Ciclo rápido, con lo que se obtienen granos finos equiaxiales, por lo tanto un metal isótropico y propiedades mecánicas superiores, como mejora del límite elástico.
o Mejor resistencia a la corrosión. El ciclo rápido no permite que elementos tales como el carbono, manganeso, fósforo… se desplacen hasta la superficie del material como ocurre en el recocido base o en campana.
o Permite la utilización de una composición de acero tipo MR, menos cargada de elementos endurecedores: carbono, manganeso…. (Recocido continuo = 0.08 % de carbono, Recocido base = 0.10/0.13 % de carbono) lo cual favorece a operaciones como la soldadura, especialidades…
Inconvenientes:
– Fabricación:
o Difícil programación de los pedidos, ya que la máxima variación de anchura entre bobinas consecutivas es del orden de 50 mm, y de espesor del orden del 10 %.
o Delicada conducción de la línea. Riesgo de ruptura de la banda en el horno. Supone una importante parada. El limite elástico de la banda a la temperatura del horno de recocido es bajo (30 N/mm2 aprox.)
o Imposibilidad de paradas de línea.
– Utilización:
o Cristalografía fina que genera un metal menos dúctil, de anisotrópica débil, que perjudica la embutición
o Riesgo de presencia de líneas de Lüder.
Recocido en campana: Varias bobinas apiladas se cubren con una campana en atmosfera reductora a 680º C de temperatura durante un tiempo al menos de 85 horas, repartidas en 32 horas de calentamiento, 34 de enfriamiento bajo campana hasta los 170º, y 19 horas de enfriamiento acelerado al aire libre. Ver figura nº 7
Figura nº 7: Esquema del proceso de recocido en campana.
En ambos casos es indispensable eliminar previamente los residuos de los agentes lubricantes y enfriadores usados anteriormente, siendo el método empleado para ello, consecuente con el tipo de recocido que se haga, normalmente por medios electroquímicos, como baño de desengrasante calentado a 95 ºC o mecánicos, con cepillado por las dos caras.
A continuación viene la operación de templado, tratamiento superficial o acabado (temper rolling o skin-pass). Se hace por medio de una reducción o laminación, sin lubricante y muy ligera, que no suele exceder del 2% en espesor. Para ello se emplea un tren de laminación formado por dos cajas. La banda, al pasar entre los cilindros bajo el efecto de la presión y tracción establecidas, sufre una modificación superficial de la estructura consiguiendo un aumento de la dureza de la capa superficial, pero conservando la suavidad interna.
En resumen, esta operación da la banda la dureza deseada, un buen aplanado y una superficie de acabado del material en función de la rugosidad de los cilindros empleados en las cajas del tren de laminación. Combinando el acabado superficial de los cilindros de las cajas de esta laminación, y el refundido final del estaño después de la operación de estañado, se consiguen diferentes acabados superficiales de la hojalata. Los principales tipos de acabados son:
Acabado brillante: Para realizar este acabado, es indispensable obtener en los cilindros un pulido a espejo. Además es necesario aplicar la refusión del estañado Este tipo de acabado es, junto al piedra, el más solicitado
Acabado piedra: Los cilindros se someten a dos pasadas de rectificación con una muela de grano especial, que da al producto un aspecto como estriado. Como en el caso precedente, el revestimiento de estaño se refunde, lo cual asegura, además la brillantez.
Acabado mate: Presenta una superficie poco reflexiva. Para realizarlo, los cilindros se granallan y la operación de refusión después del estañado se suprime.
Cuando se trata de hojalata doble reducida, la última reducción de calibre se hace sustituyendo la operación de templado por una nueva reducción de calibre o laminación de aproximadamente 33%, con el consiguiente alargamiento del material en un porcentaje similar, usando esta vez lubricantes superficiales. Así se trasmite a la hojalata unas características mecánicas elevadas con un espesor pequeño.
Es práctica corriente preparar las bobinas previamente a la operación de estañado. Consiste principalmente en cortar los bordes y eliminar las secciones de baja calidad o de calibre fuera de especificaciones formándose bobinas de tamaño óptimo para la línea de estañado.
En el estañado electrolítico, el material preparado pasa en forma continua por las operaciones de limpiado electrolítico, decapado electrolítico, electro-deposición del estaño, refundido del estaño (flow-melting), tratamiento de pasivación y lubricación. Después de esta serie de operaciones, el producto puede ser cortado en hojas al tamaño ordenado (largo, ya que el ancho se dio al preparar las bobinas), inspeccionado, seleccionado y empacado; o puede ser embobinado para enviarse al cliente o para ser cortado, etc. en una línea de corte separada. Es normal efectuar en la misma línea, la selección del material, antes de empacar. Mas adelante volveremos sobre estos puntos mas detalladamente.
1.3.- Composición del acero base.
Para hojalata, el acero base, es esencialmente un acero suave de bajo contenido de carbono, con una composición genérica del tipo siguiente:
– Carbono 0.04 – 0.15 %
– Silicio 0.08 % máximo
– Azufre 0.015 – 0.05 %
– Fósforo 0.01 – 0.14 %
– Cobre 0.02 – 0.20 %
– Manganeso 0.20 – 0.70 %
– Nitrógeno 0.001 – 0.025 %
Debido al uso de chatarra en la fabricación de acero, puede haber otros elementos como níquel, cromo y estaño, pero intencionadamente no se añade ningún otro elemento. Las solas excepciones son fósforo y nitrógeno que pueden aportar propiedades especiales. El uso de cobre para aumentar la resistencia a la corrosión, y de algunos carburos para controlar el envejecimiento ha caído en desuso.
La influencia de algunos elementos en el acero base de la hojalata, se da a grandes rasgos en los párrafos siguientes.
– Carbono: El carbono aumenta el límite elástico, el límite de rotura a la tracción y la dureza, disminuye la elongación y la ductibilidad. Dentro de los límites usuales en la hojalata, las variaciones en el contenido de este elemento revisten escasa importancia, ya que otros elementos influyen mucho más.
– Silicio: Existe en la hojalata como un elemento residual, muy raramente se le añade como agente desoxidante. Endurece ligeramente y en algunos casos afecta desfavorablemente la resistencia a la corrosión.
– Azufre: En este tipo de acero, los efectos del azufre son contrarrestados por el manganeso, que siempre está presente. Sin embargo, debido a sus consecuencias sobre la ductibilidad, calidad de superficie y resistencia a la corrosión, se hace lo posible, dentro de límites económicos, para reducirlo al mínimo posible.
– Fósforo: Es un elemento que influye altamente sobre la dureza y la resistencia a la corrosión. Cuando hay posibilidades de corrosión acida, debe mantenerse dentro de determinados límites, y se aumenta el contenido cuando se requiere una mayor resistencia del acero y no hay peligro de corrosión.
– Cobre: Aunque aumenta la resistencia, no lo hace con eficacia dentro de los límites usuales. Sobrepasar estos limites, aumenta la resistencia a la corrosión atmosférica, pero puede reducir la resistencia a la corrosión interna, por lo que en la mayoría de los tipos de hojalata, se especifica un máximo de cobre.
– Manganeso; Se emplea en la fabricación de acero para hojalata, principalmente para que reaccione con otros elementos, principalmente azufre, volviéndolos inoperantes.
– Nitrogeno: En aceros Bessemer, es un elemento constituyente normal en porcentajes superiores al 0.01% y siempre se consideró como una desventaja. Con posterioridad se ha encontrado que su adición intencionada aumenta mucho la resistencia del acero sin modificar apreciablemente la resistencia a la corrosión, aunque puede afectar el envejecimiento. El desarrollo de los procesos de oxigeno (LD, etc.) ha permitido controlar con exactitud el contenido de este elemento, dando una calidad uniforme y continua.
– Níquel: En los niveles permitidos, no afecta mayormente las propiedades físicas o mecánicas de la hojalata, pero sí las químicas, especialmente la corrosión en ciertos tipos de envasados. Lo mismo ocurre con el cromo.
– Estaño: Este elemento tiene una alta solubilidad en el hierro o acero, y se hacen necesarios porcentajes superiores al 10 % para que se forme una segunda fase. En los niveles normales no tiene efecto en la estructura metalografía. Su presencia aumenta progresivamente el limite elástico y el limite de rotura a la tracción, con una reducción en el modulo de elasticidad. Es importante notar que pequeñas cantidades de estaño, en aceros que contengan cobre, puede ocasionar graves dificultades en el trabajo en caliente del acero.
En la siderurgia a veces se usan reglas prácticas, para calcular los efectos de los elementos aleados y residuales en las propiedades mecánicas del acero para hojalata. Uno de los más comunes es el índice Strohmayer, que se calcula multiplicando el contenido de nitrógeno por 5, sumando el fósforo y multiplicando la suma por 1000.
1.4.- Tipos de acero base
Tradicionalmente hay tres tipos básicos de acero para hojalata, aunque con las tecnologías actuales resulta a veces difícil mantenerse dentro de los tipos clásicos. Estos son:
Tipo L: Es un acero laminado en frío, procedente de hornos de crisol abierto (Siemmens Martin). Tiene un bajo contenido en metaloides y elementos residuales, especialmente limitado en fósforo, con la siguiente composición:
Carbono 0.05 – 0.13 %
Manganeso 0.30 – 0.60 %
Azufre 0.04 máx.
Fósforo 0.015 máx.
Silicio 0.010 máx.
Cobre 0.06 máx.
Níquel 0.04 máx.
Cromo 0.06 máx.
Molibdeno 0.05 máx.
Arsénico 0.02 máx.
Nitrógeno 0.02 máx.
Se utiliza cuando se busca una resistencia elevada a productos muy corrosivos.
Tipo MR: Es el mas empleado. Es de la misma procedencia del anterior, laminado en frío y usado en productos medianamente corrosivos. Su análisis es:
Carbono 0.05 – 0.15 %
Manganeso 0.30 – 0.60 %
Azufre 0.04 máx.
Fósforo 0.020máx.
Silicio 0.010 máx.
Cobre 0.20 máx.
Tipo MC: Es un acero hecho en convertidor Bessemer u horno Siemmens Martin, utilizado cuando la resistencia y el contenido del envase es de baja corrosividad. Su análisis tipo es el siguiente:
Carbono 0.05 – 0.15 %
Manganeso 0.25 – 0.60 %
Azufre 0.04 máx.
Fósforo 0.03 – 0.15 %
Silicio 0.010 máx.
Cobre 0.20 máx.
Hay además algunos aceros especiales como el tipo D, calmado al aluminio, utilizado en casos específicos de embutición profunda.
Por lo general los fabricantes en Europa se han visto obligados a tratar de eliminar las producciones especializadas de hojalata y así encontrar procedimientos económicos y competitivos, por lo que tratan de simplificar el problema.
También tiene importancia, desde el punto de vista de resistencia a la corrosión, la superficie del acero, la misma en parte depende de la clase de atmosfera empleada durante el recocido. Una atmosfera que contenga nitrógeno, hidrogeno, bióxido de carbono y vapor de agua, produce una hojalata menos resistente que una de nitrógeno seco conteniendo de 4 a 8 % de hidrogeno. También los iones de estaño disueltos tienen en general un efecto inhibidor en la corrosión de la hojalata por algunos productos.
2.- ESTAÑADO
2.1.- Estaño
Cuando este material está destinado a la fabricación de hojalata, es lógico pensar que estará en contacto prolongado con productos alimenticios, y por lo tanto debe cumplir ciertos requisitos en cuanto a impurezas. La Sociedad Americana de Pruebas y Materiales (ASTM) hace una clasificación en cinco grupos, con contenidos mínimos de estaño cada una señalados a continuación: grado AA = 99.98 % de estaño, A = 99.80 %, B = 99.7 %, C-1 = 99.0 % y C-2 = 99.0 %. El mínimo especificado para la fabricación de hojalata es el grado A Su análisis es:
Estaño (mínimo) 99.80 %
Antimonio 0.04 %
Arsénico 0.04 %
Bismuto 0.015 %
Cobre 0.03 %
Hierro 0.015 %
Plomo 0.05 %
Níquel y Cobalto 0.015 %
Plata 0.01 %
Azufre 0.003 %
Zinc 0.001 %
Cadmio 0.001 %
Aluminio 0.001 %
- 2.- Estañado electrolítico
El desarrollo de este procedimiento de estañado fue uno de los pasos más importantes en la industria del sector. La electro-deposición del estaño en una cinta estrecha continua (fleje), se inició en Alemania en 1930, pero fue durante la 2ª Guerra Mundial cuando la técnica se desarrolló intensamente, principalmente en USA, debido a la escasez de estaño.
Hay una gran cantidad de razones técnicas y económicas que hicieron que la hojalata electrolítica quitara del mercado a la hojalata coke o estañadas en caliente, que era el medio tradicional de obtenerla. Una de las mas importantes, es el control preciso de la cantidad de estaño depositado y la uniformidad en espesor. Otra es la disponibilidad de hojalata electrolítica diferencial, que consiste en aplicar diferentes espesores de recubrimiento de estaño en cada cara de la hoja.
Como ya hemos indicado en la operación de templado del acero base, la hojalata electrolítica puede producirse en varios acabados, aunque tres son los más usuales. “Brillante”, que es el mas común, “mate” que consiste en estañar acero base con una superficie rugosa y después no refundir el estaño y por ultimo “piedra” que es mismo acabado anterior pero refundiendo el estaño, lo que da un acabado brillante pero no reflectante.
Los métodos de fabricación son básicamente dos, proceso acido y alcalino o básico, pero este ultimo presenta dos variantes de amplio uso, líneas halógenas horizontales y líneas alcalinas o verticales. Hay un cuarto procedimiento, que utiliza como electrolito fluoboratos, pero que es muy poco utilizado.
Las líneas que utilizan el proceso acido, son las que producen el mayor porcentaje de hojalata electrolítica. Frecuentemente son llamadas Ferrostan, por ser este nombre el registrado en su día por U.S. Steel para su hojalata, habiendo posteriormente muchas licenciatarias de su tecnología en el mundo.
Los electrolitos son la parte mas delicada en cada proceso. Por ejemplo, en las líneas acidas, es una solución de sales estanosas en acido, pero el buen funcionamiento como electrolito depende de los varios aditivos usados que tienen tres objetivos principales, evitar la oxidación, favorecer la formación de depósitos compactos y no esponjosos, y mejorar la humectabilidad.
Algunas ventajas clásicas de usar electrolito alcalino son disponer de un electrolito más sencillo, fácil de manejar y no corrosivo con relación al acero, lo que reduce el coste inicial del equipo. También la sección preparatoria es más sencilla.
Las líneas acidas tienen la ventaja de utilizar menos corriente para el estañado que las alcalinas, es por tanto necesaria menor superficie de ánodo y la eficiencia eléctrica es mayor en la electro-deposición. Sin embargo las líneas alcalinas producen una hojalata con mejores características de resistencia a la corrosión.
En términos amplios, los tres tipos de lineas se componen de las siguientes secciones:
Desbobinado
Preparación
Estañado
Acabado
Corte- embobinado – embalaje
La sección de entrada o desbobinado, tiene los equipos necesarios para el manejo de las bobinas de chapa negra, y para la alimentación continua de la línea, mediante corte del principio y fin de cada bobina y la soldadora eléctrica del fin de una con el principio de la siguiente. Incluye rodillos guía y de alimentación, de tensión, etc.
Entre la sección de desbobinado y preparación, hay un dispositivo para almacenar banda de chapa negra, destinado a acumular una cierta cantidad de banda, que alimenta la línea mientras se efectúa el cambio y empalme de bobina en la sección previa de desbobinado. Hay varios tipos, predominando los de pozo y los de “acordeón”.
La sección de preparación tiene dos objetivos principales, limpiado (desengrasado) y decapado. El primero es la eliminación de todos los elementos residuales en la superficie de la banda, provenientes de lubricantes, agentes enfriadores, etc., mientras que el segundo pretende eliminar el oxido de hierro adherido a ambas caras de la banda.
El tratamiento se efectúa en una sucesión de baños, químicos o electro-químicos, con lavados alternos a chorro de agua y/o vapor. La disposición y tipo depende de la línea. Por ejemplo, el desengrasado es normalmente hecho en una solución detergente o alcalina y en las lineas de este tipo se elimina o disminuye porque se efectuad el desengrasado automáticamente en la sección de estañado.
La sección de estañado difiere totalmente en cada proceso, siendo la del proceso halógeno la que mayor superficie ocupa, ya que la banda se mueve plana, normalmente en 3 niveles, mientras que en los otros dos sistemas sigue una forma senoidal o de serpentín.
Figura nº 9: Línea de estañado, cuba electrolítica y ánodos
Antes del estañado, se efectúan en la banda de chapa negra las marcas correspondientes a la hojalata diferencial, cuando es este tipo el que se fabrica, por tanto estas marcas van sobre el acero base. Algunos fabricantes pueden marcar el acero base para que en caso de dificultades posteriores con la hojalata, se pueda identificar al fabricante. Estas marcas no son visibles en la hoja como tal, es preciso encontrarlas en el laboratorio.
La sección de acabado incluye diferentes pasos, siendo los fundamentales: refusión, pasivación y lubricación.
La refusión tiene por objeto dar un acabado brillante a la hojalata, ya que la simple electro-deposición del estaño produce una superficie micro-rugosa de aspecto mate. Sin embargo, este paso tiene una importancia fundamental para la hojalata destinada a estar en contacto con elementos corrosivos. Durante la refusión, se forma una capa de aleación hierro-estaño, y debido a la rapidez con que se produce, el espesor es muy delgado De aquí se deduce que la hojalata mate, que no ha sufrido proceso de refusión, no debe usarse para aquellos fines que requieran la presencia de una capa de aleación hierro-estaño.
La pasivación es una característica propia de la hojalata electrolítica. En ella sobre todo en los recubrimientos bajos, es conveniente proveerla con una capa protectora que evite la oxidación, no solo durante la fabricación, sino también en operaciones sucesivas, como puede ser el barnizado. Es así mismo necesario dar una superficie químicamente más apta para litografiar y barnizar, y de cierta dureza protectora. La pasivación pretende cubrir este aspecto, y fundamentalmente consiste en formar una capa de oxido crómico. Los métodos empleados son varios químicos o electro-químicos, diseñados cada uno de ellos para obtener características especiales. Normalmente son conocidos por las siglas USS y un numero de tres cifras, la primera indica el tipo de solución (1 = acido crómico, 2 = fosfato de cromo, 3 = dicromato de sodio, 4 = carbonato de sodio), la segunda indica la polaridad de la hojalata en la solución (0 = no electrolítica, 1 = catódica, 2 = catódica/anódica) y la tercera cifra se refiere aproximadamente al nivel de corriente empleado.
Hay tres tipos básicos de pasivación, que son:
– Pasivación 300: Se obtiene por procedimiento químico, por inmersión en solución de dicromato sódico, generando una capa de oxido de cromo. Da buenos resultados desde el punto de vista de la adherencia del barniz. Ofrece una débil protección contra la sulfuración. Esta pasivación es sin embargo inestable. Su efectividad se va reduciendo con el tiempo
– Pasivación 311: Obtenida por procedimiento electroquímico por deposición electrolítica en un baño de dicromato sódico de una capa de cromo y oxido de cromo. Es la pasivación más utilizada. Tiene unos rendimientos convenientes desde el punto de vista de la adherencia de barnices, aunque inferiores a la pasivación 300. Es mucho más estable en el tiempo que la 300 .Por tanto se puede considerar un compromiso entre la estabilidad en el tiempo y la calidad de la adherencia de los sistemas litográficos
– Pasivación 312: Se consigue por el mismo sistema que la 311. De hecho es una pasivación 311 reforzada. Se utiliza principalmente para las hojalatas que deben resistir productos sulfurantes, como carnes, sopas, productos para perros y gatos…Su adherencia a tintas y barnices es inferior a la 311.
Los diferentes tratamientos de pasivación, no solo afectan a la adherencia de barnices, soldadura, etc., sino que también producen diversas formas de ataque o manchado, al estar sujeta la hojalata al contacto con productos corrosivos, o con compuestos azufrados. Aun desde el punto de vista estético o de presentación, este detalle reviste importancia, por ejemplo con la leche condensada.
Por ultimo, la sección de acabado efectúa la operación de lubricado. Este lubricante tiene por objeto, no tanto proteger la hojalata en sí, sino la pasivación y para no contrarrestar las propiedades de esta es muy ligera, por lo que el método de aplicación más comúnmente usado es por electro-deposición, aunque puede hacerse por aspersión o inmersión. Tres tipos de aceite son empleados normalmente, aceite de semilla de algodón, dioctilo sebacato y dibutil sebacato, el segundo es el más usual. La cantidad normal de lubricante es de orden de 0.005 grs/m2. Se suele secar el lubricante por medio de serpentines de vapor y aire caliente.
La última parte de la línea, depende en su formación del producto final y de la productividad que se pretende obtener, mas que del tipo de la línea (acida, …) Si la producción es exclusivamente en bobinas, no habrá corte pero si existirá un dispositivo de almacenamiento de banda, para permitir el cambio de bobinas. Si la producción es exclusivamente en hojas cortadas, no es necesario el dispositivo de almacenamiento. En la operación de corte, se hace la selección de defectos superficiales, este control no es muy eficiente debido a la velocidad de la línea, por lo que el producto obtenido se clasifica como “sin seleccionar” (unassorted). Si se desea separar “primeras” de “segundas”, es necesario utilizar los servicios auxiliares de una línea de selección. Es en esta sección donde se separan las hojas de calibre fuera de especificaciones y las perforadas (“pin holes”). Cuando se entregan bobinas, lo normal es no hacer esta separación, que disminuye el rendimiento, quedando por cuenta del cliente hacer esta operación al efectuar el corte. La calidad “sin seleccionar” se define como producto normal de una línea de estañado electrolítico.
Una línea de estañado electrolitito lleva un equipo auxiliar muy complejo, mas en realidad que la línea misma, pasa algo parecido a los icebergs, no se ve la parte hundida. El equipo eléctrico y electrónico, controles, bombas, tanques de electrolito, equipos de purificación, sistemas de agua y vapor, aire, etc., es de gran importancia y normalmente se encuentra instalado en subterráneos. La potencia electriza instalada es también muy fuerte.
La velocidad de la banda durante el estañado es función de la corriente eléctrica disponible para la electrolisis, del estado del electrolito, del tamaño y espesor del material, de la deposición de estaño que se desea obtener y de otros factores.
3.- TFS
Como consecuencia del aumento de precio del estaño y riesgo de ver las fuentes de aprovisionamiento del mismo en peligro, durante el último tercio del siglo pasado se desarrolló un producto sustitutivo de la hojalata, el TFS o chapa cromada. Este material suscitó pronto un interés que ha ido aumentando con el paso del tiempo. Su ventaja radica en que es una opción perfectamente valida para la fabricación de tapas, fondos, accesorios y envases embutidos, y ligeramente más barato que la hojalata.
El TFS esta constituido por un soporte idéntico al de la hojalata: el acero. Aunque la protección esta asegurada, no por una ligera capa de estaño aplicada por deposición electrolítica y por una película de pasivación, sino por un revestimiento mixto de cromo y oxido de cromo
En la siderurgia es frecuente fabricar el TFS sobre una instalación mixta, que puede producir hojalata o chapa cromada con una serie de cambios no muy complejos, que se realizan en un tiempo moderado. La aplicación de cromo se realiza también por sistema electrolítico. En la figura nº 10 se aprecia la parte especial de una línea para la fabricación de chapa cromada
No entramos en detalle en su proceso de obtención, pues como ya hemos indicado el acero base es el mismo que para la hojalata, y la línea de recubrimiento sigue una secuencia análoga a la de estañado.
Finalmente se debe mencionar la importante participación de las grandes compañías fabricantes de envases han tenido en los desarrollos habidos en la fabricación de acero para hojalata, en la fabricación de la hojalata en si, en otros materiales alternativos como TFS, y claro esta, en su utilización.
En la industria como a evolucionado la hojalateria
buenas necesitaría saber metos de analisis para el desprendimiento de estaño.
Me gustaría saber como se da la eliminación del estaño de la hojalata para su reciclaje.
Hola! Busco proveedores de envases de hojalatas para leche en polvo.
Muchas gracias.
Yesica Dilernia
HOLA ESTOY INTERESADO EN COMPRAR HOJALATA 0 18 TIENE QUE SER LIMPIA POR ANBOS LADAS PUEDE SER EN ROLLOS O EN CALUGAS DE UN METO PR UN METRO ES PARA LAS PATES DE ADENTRO DE LAS CAJAS
Hola, necesito cortar círculos de hojalata más o menos del tamaño de una moneda. Que herramienta debo utilizar?? Algo que pueda cortar unas 10000 unidades al año.