Introduction:
Metal cans are widely used as packaging for food and other products due to their durability and ability to protect the contents from external factors. However, one of the most significant challenges facing metal cans is corrosion. Corrosion can compromise the integrity of the package and affect the quality and safety of the packaged product. In this article, we will explore various strategies and preventive measures to avoid corrosion of metal cans.
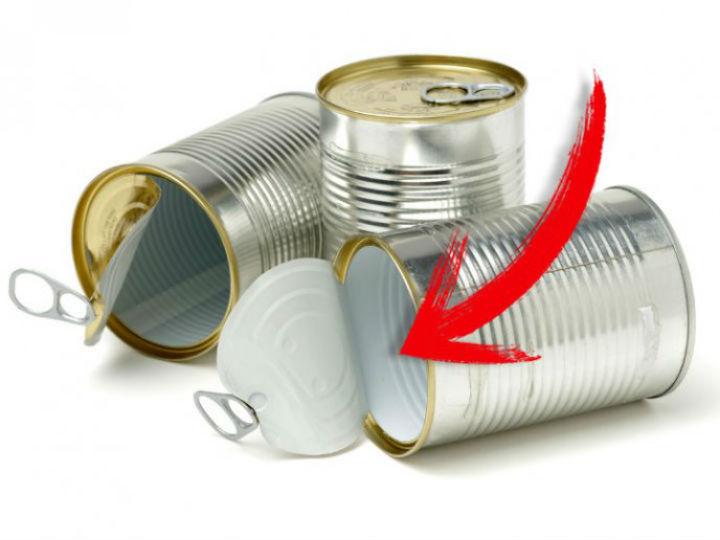
- Proper selection of materials:
It is essential to select high quality and corrosion resistant materials for the manufacture of metal cans. The most common materials used are tin-coated steel (tinplate) and aluminum. These materials offer good corrosion resistance, but it is important to ensure that they meet established technical specifications and quality standards. - Internal coating:
Internal coating of metal cans is one of the best solutions to prevent or reduce corrosion. The use of suitable coatings has made it possible to extend the use of cans to new products, even those that are highly aggressive. The thickness of the internal coating is a crucial factor affecting the performance of the coated can. For non-aggressive foods, such as apricots or beans, a thickness of 4-6 μm is recommended, while for more corrosive products, such as tomato concentrate, layers of 8-12 μm are needed to avoid interaction between the can and its contents. - Moisture control:
Moisture is a key factor that can accelerate corrosion of metal cans. It is important to ensure that cans are stored in dry conditions and to avoid prolonged exposure to moisture. Storage rooms should be separated from production areas where humidity may be high, such as cleaning areas or steam rooms. In addition, measures should be taken to prevent leakage of liquids from other nearby cans, as they can act as aggressive electrolytes and cause secondary corrosion. - Temperature control:
Temperature extremes can affect the corrosion resistance of metal cans. It is important to avoid prolonged exposure to high temperatures or sudden temperature fluctuations. Cans should be stored in temperature-controlled conditions to minimize the risk of corrosion. - Proper maintenance:
Regular maintenance of metal cans is essential to prevent corrosion. This involves periodic inspections to detect possible damage to the internal coating, such as cracks or spalling. If problems are detected, corrective action should be taken immediately to prevent the spread of corrosion.
Conclusions:
Corrosion of metal cans is a common but avoidable problem. Through proper selection of materials, use of quality internal coatings, humidity and temperature control, and regular maintenance, it is possible to prevent corrosion and ensure the durability and safety of metal cans. The industry continues to research and develop new technologies and materials to improve the corrosion resistance of cans and ensure the quality of packaged products.