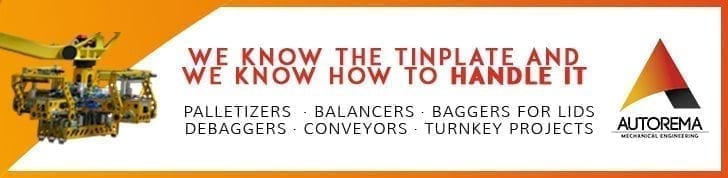
HERSTELLUNG UND EIGENSCHAFTEN VON WEISSBLECH
In diesem Dokument werden die verschiedenen Stufen der Herstellung von Weißblech, von der Gewinnung des Ausgangsstahls und seiner verschiedenen Sorten bis hin zu den aufeinanderfolgenden Sequenzen der Verzinnung von Weißblech, detailliert erläutert.
INDEX
Einführung
1.- Herstellung von StahlN
1.1.- Herstellung des Grundstahls
1.2.- Fertigungsablauf
1.3.- Zusammensetzung des Grundstahls
1.4.- Arten von Basisstahl
2.- Verzinnen
2.1- Zinn
2.2.-Elektrolytische Verzinnung
3.- TFS
EINFÜHRUNG IN WEISSBLECH
Weißblech ist ein Material, dessen Erfindung zwar aus der Antike stammt, das aber erst im letzten Jahrhundert seine maximale Entwicklung erreichte. Es waren die Vereinigten Staaten, die die treibende Kraft dieser Industrie waren und in den 1970er Jahren ihr höchstes Aktivitätsvolumen in diesem Land erreichten. Dann sorgten der große Einsatz von Getränkebehältern, die in Nordamerika Aluminium als Rohstoff verwendeten, die Verwendung von alternativen Behältern und die Veralterung der amerikanischen Stahlindustrie für den Rückgang dieses Marktes.
Das Gleiche geschah in anderen Teilen der Welt nicht. Europa war in der Lage, seine Stahlindustrie rechtzeitig zu modernisieren und seine Wettbewerbsfähigkeit zu erhalten, und konnte so der Herausforderung durch Aluminium erfolgreich widerstehen. Die Vielfalt der Verpackungsmöglichkeiten machte der Branche jedoch zu schaffen, die darauf mit einer Reihe von Fusionen erfolgreich reagierte und so ein hohes technisches Niveau halten konnte.
Auch in anderen geografischen Gebieten wie Südamerika, Fernost und Asien konnte der Markt für Weißblech und andere beschichtete Produkte eine gute Marktposition behaupten.
Heute ist es immer noch ein wichtiger Sektor weltweit, wenn auch im ständigen Konkurrenzkampf. Es lohnt sich also, ein wenig über die Herstellung dieses Materials zu wissen.
1.- HERSTELLUNG DES GRUNDSTAHLS
Weißblech besteht normalerweise zu 99 % oder mehr aus Stahl und ist daher im Wesentlichen ein Stahlprodukt. Der Herstellungsprozess beginnt eigentlich im Hochofen und in der Zinnschmelze, aber in der Praxis wird davon ausgegangen, dass er mit der Stahlerzeugung beginnt. In diesem Moment wird nämlich die Zusammensetzung und Art des herzustellenden Stahlblocks entschieden, die seine zukünftige Verwendung als Walzprodukt bestimmt. Die Basisrohstoffe für die Herstellung von Weißblech sind daher Stahl und raffiniertes Zinn.
1.1.- Herstellung des Grundstahls.
Es gibt zwei grundlegende Verfahren zur Gewinnung von Rohstahl in flüssigem Zustand: aus (a) Eisenerz und b) Altmetall.
A.- Aus Eisenerz (Verhüttungsprozess): Eisenerz ist ein Gestein, das aus Eisenoxiden und verschiedenen anderen Mineralien (Ganggestein) besteht. Die im Schmelzprozess verwendeten Erze und Schrotte sind zunächst voller Verunreinigungen. Eisen kommt in der Natur nie in einem reinen Zustand vor, sondern meist in Form von Oxiden und Sulfiden.
Bei dem im Hochofen entwickelten industriellen Verfahren ist es das Ziel, ein möglichst eisenreiches Produkt zu erhalten, in dem aber immer auch andere Bestandteile vorkommen werden. Unter den parasitären Materialien haben viele eine niedrigere Verbrennungs- und Verdampfungstemperatur als Eisen und verschwinden beim Erhitzen des Erzes, oder sie haben eine geringere Dichte als Eisen und schwimmen auf dem schmelzenden Metall. Um Eisenverbindungen in Form von Eisen- (FeO), Magnet- (Fe3O) und Eisen(III)-Oxiden (Fe2O3) von Sauerstoff zu befreien, muss man sich die Leichtigkeit zunutze machen, mit der Kohlenstoff mit Sauerstoff reagiert.
Kohlenstoff ist bei seiner Verbrennung ein großer Verzehrer von Sauerstoff, der ihn aus der Luft, aber auch aus dem Oxid zu den Verbindungen CO und CO2 (Kohlenmonoxid und Kohlendioxid) aufnimmt. Bei diesem Vorgang hinterlässt der überschüssige Kohlenstoff Spuren von Kohlenstoff in Verbindung mit Eisen (3 bis 6 %). Dieses im Hochofen erzeugte Material wird als „Schmelze“ bezeichnet.
Um den Kohlenstoff loszuwerden, kann in einem ergänzenden Arbeitsgang durch Zugabe von Sauerstoff CO und CO2, Kohlendioxidgase, gebildet werden. Dieser Sauerstoff kann auch mit anderen in der Schmelze enthaltenen Elementen reagieren, wie z.B. Mangan unter Bildung von Manganoxid (MnO), Kieselsäure (SiO2), Tonerde (Al2O3)… All diese Vorgänge werden zunächst im Hochofen und dann, wie wir später sehen werden, in der Raffination durchgeführt.
Zusammenfassend kann man sagen, dass in einem Hochofen, nach einer Phase der Erzaufbereitung in der Agglomerationswerkstatt, das Eisen im Hochofen mit Hilfe eines Brennstoffs gewonnen wird: Kohlenstoff (Koks). Es wird noch kein reines Eisen gewonnen, sondern ein flüssiges Gemisch aus Eisen (96%) plus Kohlenstoff (3%) aus dem nicht verbrannten Rest des Koks, plus einige Rückstände (Phosphor, Schwefel…) aus dem Ganggestein. Abbildung 1 zeigt einen Vertikalschnitt eines Hochofens.
Abbildung 1: Schematische Darstellung eines Hochofens
B.- Aus Schrott („elektrischer Prozess“): Die Komponenten, mit denen der Ofen beschickt wird, können von ordnungsgemäß ausgewählten Rohmaterialien (z. B. Maschinenteile) bis hin zu vorbereiteten, ausgewählten, zerkleinerten und kalibrierten Schrotten mit einem Mindesteisengehalt von 92 % reichen. Die gesamte Baugruppe wird in einem Elektroofen geschmolzen.
Roheisen oder Eisen aus dem Hochofen oder aus im Elektroofen geschmolzenem Schrott ist eine Eisen-Kohlenstoff-Legierung, spröde und mit einem hohen Gehalt an letzterem Element. Es kann auch ein hoher Schwefel- und Phosphorgehalt vorliegen. Die Stahlerzeugung ist der Prozess des Raffinierens, um die Anteile anderer Elemente als Eisen zu reduzieren und zu kontrollieren, um Barren mit der erforderlichen Reinheit, den erforderlichen Eigenschaften und der erforderlichen Verformbarkeit zu erzeugen. Im Allgemeinen werden diese Elemente und Verunreinigungen durch Oxidation mit Eisenoxid oder Sauerstoff reduziert und durch Flotation unter Zugabe von Materialien mit hohem Schmelzpunkt (z. B. Kalkstein) entfernt.
Derzeit werden vier grundlegende Verfahren zur Stahlgewinnung eingesetzt: das Siemens-Martin- oder offene Tiegelverfahren, das Bessemer- oder Thomas-Verfahren, das Sauerstoffaufblasverfahren und der Elektroofen. Letzteres wird selten für die Herstellung von Weißblech verwendet. Das erste und das zweite sind vielleicht die am häufigsten verwendeten pneumatischen Verfahren.
Offener Tiegel“-Prozess – Der Tiegel wird normalerweise mit geschmolzenem Eisen aus dem Hochofen, Schrott und kaltem Roheisen beschickt. Die Verunreinigungen werden oxidiert, was zur Bildung einer oxidierenden Schlacke führt. Der verwendete Brennstoff kann flüssig oder gasförmig sein. Die Kapazität eines Ofens dieses Typs kann bis zu 400 Tonnen betragen und durch die Verwendung von Bulk-Sauerstoff, der relativ sparsam ist, eine hohe Leistung haben, die bis zu 50 Tonnen/Stunde erreicht. Diese Öfen können fest oder kippbar sein.
Bessemer- oder Thomas-Verfahren – Bei diesem System werden die Verunreinigungen durch direktes Einblasen von Luft oder Sauerstoff durch die Metallschmelze mit Hilfe von Düsen am Boden des Konverters reduziert. Siehe Abbildung Nr. 2:
Bild Nr. 2: Stahlverarbeitung im Thomas-Konverter
Um den Kohlenstoff aus der Schmelze zu verbrennen, wird Luft oder ein Gemisch aus Luft und Sauerstoff durch das geschmolzene Metall geblasen, das in den Konverter gegossen wird, der eine große Stahlretorte mit einem Fassungsvermögen von 25 bis 50 Tonnen ist. Die feuerfesten Wände des Konverters bestehen aus basischem Dolomit, der für den Kalk, der zur Entfernung von Phosphor aus der Schmelze eingebracht werden muss, unempfindlich ist. Produktivität und Qualität können durch die Steuerung der Zusammensetzung des eingeblasenen Oxidationsgases, Luft, sauerstoffangereicherte Luft, Sauerstoff, Sauerstoff/Kohlendioxid-Gemisch usw. verbessert werden. So steigert die VLN-Variante (very low nitrogen) nicht nur die Produktion, sondern reduziert auch die normalerweise unerwünschte Einlagerung von Stickstoff in den Stahl.
Während des Prozesses können mehrere Phasen oder Perioden unterschieden werden. In der ersten Periode werden viele Funken erzeugt, verursacht durch die Verbrennung des Siliziums, die 2 bis 3 Minuten dauert. In der zweiten werden Flammen durch die Verbrennung von Kohlenstoff erzeugt, mit einer Dauer von 10 bis 12 Minuten. In der dritten wird durch den Ausstoß von Gasen, die durch das anschließende Blasen und die Verbrennung des Phosphors verursacht werden, charakterisiert, sein Intervall beträgt 3 bis 5 Minuten.
Im Laufe des Prozesses werden in der Regel verschiedene feste Elemente zugegeben, wie z. B.: Kalk, Schrott, Ferromangan oder spiegelndes Roheisen, je nach den Bedürfnissen.
Es gibt ein System, das Duplex genannt wird, was auf die Herstellung von Weißblechstahl angewandt, die Kombination des Bessemer-Säure-Verfahrens mit dem einfachen offenen Tiegelverfahren bedeutet. Im Konverter findet die Hauptreinigung statt, während im zweiten Teil des Prozesses die Phosphorreduktion erfolgt.
Überlegenes Sauerstoff-Injektionsverfahren. Das Bessemer-Verfahren ist vor allem wegen seiner geringen Installationskosten und seiner Flexibilität im Betrieb weit verbreitet, hat aber große Einschränkungen in Bezug auf die Endqualität, da es ein Rohmaterial mit hohem Phosphorgehalt und Einschränkungen bei der Verwendung von Schrott erfordert. Diese Schwierigkeiten haben einige Hersteller stark beeinträchtigt, was zur Entwicklung von überlegenen Sauerstoffinjektionsverfahren geführt hat, die es ermöglichen, Stähle von guter und konstanter Qualität zu erhalten, mit niedrigem Stickstoff- und hohem oder niedrigem Phosphorgehalt, je nach Bedarf. Es gibt drei Systeme, die häufig für laminierte Materialien verwendet werden, und sie heißen LD, DDAC und KALDO.
Der LD-Prozess war der erste, der auf der Verfügbarkeit von Sauerstoff in großen Mengen basierte. Sie besteht darin, die Einblasung von Luft von unten in einen Bessemer-Konverter durch die Einblasung eines Sauerstoffstrahls mit hohem Druck von oben zu ersetzen, der eine starke Umwälzung und damit eine sehr schnelle Oxidation der Verunreinigungen bewirkt. Es ist ein schneller und effizienter Prozess, mit Anfangsinvestitionen, die nicht viel höher sind als beim Bessemer-Verfahren, es reduziert Wartungsprobleme und produziert ein Material mit niedrigem Stickstoffgehalt, wobei eine seiner Einschränkungen die Verwendung von Eisen mit niedrigem oder mittlerem Phosphorgehalt ist. Dieses System wurde von zwei Firmen mit Sitz in Linz und Donawitz entwickelt. Aus den Anfangsbuchstaben dieser Städte ergibt sich der Name des LD-Verfahrens.
DDAC ist genau derselbe Prozess wie oben, außer dass Kalk zusammen mit dem Sauerstoff injiziert wird. Es ist eine Technologie französischen Ursprungs
Das KALDO-Verfahren wurde zuerst in Schweden entwickelt und verwendet einen rotierenden und kippenden Tiegel oder Ofen, mit der Anwendung eines Sauerstoffstrahls an der Oberseite und der Zugabe von Kalk durch Injektion oder in Stücken.
Sauerstoffprozesse sind vielseitig und erlauben die Verwendung von angemessenen Mengen an Erz und Schrott, wobei phosphor- und stickstoffarmer Stahl mit guten mechanischen Eigenschaften erzeugt wird.
Gießen des Stahls – Nachdem der Stahl durch eines der oben beschriebenen Verfahren gewonnen wurde, muss er, solange er sich noch im Konverter und in einem flüssigen Zustand befindet, durch Gießen in einen festen Zustand überführt werden. Industriell werden zwei Gießverfahren unterschieden. Am klassischsten ist die Umwandlung in Barren („Barrenguss“) oder das „Stranggussverfahren“.
Kokillenguss – Dies ist das konventionelle Verfahren. Mittels einer Pfanne wird der geschmolzene Stahl in Kokillen gegossen, aus denen nach dem Erkalten handliche Blöcke entstehen, mit denen die nachfolgenden Arbeitsgänge gespeist werden.
Strangguss – Dies ist das modernste Verfahren zur Herstellung von Platten. Die Hauptvorteile sind die Herstellung von Halbzeugen mit sehr hoher Qualität, die Möglichkeit, die Produktionskosten zu senken und die Produktivität des Stahlwerks zu erhöhen. Tatsächlich sind die Arbeitsgänge dank dieses Systems weniger und einfacher als beim Kokillenguss. . Sie verbietet die Verwendung von Blöcken für Stähle, die zum Walzen bestimmt sind. Siehe Abbildung Nr. 3:
Abbildung Nr. 3: Strangguss
Beim Stranggießen wird der Inhalt des Konverters mittels einer Schöpfkelle gleichmäßig und ohne Unterbrechung in eine gekühlte bodenlose Kokille gegossen, deren Querschnitt dem der gewünschten Platte entspricht. Anschließend durchläuft es eine Reihe von Walzen zum Glätten, und schließlich werden die Platten mit einem Autogenbrenner auf die gewünschte Länge geschnitten. Auf diese Weise erhalten wir Platten (Brammen) mit einer Länge zwischen 5 und 20 Metern, einer Breite bis zu etwas mehr als einem Meter und einer Dicke von etwa 20 cm.
1.2.- Fertigungsablauf.
Abbildung 4 zeigt eine Abfolge der verschiedenen Vorgänge oder Phasen bei der Herstellung der Stahlplatten, die das grundlegende Rohmaterial in den Weißblechherstellungsanlagen sein werden.
Abbildung Nr. 4: Herstellung von Stahlplatten
Beim Blockgussverfahren wird nach dem Schmelzen des Stahls zu Blöcken als erster Arbeitsgang das Walzen des Blocks zu einer Bramme durchgeführt. Dieser Vorgang wird üblicherweise in reversierbaren, doppelhohen Walzwerken durchgeführt. Die so genannten Universal-Typen haben Zylinder oder Seitenwalzen, die gleichzeitig die 4 Seiten des Barrens bearbeiten, wodurch der Vorgang des Drehens des Barrens um seine Achse in dieser Phase entfällt.
Das Endprodukt dieses Vorgangs, die Bramme, ist 125 bis 230 mm dick, die ungefähre Breite des schließlich gewünschten Weißblechs, und eine Länge, die von der Größe des ursprünglichen Barrens abhängt.
Die sowohl beim Stranggießen als auch beim Blockwalzen erzeugten Brammen werden für die Behandlung beim Warmwalzen vorbereitet.
Das Warmwalzen ist der nächste Schritt, obwohl es in der Regel eine Zwischenstufe gibt, die aus dem Abkühlen und Lagern der Bleche, einem Selektionsprozess, einer Oberflächenvorbereitung (Flämmen) und einer Erwärmung des Blechs auf eine zum Walzen geeignete Temperatur besteht. Die Eliminierung dieser Zwischenstufe erfordert eine sehr präzise Programmierung und eine sehr hohe technologische Kapazität, die die Fehlerfreiheit der Platten oder Brammen gewährleistet. Abbildung Nr. 5 zeigt die verschiedenen Phasen des Warmwalzens.
Bild Nr. 5: Warmwalzprozess
Die Oberflächenvorbereitung erfolgt in der „Entzunderungsmaschine“, in der das Blech einer Ablösung von Eisenoxiden und Verunreinigungen unterworfen wird, die durch einen schwachen Walzdruck erreicht wird, wobei diese durch die Einwirkung von Wasser mit hohem Druck abgelöst werden. Die Platte wird auf eine Temperatur von 880º C erhitzt. Es ist notwendig, diese Oxidschicht zu entfernen, da sie das Laminat beschädigt, da sie einen schnellen Verschleiß der Zylinder, Schlieren auf dem Metall, Oxidverkrustungen und andere Herstellungsfehler (Brüche, Verrutschen, Falten…) verursacht.
Das Warmwalzwerk reduziert das Blech zu einem kontinuierlichen Band von etwa 2 mm Dicke. Sie besteht normalerweise aus zwei Abschnitten, einem Schruppabschnitt und einem Schlichtabschnitt. Es kann ein kontinuierlicher oder reversibler Typ sein, abhängig von der Kapazität der Anlage usw.
Die Raubzug besteht in der Regel aus 4 bis 6 Kästen, die die Ausgangsdicke der Platte um 25 bis 50 % pro Kasten reduzieren. Die Zielgerade hat 4 bis 7 Kisten, wobei die Dicke wiederum um 25 bis 30 % pro Kiste reduziert wird, mit Ausnahme der letzten Kiste, die nur um 10 % reduziert wird. Die maximale Geschwindigkeit dieses Vorgangs kann im Bereich von 100km/h liegen. Am Ausgang ist das Material 850º C heiß. Es folgt eine Abkühlung durch einen Wasservorhang bis 590º, wobei Spulen mit demselben gebildet werden.
Das produzierte Coil muss vor dem Kaltwalzen gebeizt und geschmiert werden. Dieser Vorgang wird normalerweise in einer Reihe von Tanks mit heißer verdünnter Schwefelsäure (nahe 100º C) durchgeführt, gewaschen, getrocknet und mit Palmöl oder einem anderen zum Kaltwalzen geeigneten Schmiermittel geschmiert. Die Beizlinie ist in der Regel mit einem Kreisschneider ausgestattet, der die Kanten schneidet und damit sicherstellt, dass sie für die Kaltreduktion oder das Kaltwalzen geeignet sind. Außerdem wird damit die maximale Breite des Weißblechs eingestellt, die auch die besten wirtschaftlichen Ergebnisse liefert. Siehe Abbildung Nr. 6.
Bild Nr. 6: Kaltwalzen, Glühen und Dressierwalzen von Basisstahl
Der nächste Arbeitsgang ist das Kaltwalzen, das in kontinuierlichen (Tandems) oder reversierbaren Walzwerken durchgeführt werden kann. Bei diesem Vorgang werden Schmier- und Kühlmittel verwendet, und die resultierende Dicke kommt der gewünschten Oberfläche sehr nahe. Die Reduktion erfolgt daher um 1,8 oder 2 mm auf ein Maß zwischen 0,15 bis 0,3 mm, etwa entsprechend der Endgröße des zu produzierenden Weißblechs.
Das erhaltene Coil besteht aus einem sehr harten Material, das starken Spannungen ausgesetzt ist, und benötigt eine geeignete Behandlung, um ihm die notwendige Bearbeitbarkeit zu verleihen, was eine Rekristallisation des Stahls bewirkt. Diese Behandlung wird Glühen genannt und beinhaltet das Erhitzen des Metalls in einer reduzierenden Atmosphäre, um jegliche Oxidation zu vermeiden (Gemisch aus Stickstoff und Wasserstoff) und kann kontinuierlich (kontinuierliches Glühen) oder in Chargenglühöfen (Chargenglühen) erfolgen.
Kontinuierliches Glühen: Das Band zirkuliert bei einer Temperatur von 630º C durch einen Ofen, wobei jede Stelle des Materials mindestens 1,5 Minuten im Ofen verbleibt. Das kontinuierliche Glühen hat eine Reihe von Vor- und Nachteilen, wie z.B.:
Vorteile:
– Reduktion von Materialien „im Prozess“ der Produktion.
– Verkürzung der Fertigungszeiten.
– Verbesserung der Qualität der hergestellten Produkte:
o Konstante und kontinuierliche Erwärmung über die gesamte Länge der Spule, was zu homogeneren mechanischen Eigenschaften führt.
o Schneller Zyklus, wobei feine gleichachsige Körner erhalten werden, daher ein isotropes Metall und überlegene mechanische Eigenschaften, wie z. B. die Verbesserung der Elastizitätsgrenze.
o Bessere Korrosionsbeständigkeit. Der schnelle Zyklus lässt nicht zu, dass Elemente wie Kohlenstoff, Mangan, Phosphor… an die Oberfläche des Materials wandern, wie es beim Basis- oder Glockenglühen geschieht.
o Ermöglicht die Verwendung einer Stahlzusammensetzung vom Typ MR, die weniger mit härtenden Elementen belastet ist: Kohlenstoff, Mangan-…. (Durchlaufglühen = 0,08 % Kohlenstoff, Grundglühen = 0,10/0,13 % Kohlenstoff), was Arbeitsgänge wie Schweißen, Spezialitäten… begünstigt.
Benachteiligungen:
– Fertigung:
o Schwierige Programmierung der Aufträge, da die maximale Variation in der Breite zwischen aufeinanderfolgenden Coils in der Größenordnung von 50 mm und in der Dicke in der Größenordnung von 10 % liegt.
o Feinfühlige Führung der Leitung. Gefahr des Riemenbruchs im Ofen. Es ist ein wichtiger Halt. Die Elastizitätsgrenze des Bandes bei der Glühofentemperatur ist niedrig (ca. 30 N/mm2).
o Unmöglichkeit von Leitungsstopps.
– Verwendung:
o Feinkristallographie, die ein weniger duktiles Metall erzeugt, mit schwacher Anisotropie, was das Ziehen beeinträchtigt.
o Gefahr des Vorhandenseins von Lüder-Linien.
Glühen in einer Glocke: Mehrere gestapelte Coils werden mit einer Glocke in einer reduzierenden Atmosphäre bei einer Temperatur von 680º C für mindestens 85 Stunden abgedeckt, aufgeteilt in 32 Stunden Erwärmung, 34 Stunden Abkühlung unter einer Glocke bis 170º und 19 Stunden beschleunigte Abkühlung im Freien. Siehe Abbildung Nr. 7
Abbildung Nr. 7: Schema des Glockenglühprozesses.
In beiden Fällen ist es unerlässlich, die Rückstände der zuvor verwendeten Schmier- und Kühlmittel vorher zu beseitigen, wobei die dafür verwendete Methode mit der Art des durchzuführenden Glühens übereinstimmt, normalerweise durch elektrochemische Mittel, wie ein auf 95 ºC erhitztes Entfettungsmittelbad oder mechanisch, mit beidseitigem Bürsten.
Als nächstes folgt der Vorgang des Anlassens, der Oberflächenbehandlung oder der Endbearbeitung (Anlasswalzen oder Dressieren). Es wird durch eine Reduktion oder Laminierung hergestellt, ohne Schmiermittel und sehr leicht, die in der Regel nicht mehr als 2% in der Dicke. Dazu wird ein Walzwerk verwendet, das aus zwei Boxen besteht. Das Band erfährt beim Durchlaufen zwischen den Zylindern unter der Wirkung des festgelegten Drucks und Zugs eine oberflächliche Veränderung der Struktur, wodurch eine Erhöhung der Härte der Oberflächenschicht erreicht wird, aber die innere Weichheit erhalten bleibt.
Kurz gesagt, dieser Vorgang verleiht dem Band die gewünschte Härte, eine gute Abflachung und eine Oberflächengüte des Materials, die von der Rauheit der in den Walzwerkskästen verwendeten Walzen abhängt. Durch die Kombination der Oberflächenbeschaffenheit der Zylinder der Dosen dieser Kaschierung und das abschließende Umschmelzen des Zinns nach dem Verzinnungsvorgang werden unterschiedliche Oberflächenbeschaffenheiten des Weißblechs erreicht. Die wichtigsten Arten von Endbearbeitungen sind:
Glänzende Oberfläche: Um diese Oberfläche zu erreichen, ist es wichtig, eine Spiegelpolitur auf den Zylindern zu erzielen. Zusätzlich ist es notwendig, die Verzinnung aufzutragen. Diese Art der Ausführung ist, zusammen mit dem Stein, die am meisten gewünschte.
Steinfinish: Die Zylinder werden in zwei Durchgängen mit einer speziellen Kornschleifscheibe geschliffen, wodurch das Produkt ein gestreiftes Aussehen erhält. Wie im vorherigen Fall wird die Zinnschicht umgeschmolzen, was ebenfalls für Brillanz sorgt.
Matte Oberfläche: Sie hat eine schwach reflektierende Oberfläche. Um dies zu erreichen, werden die Zylinder kugelgestrahlt und der Umschmelzvorgang nach dem Verzinnen entfällt.
Bei doppelt reduziertem Weißblech erfolgt die letzte Zerkleinerung, indem der Anlassvorgang durch eine weitere Zerkleinerung bzw. Walzung um ca. 33% ersetzt wird, mit einer anschließenden Verlängerung des Materials um einen ähnlichen Prozentsatz, diesmal unter Verwendung von Oberflächenschmiermitteln. Dadurch erhält das Weißblech hohe mechanische Eigenschaften bei geringer Dicke.
Es ist gängige Praxis, die Spulen vor dem Verzinnen vorzubereiten. Sie besteht hauptsächlich aus dem Schneiden der Kanten und der Beseitigung von Abschnitten minderer Qualität oder von Kalibern außerhalb der Spezifikation, wodurch Coils mit optimaler Größe für die Verzinnungslinie entstehen.
Bei der elektrolytischen Verzinnung durchläuft das vorbereitete Material kontinuierlich die Arbeitsgänge elektrolytisches Reinigen, elektrolytisches Beizen, elektrolytisches Abscheiden von Zinn, Zinnumschmelzen (Fließschmelzen), Passivierungsbehandlung und Schmierung. Nach dieser Reihe von Arbeitsgängen kann das Produkt in Tafeln auf die bestellte Größe (Länge, da die Breite bei der Vorbereitung der Coils angegeben wurde) geschnitten, inspiziert, sortiert und verpackt werden; oder es kann für den Versand an den Kunden oder zum Schneiden usw. auf einer separaten Schneidelinie aufgewickelt werden. Es ist normal, auf der gleichen Linie die Auswahl des Materials vor dem Verpacken vorzunehmen. Auf diese Punkte werden wir später noch einmal genauer eingehen.
1.3.- Zusammensetzung des Grundstahls.
Für Weißblech ist der Grundstahl im Wesentlichen ein unlegierter Stahl mit niedrigem Kohlenstoffgehalt, mit einer generischen Zusammensetzung des folgenden Typs:
– Kohlenstoff 0,04 – 0,15 %.
– Silizium 0,08 % maximal
– Schwefel 0,015 – 0,05 %.
– Phosphor 0,01 – 0,14 %.
– Kupfer 0,02 – 0,20 %.
– Mangan 0,20 – 0,70 %.
– Stickstoff 0,001 – 0,025 %.
Aufgrund der Verwendung von Schrott in der Stahlherstellung können andere Elemente wie Nickel, Chrom und Zinn vorhanden sein, es werden jedoch keine anderen Elemente absichtlich hinzugefügt. Die einzigen Ausnahmen sind Phosphor und Stickstoff, die besondere Eigenschaften aufweisen können. Die Verwendung von Kupfer zur Erhöhung der Korrosionsbeständigkeit und von einigen Karbiden zur Kontrolle der Alterung ist nicht mehr üblich.
Der Einfluss einiger Elemente auf den Grundstahl von Weißblech wird in den folgenden Absätzen in groben Zügen dargestellt.
– Kohlenstoff: Kohlenstoff erhöht die Streckgrenze, Zugfestigkeit und Härte, verringert die Dehnung und Duktilität. Innerhalb der für Weißblech üblichen Grenzen sind Schwankungen im Gehalt dieses Elements von geringer Bedeutung, da andere Elemente einen viel größeren Einfluss haben.
– Silizium: Es kommt in Weißblech als Restelement vor, sehr selten wird es als Desoxidationsmittel zugesetzt. Härtet leicht auf und beeinträchtigt in einigen Fällen die Korrosionsbeständigkeit.
– Schwefel: Bei dieser Stahlsorte werden die Auswirkungen von Schwefel durch Mangan, das immer vorhanden ist, bekämpft. Aufgrund seiner Auswirkungen auf die Duktilität, die Oberflächenqualität und die Korrosionsbeständigkeit werden jedoch alle Anstrengungen unternommen, ihn im Rahmen der wirtschaftlichen Möglichkeiten auf ein Minimum zu reduzieren.
– Phosphor: Es ist ein Element, das die Härte und Korrosionsbeständigkeit stark beeinflusst. Wenn die Möglichkeit von Säurekorrosion besteht, muss der Gehalt in bestimmten Grenzen gehalten werden, und der Gehalt wird erhöht, wenn eine höhere Stahlfestigkeit erforderlich ist und keine Korrosionsgefahr besteht.
– Kupfer: Es erhöht zwar den Widerstand, aber nicht effektiv in den üblichen Grenzen. Ein Überschreiten dieser Grenzwerte erhöht die atmosphärische Korrosionsbeständigkeit, kann aber die innere Korrosionsbeständigkeit verringern, so dass für die meisten Weißblechsorten ein maximaler Kupfergehalt angegeben ist.
– Mangan; Es wird bei der Herstellung von Stahl für Weißblech verwendet, hauptsächlich um mit anderen Elementen, hauptsächlich Schwefel, zu reagieren und sie unwirksam zu machen.
– Stickstoff: In Bessemer-Stählen ist er in Anteilen von mehr als 0,01% ein normaler Bestandteil und wurde immer als nachteilig angesehen. In der Folge wurde festgestellt, dass seine absichtliche Zugabe die Festigkeit des Stahls stark erhöht, ohne die Korrosionsbeständigkeit nennenswert zu verändern, obwohl es die Alterung beeinflussen kann. Durch die Entwicklung von Sauerstoffverfahren (LD, etc.) ist es möglich geworden, den Gehalt dieses Elementes genau zu kontrollieren, wodurch eine gleichmäßige und kontinuierliche Qualität erreicht wird.
– Nickel: In zulässigen Mengen beeinträchtigt es nicht die physikalischen oder mechanischen Eigenschaften von Weißblech, aber es beeinträchtigt die chemischen Eigenschaften, insbesondere die Korrosion in bestimmten Arten von Verpackungen. Das gleiche gilt für Chrom.
– Zinn: Dieses Element hat eine hohe Löslichkeit in Eisen oder Stahl, und Prozentsätze von mehr als 10 % sind notwendig, damit sich eine zweite Phase bilden kann. Bei normalen Werten hat es keinen Einfluss auf die metallographische Struktur. Sein Vorhandensein führt zu einer progressiven Erhöhung der Elastizitätsgrenze und der Zugbruchgrenze bei gleichzeitiger Verringerung des Elastizitätsmoduls. Es ist wichtig zu beachten, dass geringe Mengen von Zinn in kupferhaltigen Stählen zu ernsthaften Schwierigkeiten bei der Warmumformung des Stahls führen können.
Bei der Stahlherstellung werden manchmal praktische Regeln verwendet, um die Auswirkungen von Legierungs- und Restelementen auf die mechanischen Eigenschaften von Weißblechstahl zu berechnen. Einer der gebräuchlichsten ist der Strohmayer-Index, der berechnet wird, indem man den Stickstoffgehalt mit 5 multipliziert, den Phosphor addiert und die Summe mit 1000 multipliziert.
1.4.- Arten von Basisstahl
Traditionell gibt es drei Grundtypen von Weißblech, obwohl es bei den heutigen Technologien manchmal schwierig ist, bei den klassischen Typen zu bleiben. Diese sind:
Typ L: Es ist ein kaltgewalzter Stahl, der aus offenen Tiegelöfen stammt (Siemens Martin). Es hat einen geringen Gehalt an Metalloiden und Restelementen, besonders begrenzt an Phosphor, mit der folgenden Zusammensetzung:
Kohlenstoff 0,05 – 0,13 %.
Mangan 0,30 – 0,60 %.
Schwefel 0,04 max.
Phosphor 0,015 max.
Silizium 0,010 max.
Kupfer 0,06 max.
Nickel 0,04 max.
Chrom 0,06 max.
Molybdän 0,05 max.
Arsen 0,02 max.
Stickstoff 0,02 max.
Es wird verwendet, wenn eine hohe Beständigkeit gegen sehr korrosive Produkte erforderlich ist.
Typ MR: Er ist der am häufigsten verwendete. Es ist vom gleichen Ursprung wie das vorherige, kaltgewalzt und wird in mäßig korrosiven Produkten verwendet. Ihre Analyse ist:
Kohlenstoff 0,05 – 0,15 %.
Mangan 0,30 – 0,60 %.
Schwefel 0,04 max.
Phosphor 0,020max.
Silizium 0,010 max.
Kupfer 0,20 max.
Typ MC: Es handelt sich um einen Stahl, der im Bessemer-Konverter oder Siemens-Martin-Ofen hergestellt wird. Er wird verwendet, wenn die Beständigkeit und der Inhalt des Behälters von geringer Korrosivität sind. Ihre Probenanalyse sieht folgendermaßen aus:
Kohlenstoff 0,05 – 0,15 %.
Mangan 0,25 – 0,60%.
Schwefel 0,04 max.
Phosphor 0,03 – 0,15 %.
Silizium 0,010 max.
Kupfer 0,20 max.
Es gibt auch einige Spezialstähle wie Typ D, Aluminium vergütet, die in besonderen Fällen des Tiefziehens verwendet werden.
Generell sind die Hersteller in Europa gezwungen, zu versuchen, spezialisierte Weißblechproduktionen zu eliminieren und damit wirtschaftliche und wettbewerbsfähige Verfahren zu finden, also versuchen sie, das Problem zu vereinfachen.
Wichtig im Hinblick auf die Korrosionsbeständigkeit ist auch die Oberfläche des Stahls, die zum Teil von der Art der Atmosphäre abhängt, die beim Glühen verwendet wird. Eine Atmosphäre, die Stickstoff, Wasserstoff, Kohlendioxid und Wasserdampf enthält, ergibt ein weniger beständiges Weißblech als ein trockener Stickstoff mit 4 bis 8 % Wasserstoff. Auch gelöste Zinn-Ionen haben im Allgemeinen eine hemmende Wirkung auf die Korrosion von Weißblech durch einige Produkte.
2.- VERZINNUNG
2.1.- Zinn
Wenn dieses Material für die Herstellung von Weißblech bestimmt ist, ist es logisch zu denken, dass es in längerem Kontakt mit Lebensmitteln sein wird und daher bestimmte Anforderungen in Bezug auf Verunreinigungen erfüllen muss. Die American Society for Testing and Materials (ASTM) klassifiziert in fünf Gruppen, jeweils mit folgenden Mindestzinngehalten: Güteklasse AA = 99,98 % Zinn, A = 99,80 %, B = 99,7 %, C-1 = 99,0 % und C-2 = 99,0 %. Das Minimum, das für die Herstellung von Weißblech spezifiziert ist, ist Grad A. Seine Analyse ist:
Zinn (Minimum) 99,80 %.
Antimon 0,04 %.
Arsen 0,04 %.
Wismut 0,015 % Wismut 0,015 % Wismut 0,015 % Wismut 0,015
Kupfer 0,03 %.
Eisen 0,015 % Eisen 0,015 % Eisen 0,015 % Eisen 0,015 % Eisen 0,015
Blei 0,05 %.
Nickel und Kobalt 0,015 %.
Silber 0,01 % Silber 0,01 % Silber 0,01 % Silber 0,01 % Silber 0,01 % Silber 0,01
Schwefel 0,003 % Schwefel 0,003 % Schwefel 0,003 % Schwefel 0,003 % Schwefel 0,003
Zink 0,001 % Zink 0,001 % Zink 0,001 % Zink 0,001 % Zink 0,001 % Zink 0,001
Cadmium 0,001 %.
Aluminium 0,001 %.
- 2.- Elektrolytische Verzinnung
Die Entwicklung dieses Verzinnungsprozesses war einer der wichtigsten Schritte in der Verzinnungsindustrie. Die elektrolytische Abscheidung von Zinn auf einem durchgehenden schmalen Band (Strip), begann 1930 in Deutschland, aber erst während des 2. Weltkrieges wurde die Technik aufgrund des Zinnmangels vor allem in den USA intensiv entwickelt.
Es gibt eine Reihe von technischen und wirtschaftlichen Gründen, die dazu geführt haben, dass elektrolytisches Weißblech den Markt von Koks-Weißblech oder heißem Weißblech, das die traditionelle Art der Herstellung war, verdrängt hat. Eine der wichtigsten ist die präzise Kontrolle der abgeschiedenen Zinnmenge und der Gleichmäßigkeit der Dicke. Eine weitere Möglichkeit ist die Verfügbarkeit von differentiellem elektrolytischem Weißblech, bei dem auf jeder Seite des Blechs eine unterschiedlich dicke Zinnschicht aufgebracht wird.
Wie wir bereits beim Anlassen des Grundstahls angedeutet haben, kann elektrolytisches Weißblech in verschiedenen Ausführungen hergestellt werden, wobei drei Ausführungen die gängigsten sind. „Bright“, das am häufigsten vorkommt, „matt“, bei dem der Grundstahl mit einer rauen Oberfläche verzinnt wird und das Zinn nicht umgeschmolzen wird, und schließlich „stone“, bei dem es sich um die gleiche Ausführung wie oben handelt, aber das Zinn umgeschmolzen wird, was eine glänzende, aber nicht reflektierende Oberfläche ergibt.
Es gibt grundsätzlich zwei Herstellungsverfahren, das saure und das alkalische bzw. basische Verfahren, wobei letzteres in zwei Varianten weit verbreitet ist, nämlich in horizontalen Halogenleitungen und alkalischen bzw. vertikalen Leitungen. Es gibt noch ein viertes Verfahren, das Fluoborate als Elektrolyt verwendet, aber es wird nur sehr wenig genutzt.
Die Linien, die das Säureverfahren verwenden, sind diejenigen, die den höchsten Prozentsatz an elektrolytischem Weißblech produzieren. Sie werden oft als Ferrostan bezeichnet, da dies der Name war, den U.S. Steel für sein Weißblech registrierte, mit vielen nachfolgenden Lizenznehmern seiner Technologie in der ganzen Welt.
Elektrolyte sind der empfindlichste Teil eines jeden Prozesses. In sauren Leitungen ist es zum Beispiel eine Lösung von Zinnsalzen in Säure, aber die gute Leistung als Elektrolyt hängt von den verschiedenen verwendeten Zusätzen ab, die drei Hauptziele haben, nämlich die Oxidation zu vermeiden, die Bildung von kompakten und nicht flockigen Ablagerungen zu begünstigen und die Benetzbarkeit zu verbessern.
Einige klassische Vorteile der Verwendung von alkalischem Elektrolyt sind, dass der Elektrolyt im Vergleich zu Stahl einfacher, leichter zu handhaben und nicht korrosiv ist, was die Anschaffungskosten der Geräte reduziert. Auch der vorbereitende Teil ist einfacher gestaltet.
Saure Anlagen haben den Vorteil, dass weniger Strom für die Verzinnung benötigt wird als alkalische Anlagen, es wird weniger Anodenfläche benötigt und der elektrische Wirkungsgrad ist bei der galvanischen Abscheidung höher. Alkalische Leitungen ergeben jedoch ein Weißblech mit besseren Korrosionsbeständigkeitseigenschaften.
Grob gesagt setzen sich die drei Linientypen aus folgenden Abschnitten zusammen:
Abwickeln
Vorbereitung
Verzinnen
Fertigstellung
Schneiden – Wickeln – Verpacken
Die Eingangs- oder Abwicklungssektion verfügt über die notwendige Ausrüstung für die Handhabung der Schwarzblechcoils und für die kontinuierliche Zuführung der Linie durch Schneiden des Anfangs und des Endes jedes Coils und das elektrische Verschweißen des Endes eines Coils mit dem Anfang des nächsten. Enthält Führungs- und Vorschubrollen, Spannrollen usw.
Zwischen der Abwickel- und der Vorbereitungssektion befindet sich eine Vorrichtung zum Speichern von Schwarzblechband, die dazu bestimmt ist, eine bestimmte Menge an Band zu akkumulieren, das die Linie speist, während das Coil in der vorherigen Abwickelsektion gewechselt und gespleißt wird. Es gibt mehrere Typen, vorwiegend Brunnen und „Akkordeon“.
Der Aufbereitungsabschnitt hat zwei Hauptziele, die Reinigung (Entfettung) und das Beizen. Die erste ist die Entfernung aller Reste auf der Bandoberfläche, die von Schmiermitteln, Kühlmitteln usw. stammen, während die zweite darauf abzielt, das auf beiden Seiten des Bandes anhaftende Eisenoxid zu entfernen.
Die Behandlung erfolgt in einer Abfolge von chemischen oder elektrochemischen Bädern, mit abwechselnden Wasserstrahl- und/oder Dampfwäschen. Das Layout und der Typ sind abhängig von der Linie. Zum Beispiel wird die Entfettung normalerweise in einer Reinigungsmittel- oder Alkalilösung durchgeführt. Bei Anlagen dieses Typs entfällt sie oder wird reduziert, da die Entfettung automatisch in der Verzinnungsabteilung erfolgt.
Der Verzinnungsabschnitt ist bei jedem Verfahren völlig unterschiedlich, wobei der des Halogenverfahrens die größte Fläche einnimmt, da sich das Band flach, normalerweise in 3 Ebenen, bewegt, während es bei den anderen beiden Systemen einer Sinus- oder Serpentinenform folgt.
Abbildung Nr. 9: Verzinnungslinie, Elektrolytbehälter und Anoden
Vor dem Verzinnen werden auf dem Schwarzblechstreifen die Markierungen angebracht, die dem Differentialzinnblech entsprechen. Einige Hersteller kennzeichnen den Grundstahl, damit bei späteren Schwierigkeiten mit dem Weißblech der Hersteller identifiziert werden kann. Diese Markierungen sind auf dem Blatt als solches nicht sichtbar, sie müssen im Labor gefunden werden.
Die Endbearbeitung umfasst verschiedene Schritte, die wichtigsten sind: Umschmelzen, Passivieren und Schmieren.
Der Zweck des Umschmelzens ist es, dem Weißblech eine glänzende Oberfläche zu geben, da die einfache galvanische Abscheidung von Zinn eine mikroraue Oberfläche mit einem matten Aussehen erzeugt. Dieser Schritt ist jedoch von grundlegender Bedeutung für Weißblech, das in Kontakt mit korrosiven Elementen kommen soll. Beim Umschmelzen bildet sich eine Schicht aus einer Eisen-Zinn-Legierung, die aufgrund der Schnelligkeit, mit der sie entsteht, sehr dünn ist. Daraus folgt, dass stumpfes Weißblech, das nicht umgeschmolzen wurde, nicht für solche Zwecke verwendet werden sollte, die das Vorhandensein einer Schicht aus einer Eisen-Zinn-Legierung erfordern.
Die Passivierung ist eine Eigenschaft von elektrolytischem Weißblech. In diesem Fall, insbesondere bei niedrigen Beschichtungen, ist es zweckmäßig, sie mit einer Schutzschicht zu versehen, die eine Oxidation verhindert, nicht nur während der Herstellung, sondern auch bei nachfolgenden Arbeitsgängen, wie z. B. dem Lackieren. Es ist auch notwendig, eine Oberfläche zu erhalten, die chemisch besser für Lithographie und Lackierung geeignet ist und eine gewisse Schutzhärte aufweist. Die Passivierung soll diesen Aspekt abdecken und besteht im Wesentlichen aus der Bildung einer Chromoxidschicht. Dabei kommen verschiedene chemische oder elektrochemische Verfahren zum Einsatz, die jeweils auf die Erzielung spezieller Eigenschaften ausgerichtet sind. Sie sind in der Regel unter dem Kürzel USS und einer dreistelligen Zahl bekannt, wobei die erste Ziffer die Art der Lösung angibt (1 = Chromsäure, 2 = Chromphosphat, 3 = Natriumdichromat, 4 = Natriumcarbonat), die zweite Ziffer die Polarität des Zinnblechs in der Lösung (0 = nicht-elektrolytisch, 1 = kathodisch, 2 = kathodisch/anodisch) und die dritte Ziffer in etwa die Höhe des verwendeten Stroms bezeichnet.
Es gibt drei Grundtypen der Passivierung, die da wären
– Passivierung 300: Sie wird durch ein chemisches Verfahren, durch Eintauchen in Natriumdichromatlösung, erreicht, wodurch eine Chromoxidschicht entsteht. Es ergibt gute Ergebnisse aus der Sicht der Lackhaftung. Es bietet einen schwachen Schutz gegen Sulfidierung. Diese Passivierung ist jedoch instabil. Seine Wirksamkeit nimmt mit der Zeit ab
– Passivierung 311Galvanik: Wird durch ein elektrochemisches Verfahren durch elektrolytische Abscheidung einer Schicht aus Chrom und Chromoxid in einem Bad aus Natriumdichromat gewonnen. Es ist die am häufigsten verwendete Passivierung. Sie hat eine günstige Ausbeute in Bezug auf die Lackhaftung, obwohl sie niedriger ist als die 300er Passivierung. Sie ist zeitlich viel stabiler als die 300er. Sie kann daher als Kompromiss zwischen der zeitlichen Stabilität und der Qualität der Haftung von lithografischen Systemen angesehen werden.
– Passivierung 312: Sie wird nach dem gleichen System wie 311 erhalten. Es handelt sich dabei um eine verstärkte 311-Passivierung. Es wird hauptsächlich für Weißbleche verwendet, die gegen Schwefelprodukte beständig sein müssen, wie z.B. Fleisch, Suppen, Produkte für Hunde und Katzen… Seine Haftung auf Druckfarben und Lacken ist schlechter als die von 311.
Die verschiedenen Passivierungsbehandlungen wirken sich nicht nur auf die Haftung von Lacken, Schweißungen usw. aus, sondern führen auch zu verschiedenen Formen des Angriffs oder der Fleckenbildung, da das Weißblech dem Kontakt mit korrosiven Produkten oder Schwefelverbindungen ausgesetzt ist. Auch aus ästhetischen oder präsentationstechnischen Gesichtspunkten ist dieses Detail wichtig, z. B. bei Kondensmilch.
Abschließend führt der Schlichtbereich die Schmierung durch. Der Zweck dieses Schmiermittels ist nicht so sehr, das Weißblech selbst zu schützen, sondern die Passivierung und nicht die Eigenschaften dieser ist sehr leicht, so dass die am häufigsten verwendete Methode der Anwendung ist durch Elektro-Abscheidung, obwohl es durch Sprühen oder Tauchen durchgeführt werden kann. Normalerweise werden drei Arten von Ölen verwendet: Baumwollsamenöl, Dioctylsebacat und Dibutylsebacat, wobei letzteres am häufigsten verwendet wird. Die normale Menge an Schmiermittel liegt in der Größenordnung von 0,005 grs/m2. Die Trocknung des Schmierstoffs erfolgt in der Regel mit Hilfe von Dampf und Heißluftschlangen.
Der letzte Teil der Linie hängt von der Formation des Endprodukts und der zu erzielenden Produktivität ab, nicht von der Art der Linie (Säure, …). Wenn die Produktion ausschließlich in Coils erfolgt, wird nicht geschnitten, sondern es gibt eine Speichervorrichtung für das Band, um den Wechsel der Coils zu ermöglichen. Wenn die Produktion ausschließlich in geschnittenen Bögen erfolgt, ist die Speichereinrichtung nicht erforderlich. Beim Schneiden erfolgt die Selektion von Oberflächenfehlern, diese Kontrolle ist aufgrund der Geschwindigkeit der Anlage nicht sehr effizient, so dass das erhaltene Produkt als „unsortiert“ (unsortiert) eingestuft wird. Wenn Sie „Erste“ von „Zweiten“ trennen wollen, müssen Sie die Hilfsdienste einer Auswahlzeile nutzen. In diesem Bereich werden Off-Spec- und Pinhole-Bleche getrennt. Bei der Auslieferung von Coils ist es üblich, diese Trennung nicht vorzunehmen, wodurch die Ausbeute sinkt, und es obliegt dem Kunden, diesen Vorgang beim Schneiden durchzuführen. Die Qualität „unselektiert“ wird als normales Produkt einer elektrolytischen Verzinnungsanlage definiert.
Eine elektrolytische Verzinnungsanlage hat eine sehr komplexe Zusatzausrüstung, komplexer sogar als die Anlage selbst, es passiert etwas Ähnliches wie bei Eisbergen, man sieht den versunkenen Teil nicht. Elektrische und elektronische Geräte, Steuerungen, Pumpen, Elektrolytbehälter, Reinigungsanlagen, Wasser- und Dampfsysteme, Luft usw. sind von großer Bedeutung und werden normalerweise unterirdisch installiert. Die installierte elektrische Leistung ist ebenfalls sehr stark.
Die Bandgeschwindigkeit beim Verzinnen ist eine Funktion des für die Elektrolyse zur Verfügung stehenden elektrischen Stroms, der Beschaffenheit des Elektrolyten, der Größe und Dicke des Materials, der gewünschten Zinnabscheidung und anderer Faktoren.
3.- TFS
Als Folge der Verteuerung von Zinn und der Gefahr, die Bezugsquellen von Zinn in Gefahr zu sehen, wurde im letzten Drittel des letzten Jahrhunderts ein Ersatzprodukt für Weißblech entwickelt, das TFS oder verchromte Blech. Dieses Material weckte bald ein Interesse, das im Laufe der Zeit immer größer wurde. Sein Vorteil liegt darin, dass es eine durchaus brauchbare Option für die Herstellung von Deckeln, Böden, Zubehör und tiefgezogenen Behältern ist und etwas preiswerter als Weißblech.
Der TFS besteht aus einem Träger, der mit dem von Weißblech identisch ist: Stahl. Obwohl der Schutz nicht durch eine leichte, elektrolytisch aufgebrachte Zinnschicht und eine Passivierungsschicht gewährleistet wird, sondern durch eine Mischschicht aus Chrom und Chromoxid.
In der Stahlindustrie ist es üblich, TFS auf einer gemischten Anlage zu produzieren, die Weißblech oder Chromblech mit einer Reihe von nicht sehr komplexen Änderungen herstellen kann, die in einer moderaten Zeit durchgeführt werden. Die Applikation von Chrom erfolgt ebenfalls über ein elektrolytisches System. Abbildung 10 zeigt den speziellen Teil einer Linie für die Herstellung von verchromten Blechen.
Auf den Herstellungsprozess wird nicht näher eingegangen, da, wie bereits angedeutet, der Grundstahl der gleiche ist wie bei Weißblech und die Beschichtungslinie analog zur Verzinnung abläuft.
Abschließend sei noch die wichtige Beteiligung der großen Verpackungsunternehmen an den Entwicklungen bei der Herstellung von Stahl für Weißblech, bei der Herstellung von Weißblech selbst, bei anderen alternativen Materialien wie TFS und natürlich bei deren Verwendung erwähnt.
Mein Mann muss für ein Gartenhaus Blech zuschneiden. Interessant, wie Weißblech genau hergestellt und verbreitet werden kann. Am besten geht er aber in eine Spenglerei.
Ich wusste nicht, dass Weißblech Stahl ist. Danke für diesen Artikel zu den Eigenschaften und der Verarbeitung von Weißblech. Ich möchte eine Kunstfigur aus Weißblech bauen. Ich denke, ich ziehe Spezialisten für Stahlbau hinzu.
Meine Tochter hat in einem Unternehmen für Metallbearbeitung angefangen. Heute hat sie mir Weißblech erzählt und ich wusste gar nicht, was das ist. Interessant, dass es so alltäglich ist und zum Schutz und der Verlängerung der Haltbarkeit von Lebensmitteln eingesetzt wird.