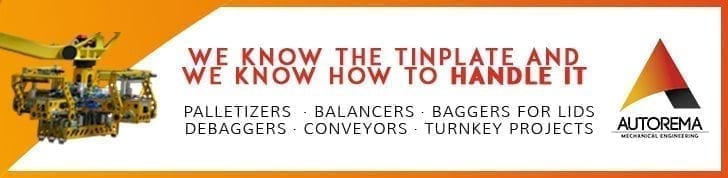
FABRICAÇÃO E CARACTERÍSTICAS DA FOLHA-DE-FLANDRES
Este documento desenvolve com algum detalhe as diferentes etapas da fabricação da folha-de-flandres, desde a obtenção do aço base e suas diferentes variedades, até as sucessivas sequências de estanhagem da folha-de-flandres.
ÍNDICE
Introdução
1.- Fabricação de açoN
1.1.- Fabricação do aço de base
1.2.- Sequência de fabrico
1.3.- Composição da base de aço
1.4.- Tipos de aço de base
2.- Estanhagem
2.1- Lata
2.2.- Revestimento de estanho eletrolítico
3.- TFS
INTRODUÇÃO À FOLHA-DE-FLANDRES
A folha-de-flandres é um material que, embora a sua invenção venha da antiguidade, atingiu realmente o seu desenvolvimento máximo durante o século passado. Foram os Estados Unidos que foram a força motriz por trás desta indústria, atingindo o seu maior volume de actividade naquele país nos anos 70. Então, a grande implantação de recipientes para bebidas, que na América do Norte utilizavam alumínio como matéria-prima, o uso de recipientes alternativos e a obsolescência da indústria siderúrgica americana, causou o declínio desse mercado.
O mesmo não aconteceu em outras partes do mundo. A Europa foi capaz de modernizar a sua indústria siderúrgica no tempo, mantendo a sua competitividade, e foi assim capaz de resistir com sucesso ao desafio do alumínio. No entanto, uma grande variedade de opções de embalagem coloca um pouco de mossa na indústria, que respondeu com sucesso com uma série de fusões, permitindo-lhe manter um excelente nível de tecnologia.
Também em outras áreas geográficas, como América do Sul, Extremo Oriente e Ásia, o mercado de folha-de-flandres e outros produtos revestidos manteve uma boa posição no mercado.
Ainda hoje é um sector importante a nível mundial, embora em contínua luta competitiva. Vale a pena, portanto, saber um pouco sobre como este material é fabricado.
1.- FABRICAÇÃO DO AÇO DE BASE
A folha-de-flandres é normalmente em peso, 99% ou mais de aço e, portanto, é essencialmente um produto de aço. O processo de fabricação começa realmente no alto-forno e na fundição de estanho, mas na prática é considerado começar da fabricação do aço. Na verdade, é neste momento que se decide a composição e o tipo de lingote de aço a ser fabricado, definindo a sua utilização futura como produto laminado. Consequentemente, as matérias-primas básicas para o fabrico de folha-de-flandres são o aço e o estanho refinado.
1.1.- Fabricação do aço de base.
Existem dois procedimentos básicos para a obtenção de aço bruto em estado líquido: a partir de (a) minério de ferro e b) sucata.
R.- Do minério de ferro (processo de fundição): o minério de ferro é uma rocha composta por óxidos de ferro e vários outros minerais (gangue). Inicialmente, os minérios e sucatas metálicas utilizados no processo estão cheios de impurezas. O ferro nunca se encontra em estado puro na natureza; na maioria das vezes sob a forma de óxidos e sulfuretos.
No processo industrial desenvolvido no alto-forno, o objetivo é obter um produto tão rico quanto possível em ferro, mas outros componentes sempre aparecerão no mesmo. Entre os materiais parasitas, muitos têm uma temperatura de combustão e evaporação inferior à do ferro, e desaparecerão por aquecimento do minério, ou terão uma densidade inferior à do ferro, e flutuarão sobre o metal em fusão. Para libertar compostos de ferro sob a forma de óxidos ferrosos (FeO), magnéticos (Fe3O) e férricos (Fe2O3) do oxigénio, é necessário tirar partido da facilidade com que o carbono reage com o oxigénio.
O carbono em sua combustão é um grande devorador de oxigênio, que o retirará do ar, mas também do óxido para formar os compostos CO e CO2 (monóxido de carbono e dióxido de carbono). Nesta operação, o excesso de carbono deixará vestígios de carbono combinado com ferro (3 a 6 %). Este material produzido no alto-forno é chamado de “derretimento”.
Para se livrar do carbono, uma operação complementar pode ser feita pela adição de oxigênio para formar CO e CO2, gases de dióxido de carbono. Este oxigênio também pode reagir com outros elementos contidos no derretimento, tais como óxido de manganês formando manganês (MnO), sílica (SiO2), alumina (Al2O3)… Todas estas operações são realizadas primeiro no alto-forno e depois, como veremos mais adiante, na operação de refinação.
Resumindo, poderíamos dizer que em um alto-forno, após uma etapa de preparação do minério na oficina de aglomeração, o ferro é extraído no alto-forno, com a ajuda de um combustível: o carbono (coque). O ferro puro ainda não é obtido, mas a fusão do ferro, uma mistura líquida de ferro (96%) mais carbono (3%) do resto do coque que não foi queimado, mais alguns resíduos (fósforo, enxofre…) da ganga. A figura 1 mostra uma seção vertical de um alto-forno.
Figura 1: Diagrama esquemático de um alto-forno
B.- A partir de sucata (“processo elétrico”): Os componentes com os quais o forno é alimentado podem ser de matérias-primas (por exemplo, peças de máquinas) devidamente selecionadas, para sucata preparada, selecionada, triturada, calibrada, com um teor mínimo de ferro de 92%. Todo o conjunto é fundido em um forno elétrico.
O ferro-gusa ou ferro do alto-forno, ou da sucata derretida num forno eléctrico, é uma liga de ferro-carbono, frágil e com um elevado teor deste último elemento. Também pode haver alto teor de enxofre e fósforo. A siderurgia é o processo de refinação, para reduzir e controlar as percentagens de elementos que não o ferro, a fim de produzir lingotes com a pureza, características e maleabilidade necessárias. Em termos gerais, estes elementos e impurezas são reduzidos por oxidação com óxido de ferro ou oxigénio, e removidos por flutuação com a adição de materiais de alto ponto de fusão (por exemplo, calcário).
Atualmente, quatro processos básicos são utilizados para obter aço, que são: Siemens-Martin ou processo de cadinho aberto, processo Bessemer ou Thomas, processo de injeção de oxigênio de sopro (processo de oxigênio de sopro) e forno elétrico. Esta última é raramente utilizada para o fabrico de folha-de-flandres. O primeiro e o segundo são talvez os procedimentos pneumáticos mais amplamente utilizados.
Processo “cadinho aberto” – O cadinho é normalmente carregado com ferro fundido do alto-forno, sucata e ferro gusa frio. As impurezas são oxidadas causando a formação de uma escória oxidante, e o combustível utilizado pode ser líquido ou gasoso. A capacidade de um forno deste tipo pode ser de até 400 toneladas e através do uso de oxigênio a granel, de economia relativa, pode ter alto desempenho, atingindo até 50 toneladas/hora. Estes fornos podem ser fixos ou basculantes.
Processo Bessemer ou Thomas – Neste sistema, as impurezas são reduzidas por injeção direta de ar ou oxigênio através do metal fundido, por meio de bicos colocados no fundo do conversor. Ver figura nº 2:
Figura nº 2: Processamento do aço no Thomas Converter
Para queimar o carbono do derretimento, sopra-se ar ou uma mistura de ar e oxigénio através do metal fundido vertido no conversor, que é uma grande retorta de aço com uma capacidade de 25 a 50 toneladas. As paredes refratárias do conversor são feitas de dolomita básica, que é resistente à cal que deve ser introduzida para remover o fósforo do derretimento. A produtividade e qualidade podem ser melhoradas controlando a composição do gás oxidante injetado, ar, ar enriquecido com oxigênio, oxigênio, mistura oxigênio/dióxido de carbono, etc. Por exemplo, a variante VLN (muito baixo nitrogênio) não só aumenta a produção como também reduz a incorporação normalmente indesejável de nitrogênio no aço.
Durante o processo podem ser distinguidas várias fases ou períodos. No primeiro período são produzidas muitas faíscas, causadas pela combustão do silício, que dura de 2 a 3 minutos. Na segunda, as chamas são geradas pela combustão do carbono, com uma persistência de 10 a 12 minutos. Na terceira é caracterizada pela expulsão de gases causados pelo subsequente sopro e combustão do fósforo, o seu intervalo é de 3 a 5 minutos.
Ao longo do processo, normalmente são adicionados diferentes elementos sólidos, tais como: cal, sucata, ferro-manganês ou ferro-gusa especular, dependendo das necessidades.
Existe um sistema chamado Duplex, que se aplica à fabricação de aço estanhado, significa a combinação do processo de ácido Bessemer com o processo básico de cadinho aberto. No conversor ocorre a purificação principal, enquanto que na segunda parte do processo ocorre a redução do fósforo.
Processo superior de injeção de oxigênio. O processo Bessemer é amplamente utilizado principalmente devido ao seu baixo custo de instalação e flexibilidade de operação, mas tem grandes limitações em termos de qualidade final, pois requer uma matéria-prima com alto teor de fósforo e restrições no uso de sucata. Estas dificuldades afetaram fortemente alguns fabricantes, o que levou ao desenvolvimento de processos superiores de injeção de oxigênio, que permitem obter aços de boa e constante qualidade, com baixo teor de nitrogênio e alto ou baixo teor de fósforo, de acordo com as necessidades. Existem três sistemas amplamente utilizados para materiais laminados e são chamados de LD, DDAC e KALDO.
O processo LD foi o primeiro baseado na disponibilidade de oxigênio em grandes quantidades. Consiste em substituir a injeção de ar do fundo de um conversor de Bessemer pela injeção de um jato de oxigênio a alta pressão do topo, o que produz uma forte agitação e, portanto, uma oxidação muito rápida das impurezas. É um processo rápido e eficiente, com investimentos iniciais não muito superiores aos do processo Bessemer, reduz os problemas de manutenção e produz um material com baixo teor de nitrogênio, sendo uma de suas limitações o uso de ferros com baixo ou médio teor de fósforo. Este sistema foi desenvolvido por duas empresas localizadas em Linz e Donawitz. Das iniciais destas cidades vem o nome do processo LD.
O DDAC é exatamente o mesmo processo acima, exceto que a cal é injetada junto com o oxigênio. É uma tecnologia de origem francesa
O processo KALDO foi desenvolvido pela primeira vez na Suécia e utiliza um cadinho ou forno rotativo e basculante, com a aplicação de um jacto de oxigénio no topo e a adição de cal por injecção ou em pedaços.
Os processos de oxigênio são versáteis e permitem o uso de quantidades razoáveis de minério e sucata, produzindo aço com baixo teor de fósforo e baixo teor de nitrogênio com boas características mecânicas.
Fundição do aço – Uma vez que o aço tenha sido obtido por um dos procedimentos descritos acima, enquanto ainda está no conversor e em estado líquido, deve ser transformado em estado sólido por fundição. Industrialmente, existem dois processos de fundição. O mais clássico em que pode ser convertido em lingotes (“fundição em lingotes”) ou seguir o procedimento de “fundição contínua”.
Fundição de moldes por ingenuidade – Este é o procedimento convencional. Através de uma concha, o aço fundido é vertido em lingotes, que uma vez arrefecidos dão origem a lingotes manejáveis, com os quais são alimentadas as seguintes operações.
Fundição contínua – Este é o processo mais moderno para o fabrico de placas. Tem as principais vantagens de produzir produtos semi-acabados de altíssima qualidade, permite menores custos de produção e aumenta a produtividade da aciaria. Na verdade, graças a este sistema, as operações são menos e mais simples do que na fundição de lingoteiras. . Está a proibir o uso de lingotes para aços destinados à laminagem. Ver figura nº 3:
Figura nº. 3: Fundição contínua
No lingotamento contínuo, o conteúdo do conversor é vertido por meio de uma concha, de forma regular e ininterrupta, em um lingote sem fundo resfriado com uma seção transversal que corresponde à da placa desejada. Em seguida, passa por uma série de rolos para aplanar e, finalmente, através de uma maçarico oxi-combustível, as chapas são cortadas no comprimento desejado. Desta forma obtemos placas (laje) de comprimento entre 5 a 20 metros, largura até um pouco mais de um metro e espessura de cerca de 20 cms.
1.2.- Seqüência de fabricação.
A Figura nº 4 apresenta uma sequência das diferentes operações ou fases na produção das chapas de aço que serão a matéria-prima básica nas fábricas de folha-de-flandres.
Figura nº 4: Fabricação de chapas de aço
Quando se utiliza o processo de lingotamento, uma vez derretido o aço em lingotes, a primeira operação realizada é a laminação do lingote para transformá-lo em uma laje. Esta operação é normalmente realizada em laminadores reversíveis, de dupla altura. O chamado tipo Universal, tem cilindros ou rolos laterais que trabalham simultaneamente as 4 faces do lingote, eliminando a operação de rotação do lingote em seu eixo durante esta etapa.
O produto final desta operação, a laje, tem uma espessura de 125 a 230 mm, a largura aproximada da folha-de-flandres que finalmente se deseja, e um comprimento que depende do tamanho do lingote original.
As placas geradas tanto por lingotamento contínuo como por laminação de lingote são preparadas para tratamento em laminação a quente.
A laminação a quente é a etapa seguinte, embora normalmente exista uma etapa intermédia, que consiste no arrefecimento e armazenamento das placas, um processo de selecção, uma preparação da superfície (escarificação) e um aquecimento da placa a uma temperatura adequada para a laminação. A eliminação desta etapa intermediária requer uma programação muito precisa e uma capacidade tecnológica muito alta, o que garante a ausência de defeitos nas placas ou lajes. A figura nº 5 mostra as diferentes fases da laminação a quente.
Figura nº 5: Processo de laminação a quente
A preparação da superfície é realizada na “máquina descalcificadora”, na qual a placa é submetida a um desprendimento de óxidos e impurezas de ferro, que é obtido por meio de uma pressão de rolagem fraca, desprendendo-os pela ação da água a alta pressão. A placa é aquecida a uma temperatura de 880º C. É necessário remover esta camada de óxidos porque danifica o laminado, pois causa desgaste rápido dos cilindros, estrias no metal, incrustações de óxidos e outros defeitos de fabricação (quebras, escorregamentos, dobras…).
O laminador a quente reduz a chapa a uma faixa contínua de cerca de 2 mm de espessura. Normalmente consiste em duas secções, uma secção de desbaste e outra de acabamento. Pode ser de tipo contínuo ou reversível, dependendo da capacidade da instalação, etc.
O trem de rugosidade consiste geralmente em 4 a 6 caixas que reduzem a espessura inicial da placa em 25 a 50% por caixa. O comboio de acabamento tem 4 a 7 caixas, reduzindo novamente a espessura em 25 a 30 % por caixa, excepto a última que apenas reduz em 10 %. A velocidade máxima desta operação pode estar nos 100km/h. Na saída, o material está a 850º C. Procede-se ao arrefecimento por cortina de água até 590º, formando bobinas com o mesmo.
A bobina produzida deve ser decapada e lubrificada antes da laminação a frio. Esta operação é geralmente realizada numa sucessão de tanques contendo ácido sulfúrico diluído a quente (perto de 100º C), lavados, secos e lubrificados com óleo de palma ou outro lubrificante adequado para laminação a frio. A linha de decapagem é normalmente equipada com um cortador circular, que corta as bordas, garantindo assim que são adequadas para a redução ou laminação a frio, fixando também a largura máxima da folha-de-flandres a ser obtida e também a que dará os melhores resultados económicos. Ver figura nº 6.
Figura nº 6: Laminagem a frio, recozimento e laminagem skin-pass de aço de base
A próxima operação é a laminação a frio, que pode ser feita em contínuo (tandems) ou em moinhos reversíveis. Os lubrificantes e refrigerantes são utilizados durante esta operação e a espessura resultante é muito próxima do acabamento desejado. A redução é portanto de 1,8 ou 2 mms para uma medida entre 0,15 a 0,3 mm aproximadamente de acordo com o tamanho final da folha-de-flandres a ser produzida.
A bobina obtida é feita de um material muito duro e sujeito a fortes tensões, e necessita de um tratamento adequado para lhe dar a maquinabilidade necessária, provocando uma recristalização do aço. Este tratamento chama-se recozimento e envolve o aquecimento do metal numa atmosfera redutora para evitar qualquer oxidação (mistura de nitrogénio e hidrogénio) e pode ser feito continuamente (recozimento contínuo) ou em fornos de recozimento por lotes (batch annealing).
Recozimento contínuo: A tira circula através de um forno a uma temperatura de 630º C, permanecendo cada ponto do material no forno por um mínimo de 1,5 minutos. O recozimento contínuo tem uma série de vantagens e desvantagens, tais como:
Vantagens:
– Redução de materiais “em processo” de produção.
– Redução dos prazos de fabrico.
– Melhoria da qualidade dos produtos fabricados:
o Aquecimento constante e contínuo ao longo de todo o comprimento da bobina, o que resulta em propriedades mecânicas mais homogêneas.
o Ciclo rápido, obtenção de grãos eqüiaxiais finos, portanto um metal isotrópico e propriedades mecânicas superiores, como a melhoria do limite elástico.
o Melhor resistência à corrosão. O ciclo rápido não permite que elementos como o carbono, manganês, fósforo… se movam para a superfície do material como acontece na base ou no recozimento do sino.
o Permite o uso de uma composição de aço tipo MR, menos carregada com elementos de endurecimento: carbono, manganese-…. (recozimento contínuo = 0,08 % carbono, recozimento de base = 0,10/0,13 % carbono) que favorece operações como a soldadura, especialidades…
Desvantagens:
– Fabricação:
o Programação difícil das encomendas, já que a variação máxima de largura entre bobinas consecutivas é da ordem de 50 mm, e em espessura da ordem de 10 %.
o Condução delicada da linha. Risco de quebra da correia no forno. É uma parada importante. O limite elástico da tira na temperatura do forno de recozimento é baixo (aprox. 30 N/mm2).
o Impossibilidade de parar a linha.
– Use:
o Cristalografia fina que gera um metal menos dúctil, com fraca anisotropia, o que prejudica o desenho.
o Risco de presença de linhas Lüder.
Recozimento em sino: várias bobinas empilhadas são cobertas com um sino numa atmosfera redutora a uma temperatura de 680º C durante pelo menos 85 horas, divididas em 32 horas de aquecimento, 34 horas de arrefecimento sob um sino até 170º, e 19 horas de arrefecimento acelerado ao ar livre. Ver figura nº 7
Figura nº 7: Diagrama do processo de recozimento da campânula.
Em ambos os casos é essencial eliminar previamente os resíduos dos agentes lubrificantes e refrigerantes utilizados anteriormente, sendo o método utilizado para tal, consistente com o tipo de recozimento a ser feito, normalmente por meios electroquímicos, como por exemplo um banho de desengordurante aquecido a 95 ºC ou mecânico, com escovagem em ambos os lados.
A seguir vem a operação de têmpera, tratamento de superfície ou acabamento (têmpera rolante ou skin-pass). É feita através de uma redução ou laminação, sem lubrificante e muito leve, que normalmente não excede 2% em espessura. Para este fim, é utilizado um laminador composto por duas caixas. A tira, ao passar entre os cilindros sob o efeito da pressão e tração estabelecidas, sofre uma modificação superficial da estrutura, conseguindo um aumento da dureza da camada superficial, mas preservando a maciez interna.
Em resumo, esta operação confere à tira a dureza desejada, um bom achatamento e um bom acabamento superficial do material, dependendo da rugosidade dos rolos utilizados nas caixas do laminador. Combinando o acabamento superficial dos cilindros das caixas desta laminação, e a refundição final do estanho após a operação de estanhagem, conseguem-se diferentes acabamentos superficiais da folha-de-flandres. Os principais tipos de acabamentos são:
Acabamento brilhante: Para conseguir este acabamento, é essencial obter um polimento espelhado nos cilindros. Além disso, é necessário aplicar a refusão de estanhagem. Este tipo de acabamento é, juntamente com a pedra, o mais solicitado.
Acabamento em pedra: Os cilindros são submetidos a duas passagens de moagem com uma mó de grão especial, o que confere ao produto um aspecto estriado. Como no caso anterior, o revestimento de estanho é refundido, o que também garante o brilho.
Acabamento mate: Tem uma superfície pouco reflectora. Para isso, os cilindros são jateados e a operação de refundição após o estanhamento é omitida.
No caso da folha-de-flandres duplamente reduzida, a última redução de tamanho é feita através da substituição da operação de têmpera por uma redução adicional de tamanho ou laminação de aproximadamente 33%, com o consequente alongamento do material por uma percentagem semelhante, desta vez utilizando lubrificantes de superfície. Isto dá à folha-de-flandres altas propriedades mecânicas com uma pequena espessura.
É prática comum preparar as bobinas antes da operação de estanhagem. Consiste principalmente em cortar as arestas e eliminar as seções de baixa qualidade ou de calibre fora de especificação, formando bobinas de tamanho ideal para a linha de estanhagem.
Na estanhagem electrolítica, o material preparado passa continuamente pelas operações de limpeza electrolítica, decapagem electrolítica, electrodeposição de estanho, refundição de estanho (flow-melting), tratamento de passivação e lubrificação. Após esta série de operações, o produto pode ser cortado em folhas no tamanho encomendado (comprimento, pois a largura foi dada na preparação das bobinas), inspecionado, separado e embalado; ou pode ser enrolado para envio ao cliente ou para corte, etc., em uma linha de corte separada. É normal realizar na mesma linha, a seleção do material, antes de embalar. Voltaremos a estes pontos com mais detalhes mais tarde.
1.3.- Composição da base de aço.
Para a folha-de-flandres, o aço de base é essencialmente um aço macio de baixo teor de carbono, com uma composição genérica do seguinte tipo:
– Carbono 0,04 – 0,15 %.
– Silício 0,08 % máximo
– Enxofre 0,015 – 0,05 %.
– Fósforo 0,01 – 0,14 %.
– Cobre 0,02 – 0,20 %.
– Manganês 0,20 – 0,70 %.
– Nitrogênio 0,001 – 0,025 %.
Devido ao uso de sucata na produção de aço, outros elementos como o níquel, cromo e estanho podem estar presentes, mas nenhum outro elemento é adicionado intencionalmente. As únicas exceções são fósforo e nitrogênio, que podem fornecer propriedades especiais. O uso do cobre para aumentar a resistência à corrosão, e de alguns carbonetos para controlar o envelhecimento, caiu em desuso.
A influência de alguns elementos na base de aço da folha-de-flandres é dada em linhas gerais nos parágrafos seguintes.
– Carbono: O carbono aumenta a resistência ao escoamento, a resistência à tração e a dureza, diminui o alongamento e a ductilidade. Dentro dos limites habituais da folha-de-flandres, as variações no conteúdo deste elemento são de pouca importância, uma vez que outros elementos têm uma influência muito maior.
– Silício: Existe em folha-de-flandres como elemento residual, muito raramente é adicionado como um agente desoxidante. Endurece ligeiramente e, em alguns casos, afecta negativamente a resistência à corrosão.
– Enxofre: Neste tipo de aço, os efeitos do enxofre são neutralizados pelo manganês, que está sempre presente. No entanto, devido às suas consequências na ductilidade, qualidade da superfície e resistência à corrosão, são feitos todos os esforços, dentro dos limites económicos, para a reduzir ao mínimo possível.
– Fósforo: É um elemento que influencia fortemente a dureza e a resistência à corrosão. Quando existe a possibilidade de corrosão ácida, esta deve ser mantida dentro de certos limites, e o conteúdo é aumentado quando é necessária uma maior resistência do aço e não existe o perigo de corrosão.
– Cobre: Embora aumente a resistência, não o faz de forma eficaz dentro dos limites habituais. A ultrapassagem destes limites aumenta a resistência à corrosão atmosférica, mas pode reduzir a resistência à corrosão interna, pelo que, para a maioria dos tipos de folha-de-flandres, é especificado um teor máximo de cobre.
– Manganês; É utilizado na fabricação de aço para folha-de-flandres, principalmente para reagir com outros elementos, principalmente enxofre, tornando-os inoperantes.
– Nitrogênio: Nos aços Bessemer, é um elemento constituinte normal em percentuais superiores a 0,01% e sempre foi considerado uma desvantagem. Posteriormente verificou-se que a sua adição intencional aumenta consideravelmente a resistência do aço sem modificar sensivelmente a resistência à corrosão, embora possa afectar o envelhecimento. O desenvolvimento dos processos de oxigénio (LD, etc.) permitiu controlar com precisão o conteúdo deste elemento, dando uma qualidade uniforme e contínua.
– Níquel: Em níveis permitidos, não afecta as propriedades físicas ou mecânicas da folha-de-flandres, mas afecta as propriedades químicas, especialmente a corrosão em certos tipos de embalagens. O mesmo é verdade para o crómio.
– Estanho: Este elemento tem uma elevada solubilidade em ferro ou aço, sendo necessárias percentagens superiores a 10% para que uma segunda fase se forme. Em níveis normais não tem efeito sobre a estrutura metalográfica. A sua presença aumenta progressivamente o limite elástico e o limite de ruptura por tracção, com uma redução do módulo de elasticidade. É importante notar que pequenas quantidades de estanho, em aços que contêm cobre, podem causar sérias dificuldades no trabalho a quente do aço.
Na produção de aço, por vezes são utilizadas regras práticas para calcular os efeitos da liga e dos elementos residuais nas propriedades mecânicas do aço folha-de-flandres. Um dos mais comuns é o índice de Strohmayer, que é calculado multiplicando o conteúdo de nitrogênio por 5, adicionando o fósforo e multiplicando a soma por 1000.
1.4.- Tipos de aço de base
Tradicionalmente existem três tipos básicos de aço folha-de-flandres, embora com as tecnologias actuais seja por vezes difícil permanecer dentro dos tipos clássicos. Estes são:
Tipo L: É um aço laminado a frio, proveniente de fornos de cadinho aberto (Siemmens Martin). Tem um baixo conteúdo em metalóides e elementos residuais, especialmente limitados em fósforo, com a seguinte composição:
Carbono 0,05 – 0,13 %.
Manganês 0,30 – 0,60 %.
Enxofre 0,04 máximo.
Fósforo 0,015 no máximo.
Silício 0,010 no máximo.
Cobre 0,06 no máximo.
Níquel 0,04 no máximo.
Crómio 0,06 máximo.
Molibdénio 0,05 máximo.
Arsénico 0.02 máx.
Nitrogênio 0,02 máximo.
É usado quando é necessária uma alta resistência a produtos muito corrosivos.
Tipo MR: É o mais utilizado. É da mesma origem que o anterior, laminado a frio e utilizado em produtos moderadamente corrosivos. A sua análise é:
Carbono 0,05 – 0,15 %.
Manganês 0,30 – 0,60 %.
Enxofre 0,04 máximo.
Fósforo 0.020max.
Silício 0,010 no máximo.
Cobre 0,20 no máximo.
Tipo MC: É um aço fabricado no conversor Bessemer ou forno Siemmens Martin, utilizado quando a resistência e o conteúdo do recipiente é de baixa corrosividade. A análise da sua amostra é a seguinte:
Carbono 0,05 – 0,15 %.
Manganês 0,25 – 0,60%.
Enxofre 0,04 máximo.
Fósforo 0,03 – 0,15 %.
Silício 0,010 no máximo.
Cobre 0,20 no máximo.
Existem também alguns aços especiais como o tipo D, de alumínio temperado e revenido, utilizados em casos específicos de trefilação profunda.
Geralmente os fabricantes na Europa têm sido forçados a tentar eliminar as produções especializadas em folha-de-flandres e assim encontrar procedimentos económicos e competitivos, por isso tentam simplificar o problema.
Também importante do ponto de vista da resistência à corrosão é a superfície do aço, que depende em parte do tipo de atmosfera utilizada durante o recozimento. Uma atmosfera contendo nitrogénio, hidrogénio, dióxido de carbono e vapor de água produz uma folha-de-flandres menos resistente do que uma folha-de-flandres seca contendo 4 a 8% de hidrogénio. Também os íons de estanho dissolvidos têm em geral um efeito inibidor sobre a corrosão da folha-de-flandres por alguns produtos.
2.- TINTAGEM
2.1.- Estanho
Quando este material se destina ao fabrico de folha-de-flandres, é lógico pensar que estará em contacto prolongado com os alimentos e deve, portanto, satisfazer certos requisitos em termos de impurezas. A American Society for Testing and Materials (ASTM) classifica em cinco grupos, cada um com conteúdo mínimo de estanho da seguinte forma: grau AA = 99,98 % de estanho, A = 99,80 %, B = 99,7 %, C-1 = 99,0 % e C-2 = 99,0 %. O mínimo especificado para o fabrico de folha-de-flandres é a classe A. A sua análise é:
Estanho (mínimo) 99,80 %.
Antimónio 0,04 %.
Arsénico 0,04 %.
Bismuto 0,015 % Bismuto 0,015 % Bismuto 0,015 % Bismuto 0,015
Cobre 0,03 %.
Ferro 0,015 % Ferro 0,015 % Ferro 0,015 % Ferro 0,015 % Ferro 0,015 % Ferro
Chumbo 0,05 %.
Níquel e Cobalto 0,015 %.
Prata 0,01 % Prata 0,01 % Prata 0,01 % Prata 0,01 % Prata 0,01 % Prata 0,01 % Prata 0,01
Enxofre 0,003 % Enxofre 0,003 % Enxofre 0,003 % Enxofre 0,003
Zinco 0,001 % Zinco 0,001 % Zinco 0,001 % Zinco 0,001 % Zinco 0,001 % Zinco
Cádmio 0,001 %.
Alumínio 0,001 %.
- 2.- Estanhagem eletrolítica
O desenvolvimento deste processo de estanhagem foi um dos passos mais importantes na indústria do estanhamento. A electrodeposição do estanho sobre uma faixa estreita contínua (faixa), começou na Alemanha em 1930, mas foi durante a 2ª Guerra Mundial que a técnica foi desenvolvida intensivamente, principalmente nos EUA, devido à escassez de estanho.
Há uma série de razões técnicas e económicas que fizeram com que a folha-de-flandres electrolítica tirasse o mercado da folha-de-flandres de coque ou da folha-de-flandres quente, que era a forma tradicional de a obter. Um dos mais importantes é o controle preciso da quantidade de estanho depositado e a uniformidade na espessura. Outra é a disponibilidade da folha-de-flandres electrolítica diferencial, que consiste em aplicar espessuras diferentes de revestimento de estanho em cada lado da folha.
Como já indicamos na operação de têmpera do aço base, a folha-de-flandres eletrolítica pode ser produzida em vários acabamentos, embora três sejam os mais comuns. “Brilhante”, que é o mais comum, “mate” que consiste em estanhar aço de base com uma superfície rugosa e depois não refundir o estanho e finalmente “pedra” que é o mesmo acabamento que acima mas refundindo o estanho, o que dá um acabamento brilhante mas não reflector.
Os métodos de fabricação são basicamente dois, ácido e alcalino ou processo básico, mas este último tem duas variantes de amplo uso, linhas halógenas horizontais e linhas alcalinas ou verticais. Há um quarto procedimento, que usa fluoboratos como eletrólitos, mas é muito pouco usado.
As linhas que utilizam o processo ácido são as que produzem a maior percentagem de folha-de-flandres electrolítica. Eles são freqüentemente chamados de Ferrostan, pois este foi o nome registrado pela U.S. Steel para sua folha-de-flandres, com muitos licenciados subsequentes de sua tecnologia ao redor do mundo.
Os electrólitos são a parte mais delicada de cada processo. Por exemplo, nas linhas ácidas, é uma solução de sais estanosos em ácido, mas o bom desempenho como electrólito depende dos vários aditivos utilizados, que têm três objectivos principais, evitar a oxidação, favorecer a formação de depósitos compactos e não combustíveis, e melhorar a molhabilidade.
Algumas vantagens clássicas do uso do eletrólito alcalino são ter um eletrólito mais simples, mais fácil de manusear e não corrosivo em relação ao aço, o que reduz o custo inicial do equipamento. A seção preparatória também é mais simples.
As linhas ácidas têm a vantagem de utilizar menos corrente para o revestimento de estanho do que as linhas alcalinas, é necessária menos área de superfície do ânodo e a eficiência elétrica é maior na eletrodeposição. No entanto, as linhas alcalinas produzem uma folha-de-flandres com melhores características de resistência à corrosão.
Em linhas gerais, os três tipos de linhas são constituídos pelas secções seguintes:
Desenrolar
Preparação
Estanhagem
Acabamento
Corte – enrolamento – embalagem
A seção de entrada ou desenrolamento tem o equipamento necessário para o manuseio das bobinas de chapa preta, e para a alimentação contínua da linha, cortando o início e o final de cada bobina e a solda elétrica do final de uma com o início da seguinte. Inclui rolos de guia e de alimentação, rolos de tensão, etc.
Entre a seção de desenrolamento e preparação, há um dispositivo para armazenar a tira de chapa preta, destinado a acumular uma certa quantidade de tira, que alimenta a linha enquanto a bobina está sendo trocada e emendada na seção de desenrolamento anterior. Existem vários tipos, predominantemente bem e “acordeão”.
A seção de preparação tem dois objetivos principais, limpeza (desengorduramento) e decapagem. O primeiro é a remoção de todos os elementos residuais na superfície da correia, provenientes de lubrificantes, agentes refrigerantes, etc., enquanto o segundo visa remover o óxido de ferro aderido a ambos os lados da correia.
O tratamento é realizado numa sucessão de banhos químicos ou electro-químicos, com jactos de água e/ou lavagens a vapor alternados. O layout e o tipo dependem da linha. Por exemplo, o desengorduramento é normalmente feito numa solução detergente ou alcalina e em linhas deste tipo é eliminado ou reduzido porque o desengorduramento é feito automaticamente na secção de estanhagem.
A seção de estanhagem difere completamente em cada processo, sendo a do processo de halogênio a que ocupa a maior superfície, já que a tira se move plana, normalmente em 3 níveis, enquanto nos outros dois sistemas segue uma forma sinusoidal ou serpentina.
Figura nº 9: Linha de estanhagem, tanque electrolítico e ânodos
Antes do estanhamento, as marcas correspondentes à folha-de-flandres diferencial são feitas na tira de chapa preta, quando é este tipo que é fabricado, portanto estas marcas vão para o aço de base. Alguns fabricantes podem marcar o aço de base para que, em caso de dificuldades posteriores com a folha-de-flandres, o fabricante possa ser identificado. Estas marcas não são visíveis na folha propriamente dita, devem ser encontradas no laboratório.
A seção de acabamento inclui diferentes etapas, sendo as principais: refusão, passivação e lubrificação.
A finalidade da refundição é dar um acabamento brilhante à folha-de-flandres, uma vez que a simples electrodeposição da folha-de-flandres produz uma superfície de micro-raspa com um aspecto mate. Contudo, este passo é de fundamental importância para a folha-de-flandres destinada a estar em contacto com elementos corrosivos. Durante a refundição, forma-se uma camada de liga de ferro-estanho e, devido à rapidez com que é produzida, a espessura é muito fina. Segue-se que a folha-de-flandres baça, que não foi submetida à refundição, não deve ser utilizada para aqueles fins que requerem a presença de uma camada de liga de ferro-estanho.
A passivação é uma característica da folha-de-flandres eletrolítica. Neste caso, especialmente em revestimentos baixos, é conveniente fornecer-lhe uma camada protectora que evite a oxidação, não só durante a fabricação, mas também em operações posteriores, como o envernizamento. Também é necessário dar uma superfície quimicamente mais adequada para litografia e envernizamento, e de uma certa dureza protectora. A passivação destina-se a cobrir este aspecto e consiste basicamente na formação de uma camada de óxido crómico. Os métodos utilizados são vários métodos químicos ou electro-químicos, cada um concebido para obter características especiais. São geralmente conhecidos pela sigla USS e um número de três dígitos, o primeiro dígito indica o tipo de solução (1 = ácido crómico, 2 = fosfato de cromo, 3 = dicromato de sódio, 4 = carbonato de sódio), o segundo dígito indica a polaridade da folha-de-flandres na solução (0 = não-eletrolítico, 1 = catódico, 2 = catódico/anódico) e o terceiro dígito refere-se aproximadamente ao nível de corrente utilizado.
Existem três tipos básicos de passivação, que são:
– Passivação 300: É obtida por procedimento químico, por imersão em solução de dicromato de sódio, gerando uma camada de óxido de crómio. Dá bons resultados do ponto de vista da aderência do verniz. Oferece uma fraca protecção contra a sulfidação. Esta passivação é, no entanto, instável. A sua eficácia diminui com o tempo.
– Passivação 311Galvanoplastia: Obtida por processo eletroquímico por deposição eletrolítica em um banho de dicromato de sódio de uma camada de cromo e óxido de cromo. É a passivação mais comumente usada. Tem rendimentos convenientes do ponto de vista da adesão do verniz, embora inferior à passivação 300. É muito mais estável ao longo do tempo do que os 300. Pode, portanto, ser considerado um compromisso entre a estabilidade ao longo do tempo e a qualidade de adesão dos sistemas litográficos.
– Passivação 312: É obtida pelo mesmo sistema que o 311. Na verdade, é uma passivação 311 reforçada. É utilizado principalmente para folhas-de-flandres que devem resistir aos produtos sulfurados, como carnes, sopas, produtos para cães e gatos… Sua adesão a tintas e vernizes é inferior a 311.
Os diferentes tratamentos de passivação não só afectam a aderência de vernizes, soldaduras, etc., mas também produzem várias formas de ataque ou coloração, uma vez que a folha-de-flandres é sujeita ao contacto com produtos corrosivos ou compostos de enxofre. Mesmo de um ponto de vista estético ou de apresentação, este detalhe é importante, por exemplo, com leite condensado.
Finalmente, a seção de acabamento realiza a operação de lubrificação. O objectivo deste lubrificante não é tanto proteger a folha-de-flandres em si, mas a passivação e não contrariar as suas propriedades é muito leve, pelo que o método de aplicação mais utilizado é por electrodeposição, embora possa ser feito por pulverização ou imersão. São normalmente utilizados três tipos de óleo: óleo de algodão, sebacate dioctílico e sebacate dibutílico, sendo este último o mais comum. A quantidade normal de lubrificante é da ordem de 0,005 grs/m2. O lubrificante é normalmente seco por meio de vapor e bobinas de ar quente.
A última parte da linha depende da formação do produto final e da produtividade a ser obtida, e não do tipo de linha (ácido, …). Se a produção for exclusivamente em bobinas, não haverá corte, mas haverá um dispositivo de armazenamento para a banda, para permitir a troca de bobinas. Se a produção é exclusivamente em folhas cortadas, o dispositivo de armazenamento não é necessário. Na operação de corte é feita a seleção dos defeitos superficiais, este controle não é muito eficiente devido à velocidade da linha, portanto o produto obtido é classificado como “unassorted” (não selecionado). Se você quiser separar “primeiros” de “segundos”, você precisa usar os serviços auxiliares de uma linha de seleção. É nesta secção que se separam as folhas de furos de pinos e as folhas de furos de pinos. Quando as bobinas são entregues, é normal não fazer essa separação, o que diminui o rendimento, e cabe ao cliente fazer essa operação ao cortar. A qualidade “não seleccionada” é definida como um produto normal de uma linha de estanhagem electrolítica.
Uma linha de estanhagem eletrolítica tem um equipamento auxiliar muito complexo, mais complexo de fato que a própria linha, algo semelhante a icebergs acontece, você não pode ver a parte afundada. Equipamentos elétricos e eletrônicos, controles, bombas, tanques de eletrólitos, equipamentos de purificação, sistemas de água e vapor, ar, etc., são de grande importância e normalmente são instalados no subsolo. A energia elétrica instalada também é muito forte.
A velocidade da tira durante o estanhamento é função da corrente elétrica disponível para a eletrólise, do estado do eletrólito, do tamanho e da espessura do material, da deposição de estanho desejada e outros fatores.
3.- TFS
Como consequência do aumento do preço do estanho e do risco de ver as fontes de abastecimento de estanho em perigo, durante o último terço do século passado foi desenvolvido um produto de substituição da folha-de-flandres, a TFS ou folha cromada. Este material logo despertou um interesse que tem aumentado com o tempo. A sua vantagem reside no facto de ser uma opção perfeitamente válida para a fabricação de tampas, fundos, acessórios e recipientes de fundo, e ligeiramente mais barata do que a folha-de-flandres.
O TFS é feito de um suporte idêntico ao da folha-de-flandres: o aço. Embora a proteção seja assegurada, não por uma camada leve de estanho aplicada por deposição eletrolítica e por uma película de passivação, mas por um revestimento misto de cromo e óxido de cromo.
Na indústria do aço é comum produzir TFS numa instalação mista, que pode produzir folha-de-flandres ou chapa cromada com uma série de alterações pouco complexas, que são realizadas num tempo moderado. A aplicação de cromo também é feita por sistema eletrolítico. A figura 10 mostra a parte especial de uma linha para a produção de chapa cromada.
Não entramos em detalhes no processo de obtenção, pois como já indicamos o aço base é o mesmo que para a folha-de-flandres, e a linha de revestimento segue uma sequência análoga à da folha-de-flandres.
Finalmente, vale a pena mencionar a importante participação das grandes empresas de embalagem nos desenvolvimentos na fabricação de aço para folha-de-flandres, na fabricação da própria folha-de-flandres, em outros materiais alternativos como a TFS, e, claro, na sua utilização.
Boa tarde, estou precisando na medida 0,50 ou maior.
O flandre é resistente a água do mar ???