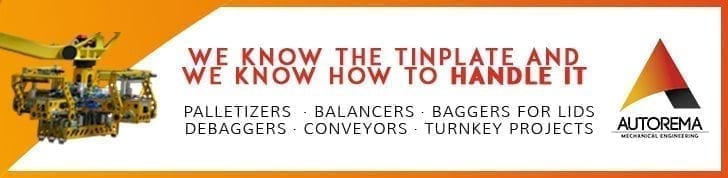
ブリキの製造と特性
本書では、ブリキの製造工程について、母材となる鋼材の入手からブリキを焼くまでの一連の工程を詳しく解説しています。
INDEX
はじめに
1.スチールの製造N
1.1.基本的なスチールの製造
1.2.製造順序
1.3.- ベーススチールの組成
1.4.-基本的なスチールの種類
2.錫メッキ
2.1-錫
2.2.-電解スズめっき
3.- TFS
ブリキの紹介
ブリキという素材は、その発明は古代に遡るが、その発展のピークは前世紀にあった。 この産業を牽引してきたのは米国であり、1970年代にその活動量は最高潮に達した。 その後、北米ではアルミニウムを原材料とする飲料用パッケージの大規模展開、代替パッケージの使用、アメリカの鉄鋼業の陳腐化などにより、この市場は減少していきました。
他の地域ではそうではありませんでした。ヨーロッパは、競争力を維持しながら鉄鋼業の近代化を間に合わせることができたため、アルミニウムの挑戦にも見事に耐えることができたのです。 しかし、パッケージの選択肢が増えたことで、業界は合併を繰り返し、優れた技術力を維持することができたのです。
また、南米、極東、アジアなどのその他の地域でも、ブリキおよびその他の塗装製品の市場は良好な地位を維持しました。
今日では、継続的な競争にさらされているとはいえ、世界的に重要なセクターであることに変わりはありません。 そのため、この素材がどのように製造されているかを少し知っておく必要があります。
1.基本となる鋼材の製造
ブリキは通常、重量比で99%以上が鋼であり、本質的には鉄鋼製品である。 実際の製造工程は高炉や錫の製錬所から始まるが、実際には製鉄から始まると考えられている。 実はこの時点で、作る鋼塊の成分や種類が決まり、将来の圧延品としての用途が決まってしまうのです。 そのため、ブリキ製造の基本的な原材料は、鋼と精製された錫である。
1.1.- ベーススチールの製造
粗鋼を液体の状態で得るには、2つの基本的なプロセスがあります。 (a) 鉄鉱石と (b) スクラップメタル
A.-鉄鉱石から (製錬工程):鉄鉱石は、鉄の酸化物と他のさまざまな鉱物(ガングー)からなる岩石です。このプロセスで使用される鉱石やスクラップは、最初は不純物が多く含まれています。鉄は自然界では純粋な状態ではなく、多くは酸化物や硫化物の形で存在する。
高炉で開発された工業プロセスでは、できるだけ鉄分の多い製品を得ることを目的としていますが、その中には必ず他の成分が含まれています。 寄生物質の中には、鉄よりも燃焼・蒸発温度が低く、鉱石を加熱すると消えてしまうものや、鉄よりも密度が低く、溶湯に浮いてしまうものが多くあります。 第一鉄(FeO)、磁性(Fe3O)、第二鉄(Fe2O3)などの鉄化合物を酸素から遊離させるためには、炭素が酸素と反応しやすいことを利用する必要がある。
燃焼中の炭素は、空気中の酸素だけでなく、酸化物からも酸素を吸収して、COとCO2(一酸化炭素と二酸化炭素)という化合物を形成する。 この操作では、余分なカーボンが鉄と結合したカーボンの痕跡(3~6%)を残します。 高炉で作られたこの素材を「メルト」と呼ぶ。
炭素を取り除くためには、酸素を加えてCOとCO2という炭酸ガスを作るという補完的な操作を行うことができる。 この酸素は、融液に含まれる他の元素、例えばマンガンと反応して酸化マンガン(MnO)、シリカ(SiO2)、アルミナ(Al2O3)…を形成する。 これらの作業は、まず高炉で行われ、後述するように精錬作業でも行われます。
要約すると、高炉では、集塊作業場で鉱石を準備する段階を経て、燃料である炭素(コークス)を使って鉄を抽出するということです。 純鉄はまだ得られていないが、鋳鉄とは、鉄(96%)と、燃焼しなかったコークスの残りの炭素(3%)と、ガングの残留物(リン、硫黄など)が混ざった液体のことである。 図1は、高炉の垂直断面図です。
図1:高炉の模式図
B.- スクラップから (炉に投入される部品は、適切に選別された原材料(機械部品など)から、準備、選別、粉砕、格付けされた鉄分92%以上のスクラップまで様々です。 アセンブリ全体を電気炉で溶かします。
銑鉄(高炉で作られた鉄、電気炉で溶かされたスクラップの鉄)は、炭素を多く含むもろい鉄と炭素の合金である。 また、硫黄やリンの含有量が多い場合もあります。製鉄とは、鉄以外の元素の割合を減らしてコントロールし、必要な純度、特性、可鍛性を備えたインゴットを製造するための精錬のことです。 一般的には、これらの元素や不純物を、酸化鉄や酸素による酸化で還元し、高融点物質(石灰石など)を加えて浮遊させることで除去します。
現在、鋼の製造には、シーメンス・マルティン法(オープンクルーシブル法)、ベッセマー法(トーマス法)、トップブロー法(酸素法)、電気炉の4つの基本プロセスが用いられている。後者はブリキの製造にはほとんど使われません。 1つ目と2つ目は、おそらく最も広く使用されている空気圧の手順と合わせて…。
オープンクルーシブル」プロセス –るつぼには通常、高炉からの溶融鉄、スクラップ、冷えた銑鉄が投入される。 不純物が酸化されて酸化スラグが形成され、使用される燃料は液体でも気体でもよい。 このようなキルンの容量は最大400トンで、比較的安価なバルク酸素を使用することで、最大50トン/時の高い処理能力を持つことができます。 このオーブンは、固定式と傾斜式があります。
ベッセマー法またはトーマス法:このシステムでは、転炉の底部に設置されたノズルを使って、空気または酸素を溶融金属に直接注入することで不純物を減らす。図No.2参照。
図2:トーマスコンバーターでの鋼材加工
溶融物中の炭素を燃焼させるために、空気または空気と酸素の混合物を、転炉に注がれた溶融物の中に吹き込む。 転炉の耐火壁には塩基性ドロマイトが使用されており、溶融物からリンを除去するために導入しなければならない石灰の影響を受けない。 注入する酸化ガス、空気、酸素富化空気、酸素、酸素/二酸化炭素混合ガスなどの組成を制御することで、生産性や品質を向上させることができます。 例えば、VLN(very low nitrogen)バリアントは、生産性を向上させるだけでなく、通常は望ましくない鋼への窒素の混入を低減させます。
このプロセスには、いくつかの段階や期間があります。 第1期では、シリコンの燃焼により多くの火花が発生し、それが2~3分続きます。 2つ目は、炭素の燃焼によって炎が発生し、その持続時間は10~12分。 3つ目の特徴は、リンのアフターブローと燃焼によるガスの排出で、その間隔は3~5分です。
このプロセスでは、必要に応じて、石灰、スクラップ、フェロマンガン、銑鉄など、さまざまな固体元素を添加します。
ブリキ鋼の製造には、ベッセマー酸プロセスと基本的なオープン・クルーシブル・プロセスを組み合わせた、いわゆるデュプレックス・システムがある。 コンバーターでは主に浄化が行われ、第2部ではリンの還元が行われます。
優れた酸素注入プロセス。 ベッセマー法は、導入コストの低さや操作の柔軟性などから広く利用されているが、リン含有量の高い原料が必要であることや、スクラップの使用に制限があるなど、最終的な品質の面で大きな制約がある。 そのため、優れた酸素注入プロセスが開発され、必要に応じて低窒素、高リン、低リンを含む良質で安定した品質の鋼材を得ることができるようになった。 ラミネート材には、LD、DDAC、KALDOと呼ばれる3つのシステムが広く使われています。
LDプロセスは、大量の酸素が得られることを前提とした最初のプロセスである。 これは、ベッセマー式転炉の底部からの空気の噴射を、上部からの高圧の酸素の噴射に置き換えることで、強い撹拌を行い、その結果、不純物を非常に迅速に酸化させるというものです。 速くて効率的なプロセスで、初期投資はベッセマー法に比べてそれほど高くなく、メンテナンスの問題も少なく、窒素含有量の少ない材料が得られますが、リン含有量の低い、あるいは中程度の鉄を使用しなければならないという制限があります。 このシステムは、リンツとドナウィッツにある2つの会社が開発しました。 これらの都市の頭文字をとって、LDプロセスの名前が生まれました。
DDACは、酸素と一緒に石灰を注入する以外は、上記と全く同じプロセスです。 フランス発祥の技術である
KALDOプロセスはスウェーデンで最初に開発されたもので、回転しながら傾くるつぼやキルンを使い、上部で酸素を吹き込み、石灰を注入または塊で加える。
酸素プロセスは汎用性が高く、適度な量の鉱石やスクラップを使用することができ、機械的特性の良い低リン・低窒素鋼を製造することができます。
鋼の鋳造 – 上述の手順のいずれかによって鋼が得られたら、それがまだ転炉の中で液体の状態にあるうちに、それを鋳造して固体の状態に変えなければならない。 工業用鋳造には2つのプロセスがある。 より古典的なものとしては、インゴットに変換する方法(「インゴット鋳造」)と、「連続鋳造」の手順を踏む方法があります。
インゴットモールド鋳造:これは従来の手順です。 溶けた鉄は、取鍋を使ってインゴット型に注がれ、冷やされると、次の工程で使用される扱いやすいインゴットになります。
連続鋳造 –これは、プレートを製造するための最も近代的なプロセスです。 これは、非常に高品質な半製品を生産し、生産コストを下げ、製鉄所の生産性を向上させるという主な利点があります。 実際、このシステムのおかげで、インゴットモールド鋳造に比べて操作が少なく、簡単になりました。 . 圧延用の鋼材にインゴットを使用することを禁止します。 図3参照。
図No. 3:連続鋳造
連続鋳造では、転炉の内容物は、冷却された有底のインゴット型に、目的のプレートに対応する断面を持つ取鍋を用いて、規則的かつ途切れることなく注がれる。 その後、ローラーで平らにし、最後にオキシ燃料のトーチで必要な長さにカットします。 このようにして、長さ5〜20メートル、幅1メートル強、厚さ約20センチのスラブができあがる。
1.2.製造順序
図4は、ブリキ製造工場の基本的な原料となる鋼板を製造する際のさまざまな作業や段階を示したものである。
図4:スチールシートの生産
鋳塊鋳造法では、鋼を鋳塊にした後、最初に行う作業は鋳塊をスラブに圧延することです。 この操作は通常、リバーシブルの2段圧延機で行われます。 ユニバーサルタイプと呼ばれるものは、インゴットの4つの面を同時に加工する横方向のシリンダーやローラーを備えており、この段階でインゴットを軸上で回転させる作業が不要になります。
この作業の最終製品であるスラブの厚さは125~230mmで、最終的に必要とされるブリキ板のおおよその幅であり、長さは元のインゴットのサイズに依存します。
連続鋳造とインゴット圧延の両方で生成されたスラブは、熱間圧延のために準備されます。
熱間圧延はその次の段階であるが、通常は中間段階があり、板の冷却・保管、選別工程、表面処理(スカーフィング)、圧延に適した温度への加熱などが行われる。 この中間段階をなくすには、非常に精密なプログラミングと、スラブに欠陥がないことを保証する非常に高い技術力が必要です。 図5は、熱間圧延の各段階を示したものです。
図No.5:熱間圧延工程
この表面処理は、「デスケーリングマシン」と呼ばれる装置で行われます。この装置では、板に低い圧延圧力をかけて酸化鉄や不純物を除去し、高圧水の作用で酸化鉄や不純物を除去します。 プレートは880℃の温度に加熱される。この酸化物の層は、シリンダーの急速な摩耗、金属の溝、酸化物の付着、その他の製造上の欠陥(破損、滑り、折り目…)の原因となり、積層体を損傷するため、除去する必要があります。
熱間圧延機では、厚さ約2mmの連続した帯状にします。 通常、荒削りの部分と仕上げの部分の2つのセクションで構成されています。 設置場所の容量などに応じて、連続タイプやリバーシブルタイプなどがあります。
のです。 なんぱ線 通常、4~6箱で構成され、1箱あたり25~50%の初期板厚を削減します。その ゴールデンタイム は4~7箱で、やはり1箱あたり25~30%厚みが薄くなりますが、最後の1箱は10%しか薄くなりません。 この操作の最高速度は、100km/hまで可能です。 出口では、材料は850℃になっています。これをウォーターカーテンで590℃まで冷却し、コイルを形成します。
生産されたコイルは、冷間圧延の前に、酸洗と潤滑剤の塗布が必要です。 この作業は通常、高温の希硫酸(100℃近く)を入れたタンクを次々に設置し、洗浄、乾燥、パーム油など冷間圧延に適した潤滑油を塗布して行われる。 通常、 酸洗ラインには円形カッターが装備されており、エッジをカットすることで、冷間還元や冷間圧延に適したエッジを確保し、得られるブリキの最大幅を設定するとともに、経済的にも最良の結果が得られるようにします。 図6参照。
図6:ベーススチールの冷間圧延、アニール、スキンパッシング
次の作業は 冷間圧延で、これは連続式(タンデム式)またはリバーシブル式の圧延機で行われます。 この作業には潤滑油や冷却剤が使用され、最終的な厚さに非常に近いものとなります。 そのため、製造するブリキの最終サイズに応じて、1.8mmまたは2mmから約0.15mm~0.3mmのサイズに縮小します。
得られたコイルは、非常に硬くて応力の高い材料でできており、必要な加工性を与えるためには、鋼の再結晶を引き起こすような処理が必要です。 この処理は「アニール」と呼ばれ、金属が酸化しないように還元性のある雰囲気(窒素と水素の混合ガス)で加熱するもので、連続的に行うもの(連続アニール)と、バッチ式のアニール炉で行うもの(バッチアニール)がある。
連続焼鈍:ストリップは630℃の温度の炉内を循環し、材料の各ポイントは最低1.5分間炉内に留まる。 連続焼鈍には、さまざまなメリットとデメリットがあります。
優位性があります。
– 製造 “過程 “における材料の削減
– 製造リードタイムの短縮
– 製造する製品の品質向上。
o コイルの全長にわたって一定の連続した加熱が行われるため、機械的特性がより均質になる。
o ファストサイクルにより、微細な等軸結晶粒が生成されるため、等方性金属となり、降伏強度の向上など、優れた機械的特性が得られる。
o 耐腐食性の向上。 高速サイクルでは、ベースアニールやベルアニールのように、炭素、マンガン、リンなどの元素が素材の表面に移動することはありません。
o 炭素やマンガンなどの硬化性元素の含有量が少ないMRタイプの鋼組成を使用することができます。…. (連続焼鈍=炭素0.08%、ベース焼鈍=炭素0.10/0.13%)で、溶接や特殊加工などの作業に適しています。
デメリットです。
– ものづくり。
o 連続するコイル間の幅の最大変動は50mm程度、厚さの最大変動は10%程度であるため、注文のスケジューリングが困難である。
o 繊細なラインガイダンス。 オーブン内でベルトが切れるリスク 重要な停車駅です。 焼鈍炉の温度でのストリップの降伏強さは低い(約30N/mm2)。
o ラインストップの不可能性
– 使う。
o 微細な結晶化により、延性が低く、異方性の弱い金属が生成され、深絞りができなくなる。
o リューダーラインの存在によるリスク。
ベルでのアニール:積層された数個のコイルをベルで覆い、温度680℃の還元性雰囲気の中で、加熱32時間、ベルの下で170℃まで冷却34時間、外気で加速冷却19時間に分けて85時間以上行う。 図7参照
図7:ベルアニーリング工程のイメージ図。
いずれの場合も、以前に使用した潤滑剤や冷却剤の残留物をあらかじめ除去しておくことが重要である。 その方法は、アニールの種類に応じて、通常は95℃に加熱した脱脂槽などの電気化学的な方法や、両面をブラッシングする機械的な方法が用いられる。
その後、焼戻し、表面処理、仕上げ(テンパーローリング、スキンパス)が行われる。 これは還元や圧延によって行われ、潤滑剤を使わずに非常に軽く、通常は厚さが2%を超えることはありません。 そのために、2つのボックスで構成された圧延機を使用します。 確立された圧力と牽引力の影響下でロールの間を通過するストリップは、構造の表面的な変更を受け、表面層の硬度の増加を達成しますが、内部の柔らかさは維持されます。
つまり、この作業により、圧延機ボックスで使用されるロールの粗さに応じて、ストリップに所望の硬さ、良好な平坦性、材料の表面仕上げが得られるのである。 この圧延による箱の円筒部の表面仕上げと、錫メッキ作業後の最終的な再溶解を組み合わせることで、ブリキの異なる表面仕上げを実現しています。 仕上げの種類は主に
ブライト仕上げ:この仕上げのためには、シリンダーの鏡面研磨が不可欠です。 さらに、錫メッキのリフローを施す必要があります。このような仕上げは、石材仕上げと並んで最も求められるものです。
石目調:ロールに特殊な石目調の砥石を用いて2回の研磨を行い、製品に石目調の外観を与えます。 前回同様、錫メッキを再溶解することで、輝きを確保しています。
マット仕上げ:表面の反射率が低い。 そのために、シリンダーにショットブラストを施し、錫メッキ後の再溶解作業を省略しています。
ダブル・リダクション・ブリキの場合、最終的なダウンゲージは、焼き戻し作業の代わりに、さらに約33%のダウンゲージまたは圧延を行い、その結果、表面潤滑剤を使用して同様の割合で材料を伸ばすことになります。 これにより、ブリキの厚さが薄くても高い機械的特性が得られます。
錫メッキ作業の前に、コイルの準備をするのが一般的です。 主に、エッジをカットしたり、品質の低い部分や規格外の部分を取り除いたりして、錫メッキラインに最適なサイズのコイルを形成します。
電解スズめっきでは、準備された材料は、電解洗浄、電解酸洗、スズの電着、流動溶解、不動態化処理、潤滑の各工程を連続的に通過します。 この一連の作業の後、注文されたサイズ(コイル作成時に幅を指定していたので長さ)に板状に切断し、検査、選別、梱包するか、あるいは巻いて顧客に出荷したり、別のスリッティングラインでスリットなどを行う。 梱包する前に、同じラインで素材の選定を行うのが普通です。 これらの点については、後で詳しく説明します。
1.3.- ベーススチールの組成。
ブリキの場合、基本的に母鋼は、以下のタイプの一般的な組成を持つ低炭素軟鋼です。
– カーボン 0.04~0.15 %。
– シリコン 0.08%以下
– 硫黄 0.015 – 0.05 %。
– リン 0.01~0.14 %.
– 銅 0.02~0.20%。
– マンガン 0.20 – 0.70 %.
– 窒素 0.001 – 0.025 %.
スクラップを製鋼に使用するため、ニッケル、クロム、スズなどの他の元素が含まれることがありますが、意図的に他の元素を添加することはありません。 唯一の例外は、リンと窒素で、これらは特別な特性を提供することができます。 耐食性を高めるための銅の使用や、経年変化を抑制するための一部の炭化物の使用は、使われなくなりました。
ブリキのベーススチールに及ぼす特定の元素の影響について、以下に概説します。
– 炭素:炭素は、降伏強さ、引張強さ、硬さを増加させ、伸びと延性を減少させる。 ブリキの通常の限界内では、他の元素の影響がはるかに大きいため、ブリキ含有量の変動はほとんど重要ではありません。
– シリコン:ブリキには残留元素として存在するが、ごく稀に脱酸剤として添加されることがある。 わずかに硬化し、場合によっては耐食性に悪影響を及ぼします。
– 硫黄:このタイプのスチールでは、硫黄の影響は、常に存在するマンガンによって打ち消されます。 しかし、延性、表面品質、耐食性に影響を与えるため、経済的制限の範囲内で、可能な限り削減する努力がなされています。
– 燐。硬度や耐食性に大きな影響を与える元素である。 酸による腐食の可能性がある場合には、一定の範囲内に抑える必要があり、より高い鋼の強度が求められ、腐食の危険性がない場合には含有量を増やします。
– 銅です。抵抗値を上げるといっても、通常の範囲内では効果的ではありません。 これを超えると耐大気腐食性は向上しますが、耐内部腐食性が低下する可能性があるため、ほとんどのブリキでは銅含有量の上限が規定されています。
– マンガン:ブリキ鋼の製造に使用されるが、主に硫黄を中心とした他の元素と反応して機能しなくなる。
– 窒素:ベッセマー鋼では、0.01%以上の割合で通常の構成元素であり、常に不利とされてきた。 意図的に添加することで、経年変化には影響があるものの、耐食性には大きな変化がなく、鋼の強度が大幅に向上することがわかった。 酸素プロセス(LDなど)の開発により、酸素含有量を正確にコントロールできるようになり、均一で継続的な品質が得られるようになりました。
– ニッケル:許容レベルであれば、ブリキの物理的・機械的特性に大きな影響はありませんが、化学的特性、特にある種の包装における腐食に影響を与えます。 クロムも同様である。
– スズ:この元素は鉄や鋼への溶解度が高く、第二相を形成するためには10%以上の含有率が必要である。 通常のレベルでは、金属組織に影響を与えません。 その存在は、降伏強さと引張強さを徐々に増加させ、弾性係数を減少させる。 重要なのは、銅を含む鋼に少量のスズが含まれていると、熱間加工に重大な支障をきたすことです。
鋼材製造においては、ブリキ鋼の機械的特性に及ぼす合金元素や残留元素の影響を計算するために、実用的なルールが用いられることがあります。 代表的なものにストロメイヤー指数がありますが、これは窒素分を5倍にしてリンを加え、その合計に1000を掛けて算出します。
1.4.-基本的なスチールの種類
従来、ブリキ鋼には3つの基本的なタイプがありましたが、現在の技術では古典的なタイプに収まらないこともあります。 これらは
タイプL:平炉からの冷延鋼(シェメンズ・マーティン社)。 メタロイドや微量元素の含有量が少なく、特にリンの含有量が制限されており、以下のような組成になっています。
カーボン 0.05~0.13 %。
マンガン 0.30 – 0.60 %.
硫黄 0.04 max.
リン 0.015 max.
シリコン 0.010 max.
銅 0.06 max.
ニッケル 0.04 max.
クロム 0.06 max.
モリブデン 0.05 max.
砒素 0.02 max.
窒素 0.02 max.
腐食性の高い製品に対して高い耐性が要求される場合に使用されます。
タイプMR:最も多く使用されています。 従来のものと同じ起源で、冷間圧延され、中程度の腐食性の製品に使用されます。 彼らの分析は
カーボン 0.05~0.15 %。
マンガン 0.30 – 0.60 %.
硫黄 0.04 max.
リン 0.020max.
シリコン 0.010 max.
銅 0.20 max.
タイプMC:ベッセマー転炉やシーメンス・マーティン炉で作られた鋼で、容器の強度や内容物の腐食性が低い場合に使用される。 彼らの標準的な分析は以下の通りです。
カーボン 0.05~0.15 %。
マンガン 0.25 – 0.60 %。
硫黄 0.04 max.
リン 0.03 – 0.15 %.
シリコン 0.010 max.
銅 0.20 max.
また、深絞り加工の特殊なケースに使用されるアルミニウム焼入れ・焼戻しを施したタイプDなどの特殊鋼もあります。
一般的にヨーロッパのメーカーは、特殊なブリキ生産を排除して、費用対効果の高い競争力のあるプロセスを見つけようとする必要に迫られているため、問題を単純化しようとします。
また、耐食性の観点からは、鋼の表面も重要であり、これは焼鈍時の雰囲気の種類にも依存する。 窒素、水素、二酸化炭素、水蒸気を含む雰囲気では、4~8%の水素を含む乾燥窒素よりも耐性の低いブリキができます。 また、溶解した錫イオンは一般的に、ある種の製品によるブリキの腐食を抑制する効果があります。
2.ティンニング(TINNING)
錫
この材料がブリキの製造を目的としている場合、食品と長時間接触することが想定されるため、不純物に関して一定の要件を満たす必要があります。 米国材料試験協会(ASTM)では、錫の含有量の最小値を次の5つのグループに分類しています:グレードAA=錫99,98%、A=99,80%、B=99,7%、C-1=99,0%、C-2=99,0%。 ブリキの製造に最低限指定されているのはグレードAで、その分析結果は以下の通りです。
錫(最小)99.80%。
アンチモン 0.04 %。
砒素 0.04 %.
Bismuth 0.015 % Bismuth 0.015 % Bismuth 0.015 % Bismuth 0.015
銅 0.03% 銅 0.03% 銅 0.03% 銅 0.03% 銅 0.03% 銅 0.03% 銅 0.03
鉄 0.015 % 鉄 0.015 % 鉄 0.015 % 鉄 0.015 % 鉄 0.015
鉛 0.05 % 鉛 0.05
ニッケル、コバルト 0.015 %。
銀 0.01 % 銀 0.01 % 銀 0.01 % 銀 0.01 % 銀 0.01 % 銀 0.01
硫黄 0.003 % 硫黄 0.003 % 硫黄 0.003 % 硫黄 0.003
亜鉛 0.001 % 亜鉛 0.001 % 亜鉛 0.001 % 亜鉛 0.001 % 亜鉛 0.001
カドミウム 0.001 %.
アルミニウム 0.001 % アルミニウム 0.001 % アルミニウム 0.001 % アルミニウム 0.001 % アルミニウム 0.001
- 電解スズめっき
この錫メッキプロセスの開発は、錫メッキ業界にとって最も重要なステップの一つでした。 連続した細長い帯に錫を電気めっきする技術は1930年にドイツで始まったが、第二次世界大戦中には錫の不足からアメリカを中心に集中的に開発されたものである。
電解ブリキが従来のコークスブリキやホットブリキから市場を奪ったのには、技術的・経済的な理由がいくつかある。 中でも重要なのは、錫の蒸着量と厚さの均一性を正確にコントロールすることです。 もう一つは、シートの両面に異なる厚さの錫メッキを施す「差動電解ブリキ」の存在です。
ベースとなる鋼の焼き戻し作業ですでに示したように、電解ブリキは様々な仕上げで製造することができますが、最も一般的なのは3つの仕上げです。 最も一般的な「ブライト」、ベースとなるスチールを表面を荒くして錫を再溶解しない「マット」、そして最後に、上記と同じ仕上げで錫を再溶解することで、光沢はあるが反射しない「ストーン」があります。
製造方法には基本的に酸とアルカリまたは塩基性プロセスの2種類があるが、後者にはハロゲンの水平ラインとアルカリまたは垂直ラインの2つのバリエーションがあり、広く使われている。 電解質としてフルオロホウ酸塩を使用する第4の方法がありますが、ほとんど使用されていません。
酸性プロセスを採用しているラインでは、電解ブリキの割合が最も高い。 フェロスタンと呼ばれることが多いのは、かつてU.S.スチールがブリキで登録した名前であり、その後、その技術を世界中に広めたからである。
電解質はあらゆるプロセスの中で最もデリケートな部分です。 例えば、酸ラインでは、スタナス塩を酸で溶かしたものですが、電解質としての性能は、酸化を避ける、コンパクトでファジーでない堆積物の形成を促す、濡れ性を改善する、という3つの主要な目的を持った様々な添加剤が使用されているかどうかで決まります。
アルカリ性電解液を使用する古典的な利点としては、電解液がシンプルで扱いやすく、鉄に対して非腐食性であるため、装置の初期費用を抑えることができます。 準備の部分もよりシンプルになっています。
酸性ラインは、アルカリ性ラインに比べてスズめっきに使用する電流が少なく、アノードの表面積が少なくて済み、電着での電気効率が高いという利点があります。 しかし、アルカリラインでは、より優れた耐食性の特性を持つブリキが得られます。
大まかに言うと、3種類のラインは以下の部分で構成されています。
巻き戻し
準備
錫メッキ
仕上がり
切断・巻取り・包装
エントリーまたは巻き戻しセクションには、黒板コイルを扱うために必要な設備があり、各コイルの始点と終点をカットしたり、あるコイルの終点と次のコイルの始点を電気溶接したりして、ラインを連続的に送り出すことができます。 ガイドローラー、フィードローラー、テンションローラーなど。
巻き戻し部と準備部の間には、前の巻き戻し部でリールの交換やスプライシングが行われている間にラインを送る、一定量のウェブを蓄積することを目的としたブラックシート・ウェブを保管する装置がある。 いくつかのタイプがあり、主にウェルタイプと「アコーディオン」タイプがあります。
準備編では、洗浄(脱脂)と酸洗の2つの目的があります。 1つ目は、潤滑油や冷却剤などでベルト表面に残留した成分をすべて除去すること、2つ目は、ベルトの両面に付着した酸化鉄を除去することです。
処理は、ウォータージェットやスチーム洗浄を交互に行いながら、化学的または電気化学的な浴場で連続して行われます。 レイアウトや種類は回線によって異なります。 例えば、脱脂は通常、洗剤やアルカリ性の溶液で行われますが、このようなラインでは、錫メッキ部で自動的に脱脂が行われるため、脱脂作業が不要または削減されます。
錫メッキ部は工程ごとに全く異なり、ハロゲンプロセスでは、ストリップが通常3段階でフラットに移動するため、最も面積が大きく、他の2つのシステムでは、正弦波や蛇行に沿って移動します。
図No.9:錫メッキライン、電解槽、アノード
錫メッキの前に、差動ブリキに対応するマーキングを黒板ストリップに行いますが、製造されるのがこのタイプのブリキである場合には、これらのマーキングはベースのスチールになります。 メーカーによっては、後にブリキに問題が発生した場合にメーカーを特定できるように、ベースとなるスチールにマークを付けることもあります。 これらのマークは、そのままでは葉の上には見えないので、実験室で見つけなければなりません。
仕上げの部分には、再溶解、不動態化、潤滑などのさまざまな工程があります。
再溶解の目的は、ブリキに光沢のある仕上げを施すことです。ブリキの単純な電着では、マットな外観のミクロの荒れた表面になります。 しかし、このステップは、腐食性の要素と接触することを意図したブリキには基本的に重要です。 再溶解時に鉄-錫合金の層が形成されますが、その生成が早いため、厚さは非常に薄くなります。 したがって、鉄-錫合金の層を必要とする用途には、再溶解を行っていないダルブリキを使用してはいけません。
不動態化は、電解ブリキの特徴です。 特に下地の場合は、製造時だけでなく、その後のワニス塗りなどの作業時にも、酸化を防ぐために保護層を設けることが望ましい。 また、化学的にリソグラフィーやニスの塗布に適しており、一定の保護硬度を持つ表面を提供する必要があります。 パッシベーションはこの点をカバーするためのもので、基本的には酸化クロム層を形成することである。 使用される方法は、様々な化学的または電気化学的な方法で、それぞれ特別な特性を得るために設計されています。 通常、USSという頭文字と3桁の数字で知られており、1桁目は溶液の種類(1=クロム酸、2=リン酸クロム、3=重クロム酸ナトリウム、4=炭酸ナトリウム)、2桁目は溶液中のブリキの極性(0=非電解、1=カソード、2=カソード/アノード)、3桁目は使用する電流のレベルをほぼ示している。
不動態化には3つの基本的なタイプがあります。
–パッシベーション300:重クロム酸ナトリウムの溶液に浸して、化学的に酸化クロムの層を生成することで得られる。 ワニスの密着性の観点からも良い結果が得られます。 硫化に対する保護機能は弱い。 しかし、このパッシベーションは不安定である。 時間の経過とともに効果が減少する
–パッシベーション 311重クロム酸ナトリウムの浴中でクロムと酸化クロムの層を電気化学的に析出させることで得られる。最もよく使われるパッシベーションである。また、300パッシベーションよりも経時安定性が高く、リソグラフィシステムの経時安定性と密着性を両立させることができます。
–パッシベーション312:311と同じシステムで実現。 実際には311のパッシベーションを強化したものです。 主に、肉類、スープ、犬や猫の製品など、硫黄を含む製品に耐える必要のあるブリキ板に使用されています。
さまざまな不動態化処理は、ワニスや溶接などの接着に影響を与えるだけでなく、ブリキが腐食性製品や硫黄化合物と接触することで、さまざまな形態の攻撃や汚れが発生します。 美しさや見せ方の観点からも、例えばコンデンスミルクのように、このディテールは重要です。
最後に、仕上げ部門では、潤滑作業を行います。 この潤滑剤の目的は、ブリキ自体を保護することではなく、不動態化を保護することであり、ブリキの特性を打ち消さないように、非常に軽いものであるため、スプレーや浸漬による塗布も可能であるが、最も一般的な塗布方法は電着によるものである。 通常は、綿実油、セバシン酸ジオクチル、セバシン酸ジブチルの3種類のオイルが使用されています。 通常の潤滑油の量は0.005grs/m2のオーダーです。 潤滑油の乾燥は、通常、蒸気や熱風コイルを使って行われます。
ラインの最後の部分は、ラインの種類(酸、…)ではなく、最終製品と得られる生産性によって形成されます。 生産がコイルのみの場合は、切断は行われませんが、コイルの交換を可能にするウェブストレージ装置があります。 カットシートのみの生産であれば、記憶装置は必要ありません。 切断作業では、表面の欠陥の選別を行いますが、この制御はラインスピードの関係であまり効率的ではないため、得られた製品は「未選別」と分類されます。 第一」と「第二」を分けたい場合は、選択ラインの補助サービスを利用する必要があります。 このセクションでは、規格外のシートとピンホールのシートが分けられています。 コイルが納品されるときには、この分離をしないのが普通で、歩留まりが悪くなるので、カットするときにこの操作をするのはお客様の自由です。 選別されていない」という品質は、電解スズめっきラインの通常の製品として定義されています。
電解研磨ラインには非常に複雑な付帯設備が搭載されており、実際にはラインそのものよりも複雑で、氷山のように沈んだ部分が見えなくなることがあります。 電気・電子機器、制御装置、ポンプ、電解液タンク、浄化装置、水・蒸気システム、空気などは非常に重要で、通常は地下に設置されます。 搭載されている電力も非常に強いものです。
錫メッキ時のストリップ速度は、電解に使用できる電流、電解液の状態、材料のサイズと厚さ、希望する錫の析出量などの要素によって決まる。
3.- TFS
ブリキの価格が上昇し、ブリキの供給が危うくなった結果、ブリキの代替品であるTFS(クロムプレート)が前世紀最後の3分の1に開発された。 この素材はすぐに興味を引き、時間とともに大きくなっていきました。 その利点は、蓋、底、金具、深絞りの容器の製造に完全に有効な選択肢であり、ブリキよりもわずかに安いということです。
TFSはブリキと同じ支持体であるスチールでできています。 しかし、保護を確保するためには、電解析出法による錫の薄層とパッシベーション膜ではなく、クロムと酸化クロムの混合皮膜が必要である。
鉄鋼業界では、ブリキ板やクロム板を、それほど複雑ではない一連の変更を、適度な時間で行うことができる混合プラントでTFSを生産するのが一般的です。 クロムの塗布も電解方式で行われます。 図10は、クロムメッキの板金を生産するラインの特殊部分です。
これを得るためのプロセスについては、すでに示したように、ベースとなるスチールはブリキと同じであり、コーティングラインはブリキメッキと類似した順序をたどるので、詳細は省く。
最後に、ブリキ鋼の製造、ブリキ自体の製造、TFSなどの他の代替材料の開発、そしてもちろんその使用において、大手包装会社が重要な役割を果たしていることは特筆に値するでしょう。
0コメント